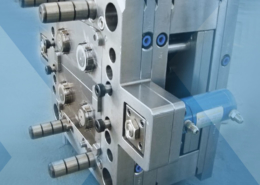
Making contact lens moulds – how do they do it? - soft plastic mould
Author:gly Date: 2024-09-30
The flagship all-electric range from TM Robotics is the SXIII all-electric series from Shibaura Machine. Shibaura Machine is the new name for Toshiba Machine — the Japanese manufacturer of industrial robots and injection mould machines. The SXIII range boasts faster injection speeds, enhanced sustainability and a streamlined design when compared to its hydraulic predecessors. What’s more, despite the perception of higher costs for all-electric machines, this range can improve cost efficiency by lowering the cost-per-part.
“AEST is good at engineering, designing and fabricating things,” said Manusos, “so it made sense to build equipment to recycle plastic. A few years ago, our students built a plastic shredder using the Precious Plastics plans; the recent grant dollars were used, in part, to help upgrade that machine. These grant dollars were also used to support the construction of an extruder, which takes the chipped-up plastic and extrudes it into a long filament, similar to a weed whacker trimmer line. This project was largely the work of one of our students who was using the project for his Honors Thesis. This machine, when complete can be used to create the aw filament needed to feed our 3D printers, or the resulting filament can be chipped up and used in our injection molding machines.”
This was demonstrated by TM Robotics’ customer Lotan, a manufacturer of plastic containers based in Leicestershire, UK. Lotan’s production facility exclusively uses all-electric injection mould machines from Shibaura Machine. The SXIII provides significantly faster injection speeds than traditional moulding equipment, providing 35% faster cycle times than conventional hydraulic servo IMMs.
Nigel Smith, managing director of TM Robotics, the international distribution partner of Shibaura Machine and the UK and Ireland distributor of its injection mould machines, explores the changing landscape of plastic's injection moulding sector and argues the case for investment in new technologies, both for better operational efficiency and improved sustainability.
Manusos says the students will get to decide what they will make from recycled plastic this semester. It could be Millersville keychains or maybe Millersville branded coasters. He says they hope to sell the products at the bookstore on campus. Another thing they’ve considered is selling shredded plastic by the pound.
The recycling process will be presented to Millersville’s Council of Trustees at their Sept. 21 meeting. Millersville students Lauren Coca and Jackson Harral will present with Manusos at the meeting.
Manusos applied for and received a $2,500 Positive Energy Fund grant from the University to purchase materials to build an extruder, an injection molder and to upgrade an existing plastics shredder. This will allow the department to scale up its capacity as the MU Sustainability Club scales up its collection.
Injection moulding applications have long played a key part in the UK’s manufacturing industry, producing everything from medical components, automotive parts, food containers, packaging items and much more. Traditionally, our manufacturers have relied on hydraulic-powered injection moulding machines in their operations. However, the industry is now at a crossroads, faced with the imperative to embrace technological advancements for sustainability and cost-effectiveness.
Manusos hopes to grow the program by building additional equipment and working with the Sustainability Club on campus so they can take in plastic from across the campus, from offices, residence halls, the cafeteria, etc., and make it into something useful.
It takes a lot of coordination, smarts and a rather large shredder to take post-consumer plastic, like plastic water or soda bottles, and repurpose them into something more permanent. But that’s exactly what’s happening at Millersville University.
This is impressive and meaningful work — much needed on campus and in all communities. Thank you for leading this effort!
The impetus behind the recycling project was to give the students an authentic experience in plastics recycling. “Often times we hear that plastic waste is not being handled properly and can end up in our local watershed. The Ocean Cleanup project is a non-profit organization that develops and scales technologies to rid the world’s oceans of plastic,” says Manusos. “The Ocean Cleanup and movements like “Precious Plastic” have many YouTube videos on how to reuse plastic in a meaningful way rather than throwing it away and having it land in the ocean. Precious Plastics also offers guidance, and schematics on building equipment for plastics recycling, opening a local recycling hub, and running an online store devoted to promoting the sale of plastic goods or equipment needed for these processes.”
The injection moulding process is responsible for up to 90 per cent of the Global Warming Potential (GWP) in the entire mould lifecycle. Recognising this, TM Robotics has championed investment in all-electric injection mould machines to replace older, more energy-intensive models.
“Currently, our students bring in their own plastic waste to be sorted, cleaned, shredded and turned into something different,” explains Dominick Manusos, assistant professor in Applied Engineering, Safety & Technology. “We take the plastic waste, sort it by type and color, clean and wash it, shred it, put it through any number of machines and processes to make something useful.”
Due to this lack of uptake, the UK industry is missing some of the potential benefits of industrial robots, including improved productivity, efficiency and throughput. As a primary distributor of Shibaura Machine robots in the UK, the TM Robotics team has spotted opportunities for the injection moulding sector to reap the rewards of robotic automation.
Another area of debate in the injection moulding world is robot integration. The UK seriously lags behind other developed countries for its number of robot installations. That’s not just for the world of injection moulding, but in the UK manufacturing sphere more widely. In fact, the International Federation of Robotics (IFR) reports that the UK has just 101 robots per 10,000 employees — rookie numbers compared to competitors in the US, China and Germany.
This is great news! I would love to see you make benches and tables from plastics on campus! This campus needs to recycle! All trash bins on campus should have a recylce bin next to it! Thank you for all you are doing!! Go Ville!!
“In addition to making durable items, students have the ethical implications for thinking about what they’re doing, what they’re making and how it will be used,” says Manusos. “And they use critical thinking to figure it out from start to finish – how the durable goods should be designed, produced, and put into the hands of others. What we do with the products when they are no longer useful and whether we can design products that can be recycled again are also important considerations.
One notable observation is the prevalence of hydraulic legacy equipment that is still being used by UK manufacturers. The TM Robotics’ injection moulding servicing department has witnessed this first-hand and regularly visits manufacturing sites to service and maintain Shibaura Machine’s own hydraulic injection mould machines — some of which have been in action for up to three decades. On one hand, it is a testament to the resilience of these machines, but the industry must consider the environmental downsides of this ageing equipment.
The most obvious application for robots in mould machine shops is for the loading and unloading of injection mould machines. However, many end users currently have relatively low robotic ability, having traditionally chosen Cartesian X-Y gantry style robots to unload injection moulding machines.
There are over 5,800 companies operating in the UK plastics industry, contributing £25 billion to our economy each year. As a key player in Britain’s manufacturing sector, injection mould shops must embrace technological advancements in injection moulding machinery and accompanying automation for improved profit, productivity and sustainability.
Students get involved in the project from across campus. They may talk about the project in an AEST class, while others have done independent studies or honors theses or become involved through a club. Manusos says the SME club (Society of Manufacturing Engineers, is one of the most involved student organizations with the project.
“These will be items made out of 100% recycled plastic,” says Manusos. “It’s from plastic from our campus that would have been tossed. It’s a great way to promote sustainability – making a durable item from something that people likely would have thrown away.”
Harral says the experience has been a good one for him, “Recycling opens up a huge number of doors in the fields of engineering and art. Personally, I have found huge capabilities in using collected plastic and reconstituting it into an engineering medium, rather than simply putting it in a bin, only to maybe get recycled at a plant.”
“Our efforts are going toward using 100% of recycled plastic collected locally to make new products, tools, and art. This includes things such as cutting boards, keychains, bowls, plates, frisbees, tool handles and so much more,” says Harral.
GETTING A QUOTE WITH LK-MOULD IS FREE AND SIMPLE.
FIND MORE OF OUR SERVICES:
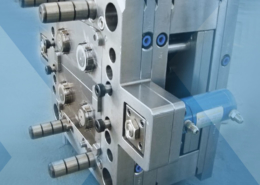
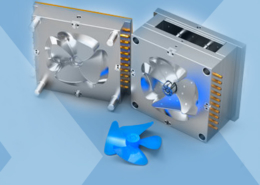
Plastic Molding

Rapid Prototyping
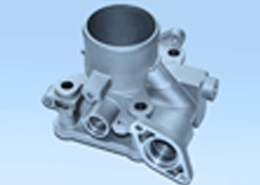
Pressure Die Casting
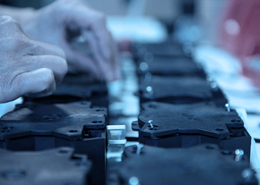
Parts Assembly
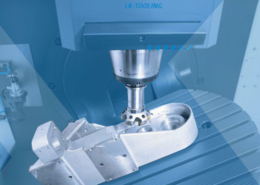