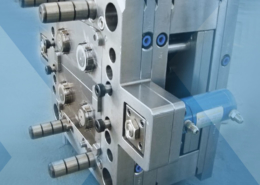
Exploring the World of ABS Injection Molding
Author:gly Date: 2024-06-08
ABS injection molding stands as a cornerstone in the realm of plastic manufacturing, offering a multitude of applications across diverse industries. This article aims to provide an in-depth exploration of ABS injection molding, shedding light on its significance, techniques, applications, challenges, and future prospects.
Introduction to ABS Injection Molding
ABS (Acrylonitrile Butadiene Styrene) injection molding is a widely utilized manufacturing process that involves the injection of molten ABS resin into a mould cavity to create complex plastic components. Renowned for its versatility, durability, and cost-effectiveness, ABS has become a preferred material for a myriad of applications, ranging from automotive parts and consumer electronics to household appliances and toys.
Techniques and Processes
ABS injection molding encompasses a series of intricate techniques and processes to achieve optimal results. The process typically involves heating ABS resin pellets to their melting point and injecting the molten material into a mould cavity under high pressure. Factors such as temperature control, injection speed, pressure, and cooling time are meticulously monitored to ensure the formation of high-quality ABS components with precise dimensions and surface finish.
Applications Across Industries
The versatility of ABS injection molding lends itself to a diverse array of applications across various industries. In the automotive sector, ABS is widely used for manufacturing exterior and interior components, including bumpers, dashboard panels, and trim pieces, due to its excellent impact resistance and aesthetic appeal. In the consumer electronics industry, ABS is favored for its electrical insulation properties, making it suitable for casings and enclosures of electronic devices. Additionally, ABS finds applications in the production of household appliances, medical devices, and recreational equipment, highlighting its adaptability and utility.
Challenges and Solutions
Despite its numerous advantages, ABS injection molding presents certain challenges that necessitate innovative solutions. Common challenges include warpage, sink marks, and surface defects, which can impact the quality and functionality of the final product. Advanced mould design, precise control of processing parameters, and the utilization of additives and reinforcements are employed to mitigate these challenges and enhance the performance of ABS components. Additionally, the integration of simulation tools aids in predicting and optimizing the injection molding process, thereby minimizing defects and optimizing cycle times.
Future Directions and Recommendations
As the manufacturing landscape continues to evolve, the future of ABS injection molding holds promising opportunities for innovation and advancement. Research efforts are focused on developing sustainable alternatives to traditional ABS resins, incorporating recycled materials and bio-based polymers to mitigate environmental impact. Furthermore, advancements in additive manufacturing techniques, such as 3D printing, are expanding the possibilities for rapid prototyping and customized production of ABS components. Continued collaboration between industry stakeholders, research institutions, and regulatory bodies is essential to drive technological innovation and ensure the sustainable growth of ABS injection molding.
In conclusion, ABS injection molding emerges as a cornerstone in modern manufacturing, offering unparalleled versatility, durability, and cost-effectiveness across diverse industries. While it presents certain challenges, innovative techniques and solutions continue to propel its evolution and adoption. Looking ahead, the future of ABS injection molding holds promise for further innovation, sustainability, and growth, shaping the way we design and produce plastic components for years to come.
GETTING A QUOTE WITH LK-MOULD IS FREE AND SIMPLE.
FIND MORE OF OUR SERVICES:
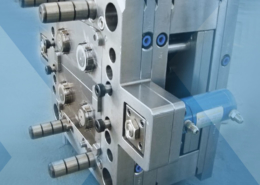
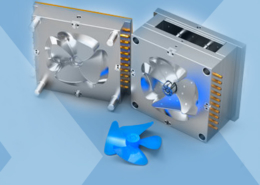
Plastic Molding

Rapid Prototyping
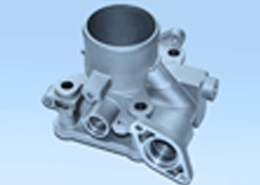
Pressure Die Casting
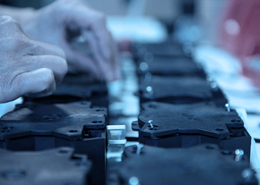
Parts Assembly
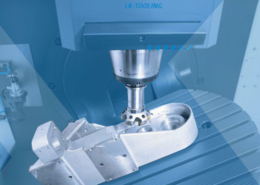