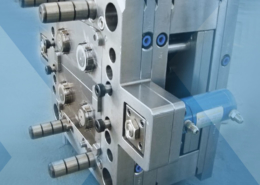
Exploring the Dynamics of Extrusion and Injection Moulding
Author:gly Date: 2024-06-08
Introduction
Extrusion and injection moulding are two fundamental processes in the realm of plastic manufacturing, each offering unique advantages and applications. These techniques play pivotal roles in shaping everyday objects, from packaging materials to automotive components, underscoring their significance in modern industry. This article aims to delve into the intricacies of extrusion and injection moulding, elucidating their principles, applications, and comparative advantages, thereby captivating readers' interest and providing comprehensive insights into their pivotal role in contemporary manufacturing.
Understanding Extrusion Moulding
Extrusion moulding is a versatile manufacturing process that involves forcing molten plastic through a die to create continuous profiles with uniform cross-sections. This technique finds widespread application in producing a myriad of products, including pipes, tubes, films, and profiles, owing to its high productivity, low cost, and scalability. The process begins with feeding thermoplastic pellets into an extruder, where they are melted and conveyed through a heated barrel before being extruded through a die to form the desired shape.
Furthermore, advancements in extrusion technology, such as co-extrusion and in-line processing, enable the production of complex structures with multiple layers, functional additives, and precise dimensions. The versatility and efficiency of extrusion moulding render it indispensable in various industries, ranging from construction and packaging to agriculture and automotive.
Exploring Injection Moulding
Injection moulding, on the other hand, is a highly versatile and precise manufacturing process that involves injecting molten plastic into a mold cavity under high pressure. This technique facilitates the production of intricate and dimensionally accurate components with excellent surface finish and mechanical properties. Injection moulding caters to diverse applications, ranging from consumer goods and electronics to medical devices and automotive parts, owing to its ability to produce complex shapes with high repeatability and efficiency.
Moreover, the advent of advanced materials, such as engineering thermoplastics and biodegradable polymers, expands the scope of injection moulding solutions, offering enhanced performance, sustainability, and regulatory compliance. The continuous evolution of injection moulding technology underscores its pivotal role in driving innovation and competitiveness in modern manufacturing.
Comparative Analysis and Applications
Extrusion and injection moulding represent two distinct yet complementary manufacturing processes, each offering unique advantages and applications. Extrusion moulding excels in producing continuous profiles and long-length products with consistent cross-sections, making it ideal for applications such as pipes, tubing, and sheeting. Conversely, injection moulding specializes in manufacturing discrete components with intricate geometries and precise dimensions, catering to diverse industries ranging from automotive and aerospace to healthcare and consumer electronics.
Furthermore, hybrid processes combining extrusion and injection moulding techniques, such as overmoulding and co-injection, enable the production of complex assemblies with integrated functionalities and reduced assembly costs. Understanding the comparative strengths and limitations of extrusion and injection moulding is crucial for optimizing product design, material selection, and manufacturing efficiency across various applications.
Future Directions and Innovations
Looking ahead, advancements in extrusion and injection moulding technologies are poised to revolutionize the landscape of plastic manufacturing, driven by the quest for sustainability, customization, and digitalization. The integration of Industry 4.0 principles, such as digital twin simulations, predictive maintenance, and real-time monitoring, promises to enhance productivity, quality, and flexibility in extrusion and injection moulding operations.
Moreover, the development of bio-based polymers, recycling technologies, and closed-loop systems aims to mitigate the environmental impact of plastic manufacturing while fostering a circular economy paradigm. By embracing innovation, collaboration, and sustainability-driven initiatives, stakeholders can unlock new opportunities for growth, resilience, and sustainability in the dynamic realm of extrusion and injection moulding.
Conclusion
Extrusion and injection moulding are integral pillars of modern manufacturing, offering unparalleled versatility, efficiency, and precision across diverse industries. By elucidating the principles, applications, and comparative advantages of these techniques, this article underscores their pivotal role in shaping the contemporary landscape of plastic manufacturing. By embracing technological advancements, sustainability imperatives, and collaborative partnerships, stakeholders can harness the transformative potential of extrusion and injection moulding to drive innovation, competitiveness, and sustainability in the global marketplace.
GETTING A QUOTE WITH LK-MOULD IS FREE AND SIMPLE.
FIND MORE OF OUR SERVICES:
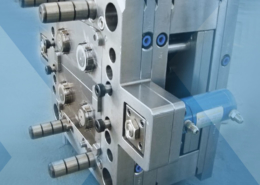
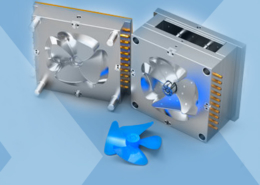
Plastic Molding

Rapid Prototyping
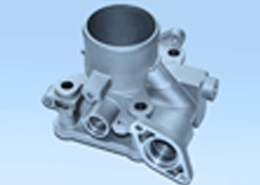
Pressure Die Casting
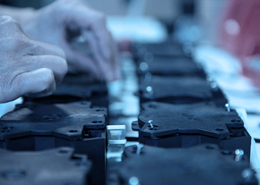
Parts Assembly
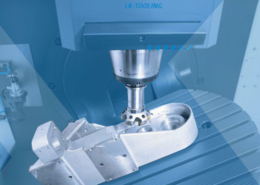