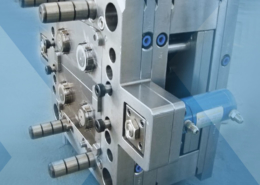
Understanding Injection Molding: Innovation and Application
Author:gly Date: 2024-06-08
Introduction:
Injection molding is a pivotal process in manufacturing, revolutionizing the production of intricate parts across industries. This article delves into the depths of injection molding, exploring its mechanisms, applications, and future prospects.
1. Process Overview:
Injection molding involves injecting molten material into a mold cavity under high pressure, allowing it to cool and solidify into the desired shape. This process is highly versatile, accommodating various materials like plastics, metals, and ceramics.
The process begins with the preparation of the material, typically in pellet or powder form. The material is then heated to a molten state and injected into the mold. Once inside the mold, it undergoes cooling and solidification, after which the mold opens, releasing the newly formed part.
Injection molding offers unmatched precision and repeatability, making it ideal for mass production of complex components with tight tolerances.
2. Material Selection:
Material selection is critical in injection molding, impacting the properties and performance of the final product. Polymers dominate the injection molding landscape due to their versatility, cost-effectiveness, and ease of processing.
Common polymers used include thermoplastics like polyethylene, polypropylene, and polystyrene, as well as engineering plastics such as ABS, nylon, and polycarbonate. Each material offers unique properties such as strength, flexibility, and heat resistance, catering to diverse application requirements.
3. Design Considerations:
Designing for injection molding requires careful consideration of various factors to ensure manufacturability and optimal part performance. Key considerations include draft angles, wall thickness, and feature geometry.
Draft angles facilitate mold ejection, minimizing friction and preventing part distortion. Uniform wall thickness promotes consistent cooling and reduces warping, while optimizing feature geometry enhances moldability and minimizes defects.
Computer-aided design (CAD) software enables designers to simulate molding processes, identifying potential issues and optimizing designs before production.
4. Applications Across Industries:
Injection molding finds applications across a myriad of industries, from automotive and aerospace to consumer electronics and medical devices. In the automotive sector, it is used for manufacturing interior and exterior components, including dashboards, bumpers, and lighting systems.
In the consumer electronics industry, injection molding produces casings, connectors, and keypads with intricate designs and high precision. Medical applications include syringes, IV components, and surgical instruments, demanding biocompatibility and strict adherence to regulatory standards.
Conclusion:
Injection molding stands as a cornerstone of modern manufacturing, driving innovation and enabling the production of complex parts with unparalleled efficiency and precision. Understanding its intricacies, from process fundamentals to material selection and design considerations, is essential for harnessing its full potential across diverse industries.
As technology advances, the integration of additive manufacturing techniques and smart materials holds promise for further enhancing the capabilities of injection molding. Continued research and development in this field are crucial for unlocking new opportunities and addressing emerging challenges, ensuring its continued relevance and impact in the ever-evolving landscape of manufacturing.
Through collaborative efforts and a commitment to innovation, injection molding will continue to shape the future of manufacturing, offering limitless possibilities for creativity and advancement.
GETTING A QUOTE WITH LK-MOULD IS FREE AND SIMPLE.
FIND MORE OF OUR SERVICES:
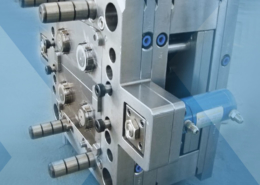
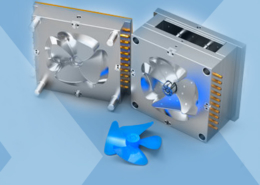
Plastic Molding

Rapid Prototyping
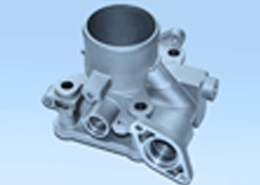
Pressure Die Casting
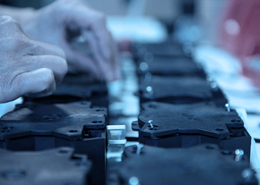
Parts Assembly
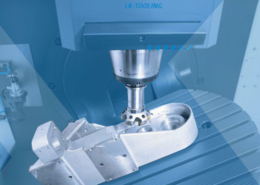