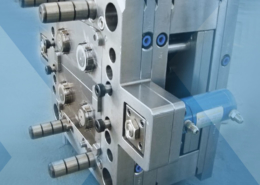
Understanding Injection Tooling: Revolutionizing Manufacturing
Author:gly Date: 2024-06-08
Injection tooling stands as a cornerstone in modern manufacturing, revolutionizing the way we produce various products across industries. From automotive components to household appliances, injection tooling plays a pivotal role in shaping our everyday lives. This article aims to delve into the intricacies of injection tooling, shedding light on its significance, components, applications, and future prospects.
1. Origins and Evolution
Injection tooling traces its origins back to the mid-20th century, with the advent of plastic injection molding. Initially developed as a method to produce simple, small-scale items, such as buttons and combs, injection molding has evolved into a sophisticated process capable of producing intricate components with high precision and efficiency.
The evolution of injection tooling has been fueled by advancements in materials science, engineering, and computer-aided design (CAD) technologies. Today, manufacturers can create molds with complex geometries and tight tolerances, enabling the production of diverse products with unmatched consistency and quality.
2. Key Components
Injection tooling comprises several essential components, each playing a crucial role in the molding process. These include:
Mold Cavity
The mold cavity defines the shape and dimensions of the final product. It is meticulously designed to accommodate the desired geometry, ensuring precise replication during the molding process.
Injection Unit
The injection unit is responsible for melting and injecting the raw material, typically plastic resin, into the mold cavity. It consists of a barrel, screw, and nozzle, working in tandem to deliver the molten material with accuracy and consistency.
Clamping System
The clamping system securely holds the mold in place during the injection process. It exerts pressure to keep the mold closed and withstand the forces generated by the injection of molten material.
3. Applications Across Industries
Injection tooling finds extensive applications across various industries, including:
Automotive
In the automotive industry, injection tooling is used to produce components such as bumpers, dashboards, and interior trim panels. Its ability to manufacture lightweight yet durable parts makes it indispensable in vehicle design and manufacturing.
Medical
In the medical sector, injection tooling is utilized to fabricate precision components for devices such as syringes, IV catheters, and surgical instruments. The sterile and biocompatible nature of injection-molded plastics makes them ideal for medical applications.
Consumer Electronics
Consumer electronics rely on injection tooling for the production of casings, buttons, and connectors. The process enables manufacturers to achieve sleek designs and ergonomic features, enhancing the user experience.
4. Future Directions and Challenges
Looking ahead, the future of injection tooling holds promising opportunities alongside certain challenges. Advancements in materials science, including the development of biodegradable and recycled plastics, are poised to enhance sustainability in manufacturing.
However, the industry also faces challenges such as rising material costs, stringent regulatory requirements, and the need for skilled labor. Addressing these challenges will require collaborative efforts from stakeholders across the supply chain.
In conclusion, injection tooling stands as a cornerstone of modern manufacturing, driving innovation and efficiency across industries. By understanding its origins, key components, applications, and future prospects, we can appreciate its profound impact on our daily lives and pave the way for continued advancements in the field.
GETTING A QUOTE WITH LK-MOULD IS FREE AND SIMPLE.
FIND MORE OF OUR SERVICES:
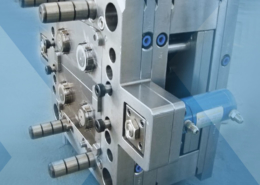
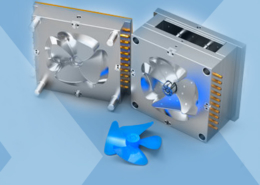
Plastic Molding

Rapid Prototyping
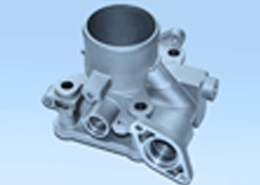
Pressure Die Casting
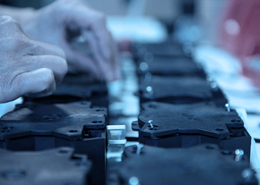
Parts Assembly
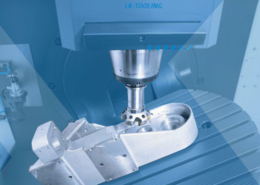