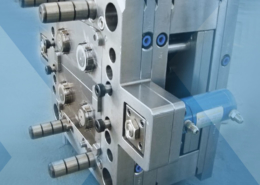
Gas Assist Molding: Innovating Plastic Injection
Author:gly Date: 2024-06-08
Gas assist molding stands as a groundbreaking technique in the realm of plastic injection molding, offering unique advantages and capabilities that traditional methods cannot match. In this comprehensive exploration, we unveil the intricacies of gas assist molding, from its inception to its modern applications and future prospects.
Introduction to Gas Assist Molding
Gas assist molding is a specialized injection molding process that utilizes inert gas, typically nitrogen, to hollow out thick-walled plastic parts, thereby reducing material usage, cycle time, and production costs. Unlike conventional molding techniques, which rely solely on the injection of molten plastic into a closed mold cavity, gas assist molding introduces pressurized gas into the core of the part during the molding cycle. This gas displaces the molten plastic, forming a hollow section within the part while maintaining structural integrity and surface finish.
Gas assist molding presents a versatile solution for manufacturing complex geometries and large parts with uniform wall thickness, addressing challenges such as sink marks, warpage, and excessive material consumption. By leveraging the benefits of gas-assisted technology, manufacturers can achieve lightweight, high-strength components with enhanced aesthetics and functionality.
Advantages of Gas Assist Molding
Gas assist molding offers a multitude of advantages over traditional molding methods, making it a preferred choice for various applications. Firstly, the hollowing effect achieved through gas assist molding reduces material usage by up to 50%, resulting in significant cost savings and material waste reduction. Moreover, the elimination of sink marks and reduction in part warpage enhance the cosmetic appearance and dimensional accuracy of molded components.
Furthermore, gas assist molding facilitates the production of large, thick-walled parts with uniform wall thickness, improving structural integrity and strength-to-weight ratio. This capability is particularly advantageous in industries such as automotive, furniture, and consumer goods, where lightweight yet durable components are paramount.
Process and Equipment
The gas assist molding process involves several key stages, including mold filling, gas injection, packing, and cooling. During mold filling, molten plastic is injected into the mold cavity under high pressure, ensuring complete cavity fill and uniform distribution. Subsequently, pressurized gas is introduced into the core of the part, displacing the molten plastic and forming the hollow section.
Specialized gas assist molding machines equipped with gas injection units and control systems are essential for executing the process with precision and efficiency. These machines feature integrated gas channels within the mold, allowing for precise gas delivery and control throughout the molding cycle. Additionally, advanced monitoring and feedback systems enable real-time adjustments to optimize part quality and production efficiency.
Applications and Industry Impact
Gas assist molding finds widespread applications across various industries, ranging from automotive and aerospace to consumer electronics and household appliances. In the automotive sector, gas assist molding is utilized for the production of structural components, such as instrument panels, door panels, and seat frames, where lightweighting and strength are critical.
Moreover, in consumer electronics, gas assist molding enables the fabrication of sleek, lightweight enclosures and housings for electronic devices, enhancing both aesthetics and functionality. The versatility and cost-effectiveness of gas assist molding make it an attractive option for manufacturers seeking to optimize part design, performance, and production efficiency.
Challenges and Future Directions
While gas assist molding offers numerous advantages, certain challenges remain, including process complexity, mold design considerations, and gas handling requirements. Addressing these challenges requires ongoing research and development efforts focused on enhancing process robustness, design guidelines, and material compatibility.
Looking ahead, the future of gas assist molding lies in further integration with digital technologies, such as predictive modeling, simulation, and real-time monitoring. By leveraging these tools, manufacturers can optimize process parameters, minimize waste, and accelerate time-to-market for new products.
In conclusion, gas assist molding represents a transformative approach to plastic injection molding, offering unparalleled capabilities and benefits for a wide range of industries. With continued innovation and collaboration, gas assist molding will continue to shape the landscape of manufacturing, driving efficiency, sustainability, and product innovation into the future.
GETTING A QUOTE WITH LK-MOULD IS FREE AND SIMPLE.
FIND MORE OF OUR SERVICES:
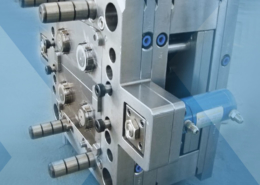
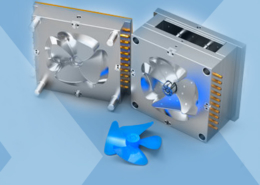
Plastic Molding

Rapid Prototyping
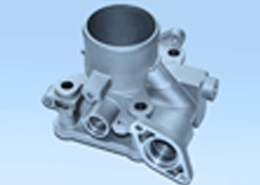
Pressure Die Casting
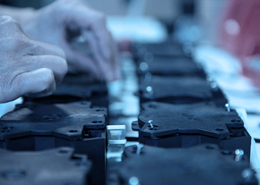
Parts Assembly
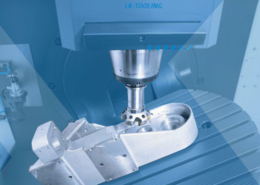