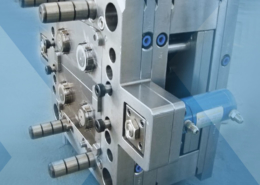
Understanding ABS Moulding: Revolutionizing Manufacturing Processes
Author:gly Date: 2024-06-08
ABS moulding, a cornerstone of modern manufacturing, stands at the intersection of innovation and efficiency. With its diverse applications and unparalleled versatility, ABS moulding has become indispensable across various industries. This article delves into the intricacies of ABS moulding, exploring its significance, applications, advantages, and future prospects.
Introduction to ABS Moulding
ABS (Acrylonitrile Butadiene Styrene) moulding is a manufacturing process that involves the injection of molten ABS resin into a mould cavity. Upon cooling and solidification, the mould releases the formed ABS component. This technique is widely employed in industries ranging from automotive and electronics to consumer goods and medical devices.
Advantages of ABS Moulding
1. Versatility
ABS moulding offers unparalleled versatility, accommodating complex geometries and intricate designs with ease. Its ability to incorporate various additives enables the customization of properties such as strength, rigidity, and flame resistance, making it suitable for diverse applications.
2. Cost-effectiveness
One of the key advantages of ABS moulding is its cost-effectiveness. The efficiency of the injection moulding process coupled with the affordability of ABS resin makes it an economical choice for large-scale production. Moreover, its durability and long-term performance contribute to reduced maintenance costs.
3. Impact Resistance
ABS moulded components exhibit excellent impact resistance, making them ideal for applications where durability is paramount. This property, combined with ABS's ability to withstand harsh environmental conditions, ensures the reliability of products in demanding settings.
Applications of ABS Moulding
1. Automotive Industry
In the automotive sector, ABS moulding is extensively utilized for manufacturing interior and exterior components such as dashboards, panels, and bumpers. Its lightweight nature, coupled with high impact resistance, enhances fuel efficiency and passenger safety.
2. Electronics
ABS moulding plays a crucial role in the production of electronic devices and appliances. From housings for smartphones and laptops to enclosures for electronic circuitry, ABS components offer a balance of aesthetics, functionality, and durability demanded by the electronics industry.
3. Consumer Goods
The consumer goods industry relies on ABS moulding for manufacturing a wide range of products, including toys, kitchenware, and home appliances. ABS's ability to replicate intricate details and vibrant colors enhances the appeal of consumer goods while ensuring structural integrity.
Future Outlook and Recommendations
As technology continues to advance, the future of ABS moulding holds immense promise. Research into bio-based and recyclable ABS resins aims to mitigate environmental concerns associated with traditional petroleum-based plastics. Additionally, advancements in additive manufacturing techniques such as 3D printing open new avenues for ABS moulding, facilitating rapid prototyping and customization.
In conclusion, ABS moulding stands as a testament to the ingenuity of modern manufacturing processes. Its versatility, cost-effectiveness, and impact resistance make it indispensable across various industries. Looking ahead, continued innovation and sustainability efforts will further elevate ABS moulding as a cornerstone of the manufacturing landscape.
By comprehensively understanding ABS moulding and embracing emerging technologies, manufacturers can unlock new possibilities and drive progress towards a more efficient and sustainable future.
GETTING A QUOTE WITH LK-MOULD IS FREE AND SIMPLE.
FIND MORE OF OUR SERVICES:
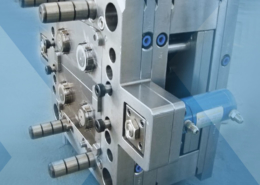
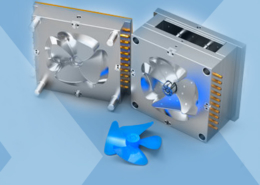
Plastic Molding

Rapid Prototyping
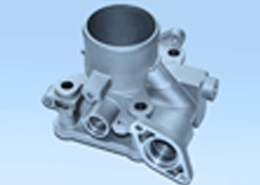
Pressure Die Casting
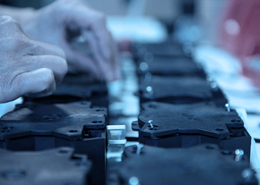
Parts Assembly
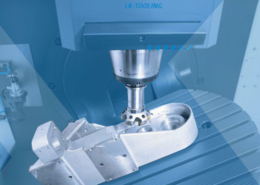