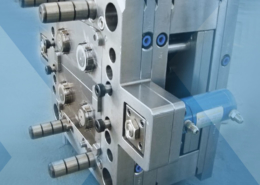
Exploring ABS Injection Molding: Precision Engineering Unveiled
Author:gly Date: 2024-06-08
Introduction
ABS (Acrylonitrile Butadiene Styrene) injection molding stands as a cornerstone in modern manufacturing, offering unparalleled versatility, durability, and aesthetic appeal. This innovative process involves injecting molten ABS resin into a mold cavity under high pressure, resulting in the production of complex and precise components. Delving into the realm of ABS injection molding unveils a world where creativity meets functionality, where precision engineering converges with material science, and where every mold tells a story of innovation.
Understanding ABS Injection Molding
ABS injection molding is a highly efficient manufacturing process that enables the production of a wide range of components with exceptional mechanical properties.
Precision in Design and Production
ABS injection molding demands meticulous attention to detail in both design and production phases. Computer-aided design (CAD) software allows engineers to create intricate geometries with utmost precision, while advanced molding techniques and machinery ensure consistent quality and dimensional accuracy.
Material Properties and Performance
ABS resin offers a unique combination of properties, including high impact resistance, thermal stability, and surface finish. These characteristics make ABS an ideal choice for a diverse array of applications, ranging from automotive components to consumer electronics.
Surface Finishing and Aesthetics
ABS injection molding enables the production of components with impeccable surface finish and aesthetic appeal. Post-processing techniques such as painting, plating, and texturing further enhance the visual appeal and functionality of ABS parts, catering to the diverse needs of end-users.
Applications Across Industries
ABS injection molding finds widespread application across various industries, contributing to the functionality and aesthetics of countless products.
Automotive Sector
In the automotive industry, ABS injection molding plays a vital role in the production of interior and exterior components, including dashboard panels, trim pieces, and grille assemblies. The high impact resistance and durability of ABS make it well-suited for demanding automotive applications.
Consumer Electronics
ABS injection molding is prevalent in the consumer electronics industry, where it is used to manufacture casings, housings, and structural components for devices such as smartphones, laptops, and home appliances. The lightweight nature of ABS, coupled with its excellent dimensional stability, makes it an ideal choice for electronic enclosures.
Medical Devices
ABS injection molding finds application in the fabrication of medical devices and equipment, where precision, biocompatibility, and sterilizability are paramount. Components such as instrument housings, enclosures, and disposable devices benefit from the versatility and reliability of ABS resin.
Technological Advancements and Future Outlook
The landscape of ABS injection molding continues to evolve with advancements in technology, materials, and manufacturing processes.
Additive Manufacturing Integration
The integration of additive manufacturing, such as 3D printing, into ABS injection molding processes offers new possibilities for design freedom and rapid prototyping. Hybrid manufacturing techniques enable the production of complex geometries and customized components with reduced lead times and costs.
Sustainable Practices
ABS injection molding manufacturers are increasingly embracing sustainable practices to minimize environmental impact. From utilizing recycled ABS resin to optimizing energy consumption and waste management, these initiatives underscore a commitment to eco-friendly manufacturing and resource conservation.
Digital Twin Technologies
Digital twin technologies enable real-time monitoring and optimization of ABS injection molding processes, enhancing efficiency, quality, and predictive maintenance. By creating virtual replicas of production systems, manufacturers can identify potential issues, optimize parameters, and improve overall performance.
Conclusion
In conclusion, ABS injection molding stands as a testament to the ingenuity and precision of modern manufacturing. From automotive to consumer electronics and medical devices, ABS components permeate every facet of our daily lives. As technology advances and sustainability becomes increasingly important, the role of ABS injection molding in shaping the future of manufacturing will only continue to grow. By embracing innovation, sustainability, and collaboration, ABS injection molding manufacturers can pave the way for a more efficient, resilient, and environmentally friendly manufacturing industry.
GETTING A QUOTE WITH LK-MOULD IS FREE AND SIMPLE.
FIND MORE OF OUR SERVICES:
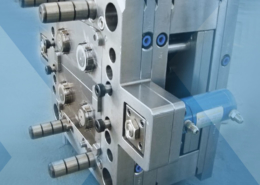
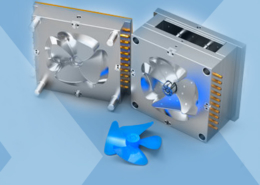
Plastic Molding

Rapid Prototyping
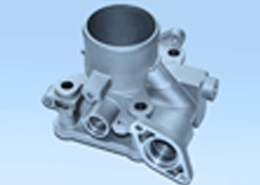
Pressure Die Casting
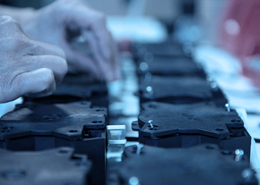
Parts Assembly
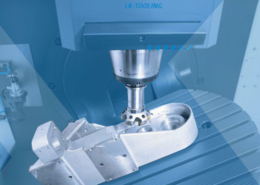