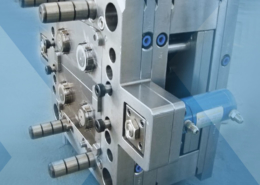
Unraveling the Dynamics of Thermoplastic Injection Molding
Author:gly Date: 2024-06-08
Thermoplastic injection molding stands as a cornerstone in modern manufacturing, revolutionizing the production of intricate components across various industries. This article embarks on a journey through the realm of thermoplastic injection, unraveling its complexities, applications, advancements, and future prospects.
Introducing Thermoplastic Injection Molding
Thermoplastic injection molding involves the melting of thermoplastic materials, injecting the molten resin into a mold cavity, and cooling it to solidify into the desired shape. This versatile process enables the fabrication of complex geometries with high precision and repeatability, making it indispensable in industries ranging from automotive and aerospace to electronics and consumer goods.
Evolution and Significance
The origins of thermoplastic injection molding trace back to the mid-20th century, driven by the need for cost-effective mass production techniques. Over the decades, advancements in materials science, mold design, and manufacturing technologies have propelled the technique to new heights of efficiency and versatility. Today, thermoplastic injection molding serves as the backbone of modern manufacturing, underpinning the production of a vast array of products that shape our daily lives.
Exploring Key Aspects of Thermoplastic Injection
Material Selection and Compatibility
Material selection is a critical aspect of thermoplastic injection molding, influencing part properties, performance, and manufacturability. Engineers must consider factors such as mechanical strength, thermal stability, chemical resistance, and cost when choosing the appropriate resin for a given application. Moreover, compatibility between the resin and mold materials is paramount to prevent issues like adhesion, warping, and mold fouling.
Impact of Material Properties
The mechanical, thermal, and rheological properties of thermoplastic resins significantly impact the injection molding process and the quality of the final parts. Materials with high melt flow rates facilitate faster filling and shorter cycle times, whereas those with superior strength and durability ensure long-term performance and reliability. Additionally, factors like shrinkage and crystallization behavior must be carefully evaluated to mitigate dimensional inaccuracies and part defects.
Advancements in Material Science
Ongoing research in material science continues to expand the palette of thermoplastic resins available for injection molding, offering enhanced properties and functionalities. Innovations such as bio-based polymers, conductive plastics, and self-healing materials open new possibilities for applications in sectors like healthcare, electronics, and sustainability. Furthermore, developments in recycling technologies address concerns regarding environmental impact, fostering a circular economy for thermoplastics.
Process Optimization and Control
Optimizing the injection molding process is essential for achieving consistent part quality, minimizing cycle times, and maximizing production efficiency. This entails fine-tuning parameters such as injection speed, pressure, temperature, and cooling time to balance material flow, mold filling, and part ejection. Additionally, real-time monitoring and feedback systems enable proactive adjustments to mitigate deviations and ensure conformity to specifications.
Role of Process Simulation
Simulation software plays a pivotal role in predicting and optimizing various aspects of the injection molding process, from mold design and material selection to cycle optimization and defect analysis. By simulating fluid flow, heat transfer, and stress distribution, engineers can identify potential issues upfront, refine design parameters, and optimize production parameters. This proactive approach minimizes costly iterations and accelerates time-to-market for new products.
Advancements in Process Monitoring
Recent advancements in sensor technology and data analytics enable comprehensive monitoring of key process parameters during injection molding. Real-time feedback on variables like temperature, pressure, and material viscosity allows for immediate adjustments to maintain process stability and part quality. Furthermore, machine learning algorithms analyze vast datasets to identify patterns, optimize process parameters, and predict potential defects, enhancing overall efficiency and productivity.
Design for Manufacturability
Designing parts for manufacturability is essential to ensure successful and cost-effective production via thermoplastic injection molding. Engineers must consider factors such as part geometry, draft angles, wall thickness, and gating design to facilitate proper material flow, mold filling, and part ejection. Moreover, incorporating features like ribs, fillets, and bosses enhances structural integrity and dimensional stability while minimizing material usage and cycle times.
Importance of Design Guidelines
Adhering to established design guidelines for thermoplastic injection molding is crucial to avoid common pitfalls and optimize part quality and production efficiency. Guidelines regarding wall thickness, corner radii, surface finishes, and undercuts help mitigate issues like sink marks, warpage, and moldability defects. Collaboration between designers, engineers, and molders early in the product development process ensures that design intent aligns with manufacturing capabilities and constraints.
Integration of Additive Manufacturing
The integration of additive manufacturing technologies, such as 3D printing, with thermoplastic injection molding offers new opportunities for design innovation and customization. Hybrid processes like conformal cooling and tooling enable the production of complex mold geometries with enhanced cooling efficiency, reducing cycle times and improving part quality. Furthermore, additive manufacturing facilitates rapid prototyping and iteration, accelerating product development cycles and fostering innovation.
Concluding Remarks
Thermoplastic injection molding stands at the nexus of innovation and industrial progress, enabling the efficient and cost-effective production of complex components across diverse industries. By delving into its intricacies, exploring key aspects, and embracing advancements, manufacturers can unlock new possibilities for product design, performance, and sustainability. As the journey of thermoplastic injection molding continues, fueled by research, collaboration, and technological breakthroughs, it remains poised to shape the future of manufacturing in profound ways.
GETTING A QUOTE WITH LK-MOULD IS FREE AND SIMPLE.
FIND MORE OF OUR SERVICES:
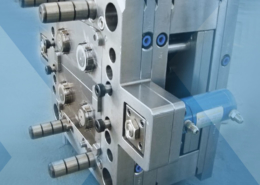
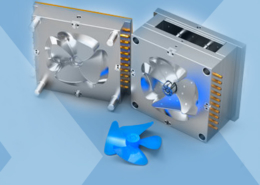
Plastic Molding

Rapid Prototyping
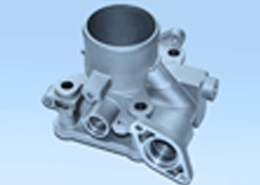
Pressure Die Casting
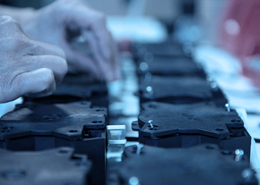
Parts Assembly
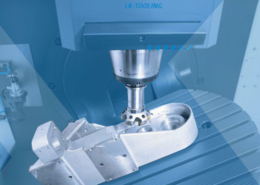