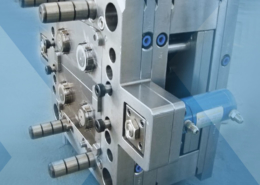
Exploring the Innovations in Back Injection Molding
Author:gly Date: 2024-06-08
Introduction
Back injection molding, also known as two-shot injection molding or overmolding, is a specialized process that enables the creation of complex plastic parts with multiple materials or colors. This innovative technique has gained significant traction in various industries due to its ability to enhance product functionality, aesthetics, and performance. In this article, we delve into the world of back injection molding, exploring its applications, benefits, and technological advancements that have propelled its popularity.
Understanding Back Injection Molding
Back injection molding involves the injection of one material (typically thermoplastic) over another substrate material to create a single integrated component. This process enables the incorporation of multiple materials, colors, textures, or functionalities into a single part, offering designers and manufacturers unprecedented flexibility and creativity in product design.
Applications and Benefits
Enhanced Product Aesthetics:
One of the key benefits of back injection molding is its ability to enhance the visual appeal of products by incorporating different colors, finishes, or textures into a single part. This capability is particularly valuable in industries such as consumer electronics, automotive, and consumer goods, where aesthetics play a crucial role in product differentiation.
Improved Product Functionality:
Back injection molding allows for the integration of functional features, such as soft-touch grips, ergonomic contours, or tactile surfaces, directly into the molded part. By combining different materials with varying properties, manufacturers can enhance product functionality, comfort, and usability, leading to improved customer satisfaction and market competitiveness.
Cost and Time Savings:
Despite its complexity, back injection molding can result in cost and time savings compared to traditional manufacturing methods. By consolidating multiple manufacturing steps into a single process, such as molding, assembly, and finishing, it reduces production lead times, labor costs, and material waste, resulting in overall efficiency gains.
Technological Advancements
Advanced Molding Equipment:
Technological advancements in injection molding machinery, such as multi-component injection molding machines and robotic automation systems, have significantly enhanced the capabilities and precision of back injection molding processes. These sophisticated systems enable precise control over material placement, injection timing, and part quality, ensuring consistent and high-quality production.
Innovative Materials and Additives:
The development of new materials and additives tailored for back injection molding has expanded the range of applications and possibilities in product design. From thermoplastic elastomers (TPEs) for soft-touch grips to specialty resins for chemical resistance, manufacturers have access to a wide array of materials that offer superior performance and aesthetics.
Simulation and Optimization Tools:
Simulation software and optimization tools have become indispensable for designing and refining back injection molding processes. These tools allow engineers to simulate material flow, mold filling, cooling, and part shrinkage, optimizing process parameters and reducing the risk of defects or production issues before actual production begins.
Challenges and Future Directions
Design Complexity and Integration:
As back injection molding enables increasingly complex part designs and material combinations, manufacturers face challenges in design optimization, material selection, and process integration. Overcoming these challenges requires collaboration between designers, engineers, and material suppliers to ensure seamless integration and optimal performance.
Sustainability and Material Recycling:
While back injection molding offers numerous benefits in terms of product functionality and aesthetics, there is a growing emphasis on sustainability and environmental responsibility in manufacturing. Future developments in back injection molding may focus on using recycled materials, reducing waste, and adopting eco-friendly processes to minimize the environmental impact of production.
Integration of Industry 4.0 Technologies:
The integration of Industry 4.0 technologies, such as Internet of Things (IoT), artificial intelligence (AI), and digital twins, holds promise for optimizing back injection molding processes and enhancing production efficiency. By leveraging real-time data analytics, predictive maintenance, and remote monitoring, manufacturers can achieve greater process control, reliability, and productivity.
Conclusion
In conclusion, back injection molding represents a versatile and innovative manufacturing technique that offers unique opportunities for product designers and manufacturers. With its ability to create complex parts with multiple materials or colors, enhance product aesthetics and functionality, and achieve cost and time savings, it has become increasingly popular across various industries. However, as the demand for customization, sustainability, and efficiency continues to grow, future developments in back injection molding will likely focus on addressing challenges such as design complexity, sustainability, and the integration of advanced technologies. By staying at the forefront of innovation and embracing emerging trends, manufacturers can unlock new possibilities and maintain a competitive edge in the dynamic world of back injection molding.
GETTING A QUOTE WITH LK-MOULD IS FREE AND SIMPLE.
FIND MORE OF OUR SERVICES:
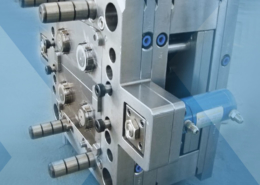
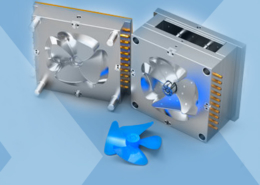
Plastic Molding

Rapid Prototyping
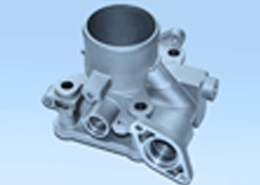
Pressure Die Casting
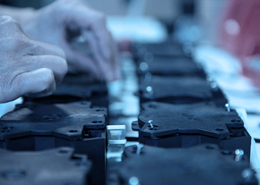
Parts Assembly
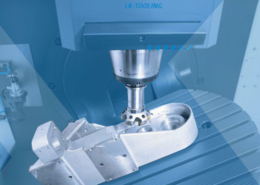