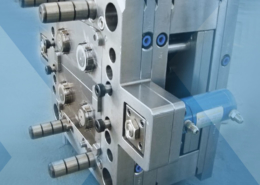
Exploring the World of Benchtop Injection Molding
Author:gly Date: 2024-06-08
Introduction
Benchtop injection molding is a fascinating technology that brings the power of traditional industrial injection molding to smaller-scale operations. With its versatility and efficiency, it has garnered significant interest across various industries, from prototyping to small-scale production. In this article, we delve into the intricacies of benchtop injection molding, exploring its capabilities, applications, and future prospects.
Overview of Benchtop Injection Molding
Benchtop injection molding, also known as desktop injection molding, refers to the process of injecting molten material into a mold cavity under high pressure to produce precision parts. Unlike traditional injection molding machines, which are large and costly, benchtop models are compact, affordable, and suitable for small-scale production or prototyping purposes. These machines typically operate on a smaller scale but maintain the precision and quality associated with industrial-grade molding.
Advantages and Applications
Bridging Prototyping and Production:
One of the key advantages of benchtop injection molding is its ability to bridge the gap between prototyping and production. By allowing manufacturers to create small batches of parts quickly and cost-effectively, it facilitates rapid iteration and testing during the product development phase.
Cost-Effectiveness:
Compared to traditional injection molding machines, benchtop models offer a more cost-effective solution for small-scale production. They require less space, energy, and material, making them ideal for startups, small businesses, and research labs with limited resources.
Versatility Across Industries:
Benchtop injection molding finds applications across a wide range of industries, including automotive, aerospace, medical, consumer goods, and electronics. From manufacturing intricate components to producing custom-designed prototypes, its versatility makes it a valuable tool in various sectors.
Technical Considerations
Machine Specifications:
Benchtop injection molding machines come in various sizes and configurations, each tailored to specific production needs. Factors such as clamping force, shot size, injection pressure, and mold capacity influence machine selection and performance.
Material Selection:
Choosing the right material is critical for achieving desired part properties and performance. Benchtop injection molding supports a wide range of thermoplastic materials, including ABS, PC, PP, and Nylon, allowing manufacturers to customize parts according to their requirements.
Process Optimization:
Optimizing the injection molding process involves fine-tuning parameters such as temperature, pressure, injection speed, and cooling time to ensure consistent part quality and production efficiency. Advanced software and automation technologies aid in process monitoring and optimization.
Challenges and Future Directions
Complexity of Parts:
While benchtop injection molding excels at producing small to medium-sized parts with high precision, it may face challenges when manufacturing complex geometries or large-scale components. Addressing these challenges requires advancements in mold design, material science, and process optimization.
Sustainability and Material Recycling:
As environmental concerns continue to rise, there is a growing emphasis on sustainable manufacturing practices and material recycling in the injection molding industry. Future developments in benchtop injection molding may focus on using recycled materials, reducing waste, and minimizing environmental impact.
Integration of Additive Manufacturing:
The integration of additive manufacturing technologies, such as 3D printing, with benchtop injection molding holds promise for streamlining the product development process and creating more complex and customized parts. This convergence of technologies may lead to innovative solutions and new opportunities in manufacturing.
Conclusion
In conclusion, benchtop injection molding offers a versatile and cost-effective solution for small-scale production, prototyping, and research applications. Its ability to produce precision parts with minimal resources makes it an invaluable tool across various industries. While facing challenges such as part complexity and sustainability concerns, ongoing advancements in machine technology, material science, and process optimization continue to expand the capabilities and potential of benchtop injection molding. As we look towards the future, integrating additive manufacturing, embracing sustainable practices, and pushing the boundaries of innovation will shape the evolution of this exciting technology.
GETTING A QUOTE WITH LK-MOULD IS FREE AND SIMPLE.
FIND MORE OF OUR SERVICES:
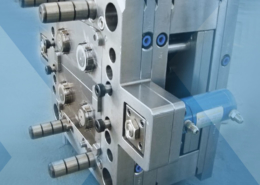
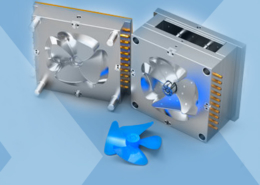
Plastic Molding

Rapid Prototyping
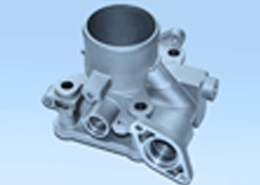
Pressure Die Casting
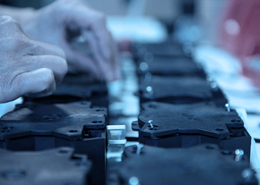
Parts Assembly
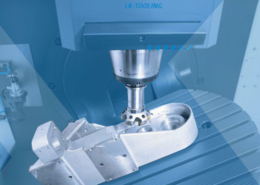