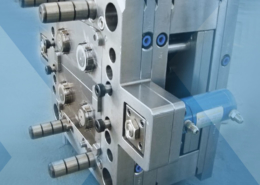
Exploring Thermoset Molding: Innovation in Polymer Engineering
Author:gly Date: 2024-06-08
Introduction
Thermoset molding stands as a cornerstone in modern polymer engineering, offering unparalleled versatility and durability in the manufacturing industry. This process involves the transformation of thermosetting polymers from a liquid or soft solid state into a rigid final product through the application of heat and pressure. Its widespread application spans across automotive, aerospace, electronics, and consumer goods sectors, showcasing its significance in various fields. This article aims to delve into the intricacies of thermoset molding, exploring its diverse applications, unique properties, processing techniques, and future prospects.
Applications
Automotive Industry:
Thermoset molding plays a crucial role in the automotive sector, where lightweight yet resilient components are in high demand. Parts such as engine components, exterior panels, and interior trim benefit from the exceptional strength-to-weight ratio and heat resistance offered by thermoset materials, contributing to vehicle performance, safety, and fuel efficiency.
Electronics:
In the electronics industry, miniaturization and performance optimization are key drivers, making thermoset molding an ideal choice for encapsulating and protecting delicate electronic components. Printed circuit boards (PCBs), connectors, and housing enclosures manufactured through this process exhibit excellent dimensional stability, flame retardancy, and electrical insulation properties, ensuring reliability and longevity in electronic devices.
Construction and Infrastructure:
Thermoset molded products find extensive use in construction and infrastructure applications, where durability, weather resistance, and corrosion resistance are paramount. From pipes and fittings to structural composites and insulation materials, thermoset polymers offer superior performance in harsh environments, enhancing the longevity and sustainability of infrastructure projects.
Unique Properties
Chemical Resistance:
Thermoset polymers exhibit exceptional resistance to a wide range of chemicals, including acids, bases, solvents, and oils. This property makes them suitable for applications where exposure to corrosive substances is inevitable, ensuring long-term performance and reliability in challenging environments.
Dimensional Stability:
Unlike thermoplastics, which can deform under high temperatures, thermoset materials retain their shape and mechanical properties even when exposed to elevated temperatures. This dimensional stability is crucial in precision engineering applications where tight tolerances and consistency are required.
High Temperature Resistance:
Thermoset polymers possess inherent heat resistance, enabling them to withstand elevated temperatures without softening or melting. This property makes them suitable for high-temperature applications such as automotive under-the-hood components, industrial machinery, and aerospace structures.
Processing Techniques
Compression Molding:
Compression molding is a widely used technique in thermoset molding, wherein the polymer is placed in a heated mold cavity and compressed under high pressure until it cures and solidifies. This method is suitable for large and intricate parts, offering high production efficiency and excellent surface finish.
Injection Molding:
Injection molding involves injecting molten thermoset resin into a mold cavity under high pressure, where it undergoes polymerization and solidification. This process offers precise control over part dimensions, intricate geometries, and short cycle times, making it ideal for mass production of complex components.
Transfer Molding:
Transfer molding combines the principles of compression and injection molding, utilizing a heated pot containing the thermoset material, which is then forced into the mold cavity through a plunger. This method allows for greater control over material flow and can accommodate inserts or reinforcements, offering versatility in part design and customization.
Future Prospects
The future of thermoset molding lies in innovation-driven advancements that address sustainability, performance, and process efficiency. Research efforts focus on developing bio-based thermoset resins derived from renewable sources, reducing reliance on fossil fuels and minimizing environmental impact. Furthermore, advancements in digital design, simulation software, and additive manufacturing techniques pave the way for enhanced part optimization, material utilization, and waste reduction.
Conclusion
Thermoset molding stands as a cornerstone in polymer engineering, offering a unique combination of properties, processing techniques, and applications. Its versatility, durability, and reliability make it indispensable across various industries, driving innovation and progress in manufacturing. By embracing technological advancements and sustainable practices, the thermoset molding industry is poised to meet the evolving needs of the global market while contributing to a greener and more resilient future.
GETTING A QUOTE WITH LK-MOULD IS FREE AND SIMPLE.
FIND MORE OF OUR SERVICES:
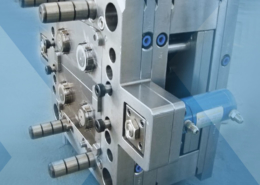
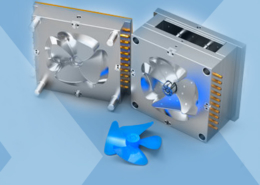
Plastic Molding

Rapid Prototyping
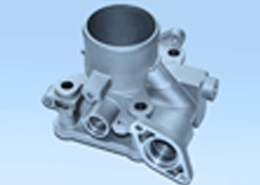
Pressure Die Casting
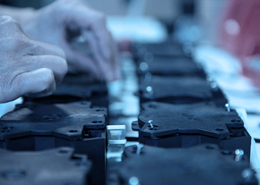
Parts Assembly
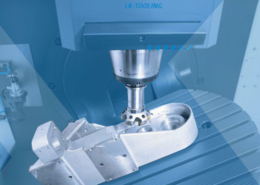