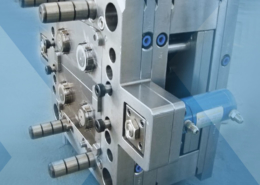
Advancements in Automotive Injection Molding: Revolutionizing Vehicle Manufactur
Author:gly Date: 2024-06-08
Introduction:
Automotive injection molding stands as a cornerstone in the evolution of vehicle manufacturing, shaping the way modern automobiles are produced. This cutting-edge process entails injecting molten material into a mold cavity at high pressure, resulting in intricate and precise components. Its significance lies in its ability to streamline production, enhance design flexibility, and ensure unparalleled product consistency. In this article, we delve into the multifaceted realm of automotive injection molding, exploring its various aspects and elucidating its pivotal role in the automotive industry.
1. Material Selection and Customization
The versatility of automotive injection molding begins with the selection and customization of materials. Manufacturers have a plethora of options ranging from traditional polymers to advanced composites, each offering distinct properties tailored to specific automotive applications. Polypropylene, for instance, dominates the realm of interior components due to its lightweight nature and excellent impact resistance. In contrast, engineering-grade thermoplastics like ABS and PC/ABS blends find prominence in exterior body panels owing to their superior strength and weatherability.
Furthermore, the advent of innovative material additives and reinforcements has propelled customization to unprecedented heights. Fillers such as glass fibers and carbon nanotubes augment mechanical properties, while additives like UV stabilizers and flame retardants enhance durability and safety. This amalgamation of material science and injection molding technology empowers manufacturers to achieve optimal performance while adhering to stringent regulatory standards.
2. Design Optimization and Complexity
The evolution of automotive design has been intricately intertwined with advancements in injection molding technology. The ability to produce complex geometries with unparalleled precision has revolutionized component design, enabling engineers to push the boundaries of innovation. From intricate interior trim panels to aerodynamically optimized exterior fascias, injection molding facilitates the realization of diverse design visions.
Moreover, the integration of computer-aided design (CAD) and simulation tools has further catalyzed design optimization. Finite element analysis (FEA) and mold flow simulation allow for comprehensive evaluation of part manufacturability and performance, mitigating potential defects and enhancing production efficiency. This seamless synergy between design and manufacturing fosters a culture of continuous improvement, driving the automotive industry towards greater innovation and competitiveness.
3. Sustainability and Environmental Impact
In an era characterized by growing environmental consciousness, automotive injection molding has emerged as a catalyst for sustainability within the industry. The adoption of bio-based and recycled materials, coupled with innovative recycling processes, has significantly reduced the carbon footprint associated with vehicle production. Bio-plastics derived from renewable sources offer a viable alternative to traditional petroleum-based polymers, mitigating reliance on finite fossil fuel reserves.
Furthermore, advancements in process efficiency and waste management have further bolstered the sustainability credentials of injection molding. Closed-loop recycling systems minimize material wastage, while energy-efficient machinery and optimized production workflows reduce overall resource consumption. By embracing a holistic approach to sustainability, automotive manufacturers can not only mitigate environmental impact but also enhance brand reputation and customer loyalty.
4. Quality Assurance and Manufacturing Efficiency
Quality assurance stands as a cornerstone of automotive manufacturing, with injection molding playing a pivotal role in ensuring product excellence. The inherent repeatability and precision of the injection molding process minimize variability, resulting in consistent part quality and dimensional accuracy. Advanced inspection techniques, such as computer vision systems and automated gauging, further enhance quality control capabilities, detecting defects with unparalleled sensitivity.
Moreover, the seamless integration of automation and Industry 4.0 technologies has ushered in a new era of manufacturing efficiency. Robotics and IoT-enabled devices optimize production workflows, reducing cycle times and enhancing throughput. Real-time data analytics facilitate predictive maintenance and process optimization, mitigating downtime and maximizing equipment utilization. By embracing these transformative technologies, automotive manufacturers can achieve unparalleled levels of productivity and competitiveness in the global market.
Conclusion:
In conclusion, automotive injection molding stands as a beacon of innovation and efficiency in the realm of vehicle manufacturing. From material selection and design optimization to sustainability and quality assurance, its impact resonates across every facet of the automotive industry. By embracing technological advancements and fostering a culture of continuous improvement, automotive manufacturers can navigate the evolving landscape of mobility with confidence and resilience. As we look towards the future, the potential for further advancements in injection molding technology remains boundless, promising a future where automotive manufacturing transcends conventional boundaries to achieve new heights of excellence.
GETTING A QUOTE WITH LK-MOULD IS FREE AND SIMPLE.
FIND MORE OF OUR SERVICES:
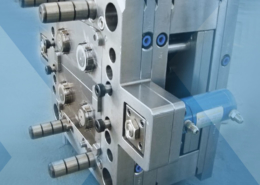
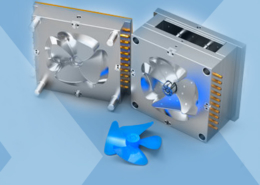
Plastic Molding

Rapid Prototyping
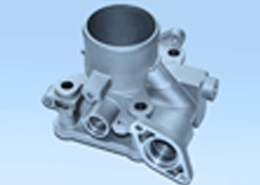
Pressure Die Casting
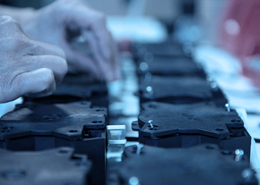
Parts Assembly
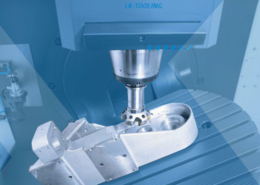