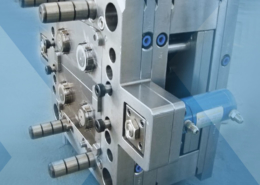
Making contact lens moulds – how do they do it? - soft plastic mould
Author:gly Date: 2024-09-30
In addition to injection molding, the material can also be used for injection stretch blow molding, something that was previously believed to be difficult using conventional light diffusion PP resin molding compounds. It can also be injection stretch blow molded in wall thicknesses of as thin as 0.5 mm with 10% thickness tolerance, something else that was reportedly previously unachievable. The MFR of the compound is 25 g/10 min.
“AddiFab has built Freeform Injection Molding to break key injection moulding constraints,” commented Staal. “FIM lets the injection moulder create injection-moulded objects with the same design freedom offered by conventional 3D printing. At the same time, we have brought 3D printing lead-times and start-up costs to the injection moulding industry, without compromising on the choice of materials. We look forward to working with MCAM on adding entirely new dimensions to the fields of generative design and topology optimisation, and to redefining the way metal replacement materials are using in weight reductions.”
Diffusion plates are generally positioned adjacent to LED lighting sources in order to maintain uniform luminance. Currently, these diffusion plates are primarily molded of polycarbonate or acrylic resin. However, in the diversified environment of LED light sources, further light resistance, chemical resistance, resistance to high temperature and high humidity, and moreover lighter weight have been sought. Panasonic’s PP compound reportedly provides a solution to these issues and extends product life while contributing to lightweighting: the material is 30% lighter than polycarbonate.
The company has already commenced commercial production of the material, which is both lightweight and delivers a higher brightness for LED lighting. Panasonic claims Full Bright is the first material applicable for injection stretch blow molding processes, and it enables the formation of complex shapes, thereby contributing to greater product design freedom for customers.
For Mitsubishi Chemical, it has been seen as a method of harnessing some of the benefits of 3D printing, without waiting for technology to develop enough to process some of its higher-performing materials. It led the company to provide financial support to AddiFab in the autumn of 2019 and less than a year later the companies have expanded their collaboration.
“We quickly realised that Freeform Injection Molding would allow us to offer entirely new levels of light-weighting and we have been working with AddiFab to bring our KyronMAX materials onto the FIM platform,” added Randy White, the company’s Chief Innovations Officer. “When we were able to drive an 8,000-pound pick-up truck onto a KyronMAX lattice weighing only 70 grams, we knew we were onto something.”
Target applications for the material include automotive interior lighting, outdoor sign boards, store lighting, water-related lighting, and digital signage.
Mitsubishi Chemical Advanced Materials (MCAM) is to begin offering a Freeform Injection Molding (FIM) service in collaboration with AddiFab later this year.
The company will provide this service from its facilities in Mesa, Arizona; Tielt, Belgium; and Tokyo and Nagoya in Japan. It represents a significant expansion of the relationship between Mitsubishi and AddiFab, which began in 2019 with the former’s venture arm, Diamond Edge Ventures, investing in the latter.
“When we were able to drive an 8,000-pound pick-up truck onto a KyronMAX lattice weighing only 70 grams, we knew we were onto something.”
Freeform Injection Molding is AddiFab’s flagship technology, based on 3D printed injection mould inserts and designed to allow users to access the design capabilities of 3D printing while maintaining the performance of traditionally manufactured parts. It also gives manufacturers the ability to prototype components in the same material they intend to move into manufacturing with.
Speaking to TCT last year, AddiFab CEO Lasse Staal referenced the opportunities available via its relationship with Mitsubishi, stating a ‘very interesting journey’ lay ahead. With this announcement, the partners have made the first step in that journey, and will give customers in three continents access to FIM and thousands of Mitsubishi Chemical materials.
In terms of light resistance, the PP compound’s discoloration as recorded in UV tests is equivalent to ten years of use in outdoor environments.
Japanese electronics firm Panasonic Corporation has developed a polypropylene (PP) compound that exhibits light diffusion properties called Full Bright. The material can reportedly extend the operational life of LEDs.
GETTING A QUOTE WITH LK-MOULD IS FREE AND SIMPLE.
FIND MORE OF OUR SERVICES:
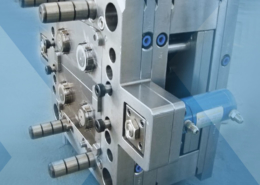
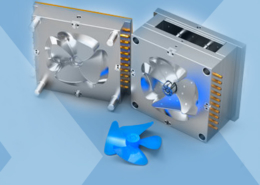
Plastic Molding

Rapid Prototyping
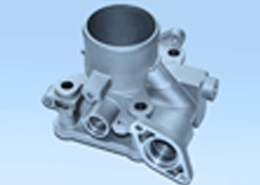
Pressure Die Casting
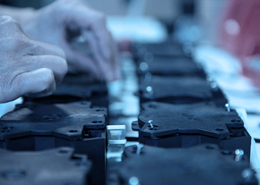
Parts Assembly
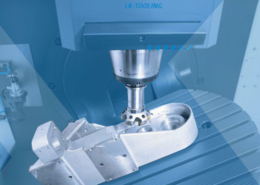