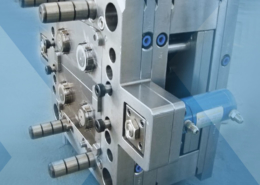
Exploring the Evolution of Injection Moulding Solutions
Author:gly Date: 2024-06-08
Introduction
Injection moulding solutions represent a cornerstone of modern manufacturing, offering unparalleled precision, efficiency, and versatility across diverse industries. From automotive components to consumer electronics, their widespread adoption underscores their indispensability in contemporary production processes. This article delves into the multifaceted world of injection moulding solutions, elucidating their evolution, applications, and future prospects, aiming to captivate readers' interest and provide comprehensive insights into their significance and implications.
Evolution of Technology
The evolution of injection moulding technology has been marked by continuous innovation and refinement, driven by the quest for enhanced efficiency, precision, and sustainability. Traditional injection moulding processes have evolved to incorporate advanced features such as multi-cavity molds, hot runner systems, and automated control systems, enabling higher production rates, reduced cycle times, and improved part quality.
Moreover, the integration of additive manufacturing techniques, such as 3D printing, with injection moulding processes has revolutionized product development and customization, facilitating rapid prototyping, design iteration, and on-demand manufacturing. These advancements underscore the transformative potential of injection moulding solutions in shaping the future of manufacturing.
Applications Across Industries
Injection moulding solutions find diverse applications across a myriad of industries, ranging from automotive and aerospace to healthcare and consumer goods. In the automotive sector, injection moulding is utilized for manufacturing intricate components such as interior trim, exterior panels, and engine parts, owing to its ability to produce lightweight, durable, and cost-effective parts at scale.
Similarly, in the healthcare industry, injection moulding plays a pivotal role in producing medical devices, implants, and disposable consumables, adhering to stringent regulatory standards and ensuring biocompatibility, sterilizability, and precision. Moreover, injection moulding solutions cater to the burgeoning demand for consumer electronics, enabling the production of sleek, functional, and lightweight components with intricate geometries and superior surface finish.
Material Innovation and Sustainability
Material selection is paramount in injection moulding, influencing the performance, aesthetics, and environmental footprint of manufactured parts. The advent of advanced polymers, composites, and bio-based materials has expanded the scope of injection moulding solutions, offering enhanced mechanical properties, chemical resistance, and sustainability.
Furthermore, the pursuit of sustainability has spurred the development of biodegradable and recycled materials compatible with injection moulding processes, mitigating the environmental impact of plastic waste and fostering a circular economy paradigm. By embracing eco-friendly materials and adopting energy-efficient manufacturing practices, stakeholders can enhance the sustainability profile of injection moulding solutions while meeting evolving regulatory requirements and consumer preferences.
Future Outlook and Emerging Trends
Looking ahead, injection moulding solutions are poised to witness continued evolution and proliferation, fueled by technological advancements, market demands, and regulatory imperatives. Industry 4.0 technologies, including artificial intelligence, internet of things (IoT), and digital twin simulations, promise to revolutionize injection moulding operations, enabling real-time monitoring, predictive maintenance, and adaptive manufacturing.
Moreover, the rise of customization and personalization trends is driving the adoption of agile manufacturing paradigms, wherein injection moulding solutions play a central role in enabling mass customization, just-in-time production, and decentralized manufacturing networks. By embracing digitalization, automation, and sustainability-driven innovation, stakeholders can unlock new opportunities for growth, resilience, and competitiveness in the dynamic landscape of injection moulding solutions.
Conclusion
Injection moulding solutions have emerged as a linchpin of modern manufacturing, offering unparalleled precision, efficiency, and versatility across diverse industries. By tracing the evolution of technology, exploring applications across industries, delving into material innovation and sustainability, and envisioning future trends, this article elucidates the transformative potential of injection moulding solutions in shaping the future of manufacturing. By embracing technological advancements, sustainability imperatives, and market opportunities, stakeholders can harness the full potential of injection moulding solutions to drive innovation, enhance competitiveness, and foster sustainable development in the global marketplace.
GETTING A QUOTE WITH LK-MOULD IS FREE AND SIMPLE.
FIND MORE OF OUR SERVICES:
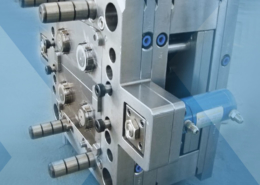
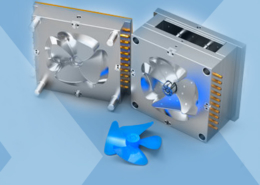
Plastic Molding

Rapid Prototyping
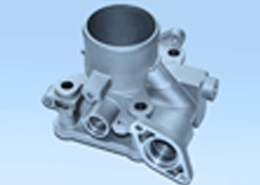
Pressure Die Casting
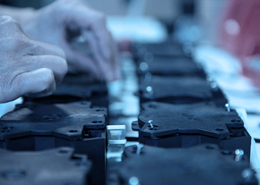
Parts Assembly
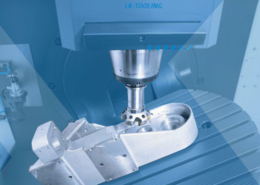