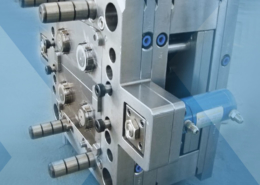
Unveiling the Power of Thermolator Injection Molding: Precision and Efficiency
Author:gly Date: 2024-06-08
Thermolator injection molding stands as a pinnacle of precision engineering, combining the principles of injection molding with advanced thermolator technology to achieve unparalleled control over the molding process. This sophisticated manufacturing technique offers exceptional temperature regulation, ensuring optimal conditions for producing high-quality molded products. In this article, we embark on a journey to explore the world of thermolator injection molding, uncovering its significance, mechanisms, applications, and future prospects.
Introducing Thermolator Injection Molding
Thermolator injection molding, also known as temperature-controlled injection molding, revolutionizes the traditional injection molding process by integrating precise temperature control mechanisms into the molding equipment. This technology allows for meticulous regulation of the temperature of the mold and the injected material, optimizing the flow characteristics, material properties, and overall quality of the molded products. The ability to maintain uniform temperatures throughout the molding process enhances product consistency, reduces defects, and improves production efficiency, making thermolator injection molding a preferred choice for industries requiring precision-engineered components.
Key Components and Mechanisms
Temperature Control Units
At the heart of thermolator injection molding is the temperature control unit, comprising heating and cooling elements, sensors, and controllers. These units meticulously regulate the temperature of the mold and the injected material, ensuring precise control over the molding process. Advanced temperature control algorithms and feedback mechanisms further enhance the accuracy and stability of the system.
Thermal Management Systems
Thermolator injection molding systems employ sophisticated thermal management systems to maintain uniform temperatures throughout the mold cavity. This prevents thermal gradients and ensures consistent material flow and solidification, resulting in high-quality, dimensionally accurate molded products.
Applications and Industries
Automotive
In the automotive industry, thermolator injection molding is utilized for manufacturing precision components such as interior trim, dashboard panels, and exterior body parts. The ability to produce complex geometries with tight tolerances and exceptional surface finish makes thermolator injection molding an ideal choice for automotive applications.
Electronics
The electronics industry relies on thermolator injection molding for producing delicate components such as connectors, housings, and enclosures. The precise temperature control ensures the integrity of electronic components, protecting them from thermal stress and ensuring optimal performance and reliability.
Advantages and Benefits
Enhanced Product Quality
Thermolator injection molding offers superior product quality, with precise control over dimensions, surface finish, and material properties. The uniform temperature distribution minimizes defects such as warpage, shrinkage, and sink marks, resulting in pristine molded products.
Increased Efficiency and Productivity
The efficiency of thermolator injection molding translates into increased productivity and cost savings for manufacturers. The ability to achieve optimal processing conditions rapidly reduces cycle times, increases throughput, and minimizes downtime, maximizing the overall efficiency of the manufacturing process.
Challenges and Future Directions
Cost of Implementation
The initial investment required for implementing thermolator injection molding systems may be significant, posing a barrier to entry for some manufacturers. However, advancements in technology and economies of scale are driving down costs, making thermolator injection molding more accessible to a broader range of industries.
Sustainability and Environmental Impact
As environmental concerns become increasingly prominent, there is growing pressure on manufacturers to adopt sustainable practices. Future research and development efforts in thermolator injection molding may focus on optimizing energy efficiency, reducing material waste, and exploring eco-friendly materials to minimize the environmental impact of the manufacturing process.
Conclusion
In conclusion, thermolator injection molding represents a pinnacle of precision engineering, offering unparalleled control over the molding process to achieve superior product quality and efficiency. With its applications spanning across industries such as automotive, electronics, and consumer goods, thermolator injection molding plays a vital role in shaping the modern manufacturing landscape. As technology continues to evolve and environmental considerations become increasingly prominent, the future of thermolator injection molding holds promising opportunities for innovation, sustainability, and continued advancements in precision manufacturing. Through ongoing research, collaboration, and investment in technology, manufacturers can unlock new possibilities and propel the industry towards a cleaner, more efficient, and more sustainable future.
GETTING A QUOTE WITH LK-MOULD IS FREE AND SIMPLE.
FIND MORE OF OUR SERVICES:
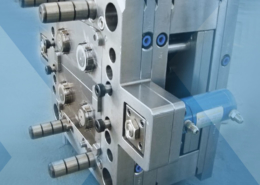
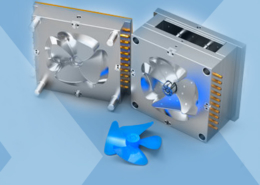
Plastic Molding

Rapid Prototyping
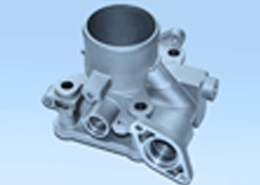
Pressure Die Casting
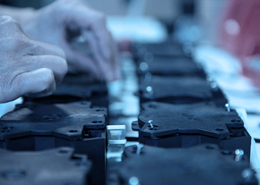
Parts Assembly
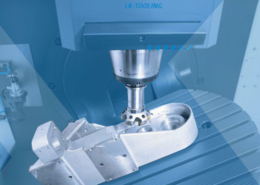