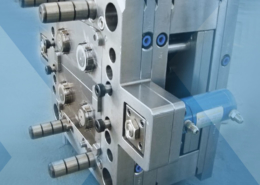
Exploring the Advancements in Hard Plastic Molds
Author:gly Date: 2024-06-08
Hard plastic molds stand as pillars of modern manufacturing, facilitating the production of intricate components across various industries. This article aims to delve into the world of hard plastic molds, captivating readers with their significance, applications, advancements, and future potential.
Introduction to Hard Plastic Molds
Hard plastic molds are precision tools used in the injection molding process to shape molten plastic into specific forms. They are crafted from durable materials such as steel or aluminum and are designed to withstand high temperatures and pressures. These molds serve as the foundation of countless products, ranging from consumer goods and automotive parts to medical devices and electronics.
The Evolution of Hard Plastic Molds
1. Traditional Manufacturing Methods
Historically, hard plastic molds were predominantly crafted using conventional machining techniques such as milling and grinding. While effective, these methods were time-consuming and limited in their ability to produce complex geometries.
2. Advances in CAD/CAM Technology
The advent of computer-aided design (CAD) and computer-aided manufacturing (CAM) revolutionized the production of hard plastic molds. These technologies enable precise modeling and simulation of mold designs, facilitating faster prototyping and optimization of tooling configurations.
3. Additive Manufacturing
Recent years have witnessed the emergence of additive manufacturing techniques such as 3D printing for producing hard plastic molds. This approach offers greater design freedom, reduced lead times, and cost-effective production of customized molds, especially for low-volume production runs and rapid prototyping.
Applications of Hard Plastic Molds
1. Automotive Industry
Hard plastic molds play a critical role in the automotive sector, where they are used to manufacture interior and exterior components such as dashboards, door panels, and bumpers. The ability to produce durable, high-quality parts with tight tolerances ensures the reliability and performance of vehicles.
2. Consumer Goods
In the realm of consumer goods, hard plastic molds are utilized to create a myriad of products, including household appliances, toys, and packaging containers. The efficiency and repeatability of injection molding processes enable mass production of items with consistent quality and cost-effectiveness.
3. Medical Devices
The healthcare industry relies on hard plastic molds for the fabrication of medical devices and equipment, ranging from syringes and surgical instruments to implantable devices and diagnostic tools. The precision and biocompatibility of molded components are critical for ensuring patient safety and efficacy.
Challenges and Future Directions
Despite the advancements in hard plastic mold manufacturing, challenges persist, including the need for enhanced materials, improved surface finishes, and sustainable production practices. Future research efforts may focus on exploring novel materials, optimizing mold design algorithms, and integrating smart technologies for real-time monitoring and maintenance.
Conclusion
Hard plastic molds represent the cornerstone of modern manufacturing, driving innovation and enabling the production of diverse products across industries. From automotive components to medical devices, these precision tools continue to shape the world around us. By embracing advancements in technology and addressing ongoing challenges, the future of hard plastic molds holds immense promise, paving the way for continued progress and innovation in manufacturing processes.
GETTING A QUOTE WITH LK-MOULD IS FREE AND SIMPLE.
FIND MORE OF OUR SERVICES:
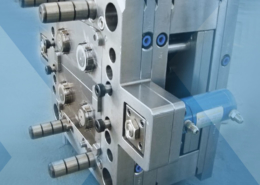
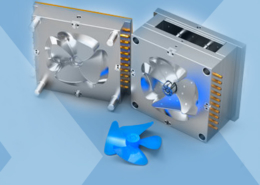
Plastic Molding

Rapid Prototyping
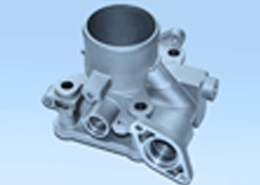
Pressure Die Casting
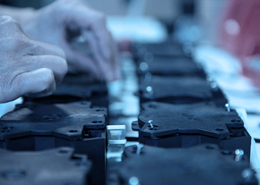
Parts Assembly
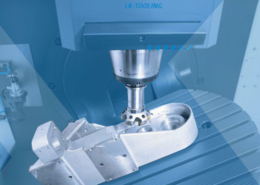