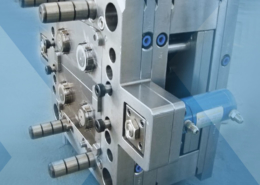
Exploring the World of HDPE Molding
Author:gly Date: 2024-06-08
HDPE (High-Density Polyethylene) molding is a fascinating process that plays a pivotal role in the manufacturing of various products, ranging from bottles and containers to toys and automotive components. This article aims to delve into the realm of HDPE molding, providing readers with an insight into its intricacies and significance.
Introduction: Unveiling the Potential of HDPE Molding
HDPE molding involves the transformation of high-density polyethylene resin into a wide array of products through processes such as injection molding, blow molding, and extrusion. The versatility and durability of HDPE make it a preferred choice for manufacturers seeking to create robust and cost-effective solutions for diverse applications.
The Versatility of HDPE
Adaptability Across Industries
HDPE's versatility extends across industries, including packaging, construction, healthcare, and automotive. Its ability to withstand high temperatures, chemicals, and impact makes it suitable for an array of applications, from food packaging to automotive fuel tanks.
Customization and Design Flexibility
One of the key advantages of HDPE molding is its inherent design flexibility. Manufacturers can easily customize products to meet specific requirements, whether it's creating intricate shapes, incorporating ergonomic features, or optimizing for functionality and aesthetics.
Environmental Sustainability
In an era where sustainability is paramount, HDPE stands out as a recyclable and eco-friendly material. Its lightweight nature reduces transportation emissions, while its recyclability ensures a closed-loop system, minimizing environmental impact and promoting a circular economy.
Technological Advancements in HDPE Molding
Advanced Molding Techniques
Technological advancements have revolutionized the HDPE molding process, leading to increased efficiency, precision, and quality. Innovations such as multi-cavity molds, in-mold labeling, and robotic automation have streamlined production, reducing cycle times and enhancing product consistency.
Material Innovations
The development of new HDPE grades and additives has expanded the material's capabilities, allowing for enhanced performance and properties. Additives such as antioxidants, UV stabilizers, and impact modifiers improve resistance to environmental factors, extending product lifespan and durability.
Simulation and Prototyping
Simulation tools enable manufacturers to simulate the molding process virtually, allowing for the optimization of mold design and process parameters before physical production. This reduces time-to-market and minimizes the need for costly trial-and-error iterations, resulting in significant cost savings and improved product quality.
Challenges and Future Directions
Addressing Material Waste
Despite its recyclability, HDPE molding still generates waste during production and post-consumer use. Future research efforts should focus on developing innovative recycling technologies and sustainable alternatives to minimize waste generation and promote a circular economy.
Enhancing Energy Efficiency
Energy consumption is another area of concern in HDPE molding. Continued efforts to optimize manufacturing processes, adopt energy-efficient equipment, and explore alternative energy sources will be crucial for reducing the environmental footprint of HDPE molding operations.
Advancing Sustainable Practices
Sustainability will remain a key driver in the future of HDPE molding. Manufacturers must prioritize sustainable practices throughout the entire product lifecycle, from material sourcing and production to end-of-life disposal, to minimize environmental impact and meet evolving consumer demands.
Conclusion
HDPE molding represents a dynamic and evolving field that intersects technology, innovation, and sustainability. From its versatility and design flexibility to technological advancements and environmental considerations, HDPE molding continues to shape the future of manufacturing. By addressing challenges and embracing sustainable practices, the industry can unlock new opportunities and pave the way for a more sustainable and resilient future.
GETTING A QUOTE WITH LK-MOULD IS FREE AND SIMPLE.
FIND MORE OF OUR SERVICES:
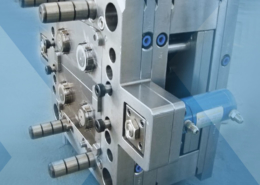
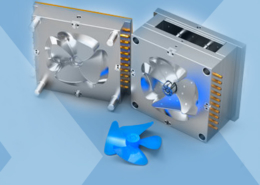
Plastic Molding

Rapid Prototyping
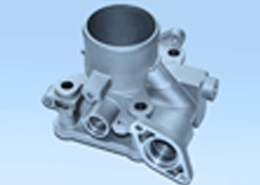
Pressure Die Casting
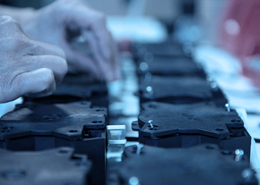
Parts Assembly
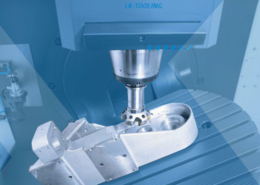