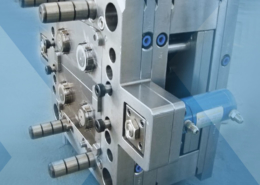
Exploring the Intersection of Prototyping and Plastic Molding
Author:gly Date: 2024-06-08
Introduction
The marriage of prototyping and plastic molding represents a pivotal synergy in modern manufacturing. This article delves into the symbiotic relationship between these two processes, offering insights into their significance, applications, and impact on various industries.
Understanding Prototyping
Prototyping serves as a vital phase in the product development cycle, allowing designers and engineers to translate conceptual ideas into tangible prototypes. Whether through rapid prototyping techniques like 3D printing or traditional methods such as CNC machining, prototyping enables iterative design refinement and validation before mass production.
The Role of Plastic Molding
Plastic molding, on the other hand, facilitates the mass production of components with intricate geometries and precise specifications. Through techniques like injection molding and blow molding, manufacturers can replicate prototypes at scale, achieving cost-effectiveness and efficiency in production.
Prototyping for Plastic Molding
Prototyping plays a crucial role in the plastic molding process, serving as a blueprint for tooling and production. By creating prototypes, manufacturers can assess design feasibility, identify potential issues, and optimize mold configurations before proceeding to mass production. This iterative approach minimizes risks and ensures the final product meets quality standards.
Advanced Materials and Techniques
Recent advancements in materials science and molding techniques have revolutionized the prototyping and plastic molding landscape. From high-performance polymers to multi-shot molding technologies, manufacturers now have access to a diverse range of materials and processes, enabling greater innovation and customization in product development.
Applications Across Industries
The integration of prototyping and plastic molding finds applications across a myriad of industries, from automotive and aerospace to consumer electronics and medical devices. By leveraging prototyping for design validation and plastic molding for mass production, companies can accelerate time-to-market, enhance product quality, and gain a competitive edge in their respective markets.
Challenges and Opportunities
Despite its numerous benefits, the integration of prototyping and plastic molding presents challenges such as cost constraints, material selection, and process optimization. However, these challenges also present opportunities for innovation and improvement, driving continuous advancements in manufacturing technologies and practices.
Future Perspectives
Looking ahead, the synergy between prototyping and plastic molding is poised to further revolutionize the manufacturing industry. With ongoing advancements in materials, processes, and digital technologies, the possibilities for product innovation and customization are limitless. Embracing this convergence will be key for companies seeking to stay competitive in an ever-evolving market landscape.
Conclusion
In conclusion, the convergence of prototyping and plastic molding represents a transformative force in modern manufacturing. By bridging the gap between design iteration and mass production, this synergy enables companies to streamline the product development process, reduce time-to-market, and unlock new opportunities for innovation. As technology continues to advance, the integration of prototyping and plastic molding will remain a cornerstone of success for forward-thinking manufacturers.
GETTING A QUOTE WITH LK-MOULD IS FREE AND SIMPLE.
FIND MORE OF OUR SERVICES:
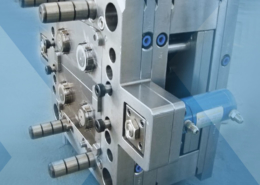
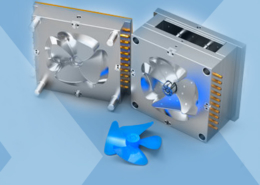
Plastic Molding

Rapid Prototyping
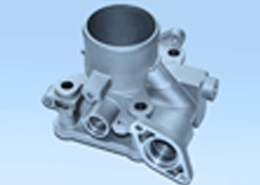
Pressure Die Casting
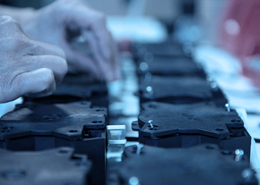
Parts Assembly
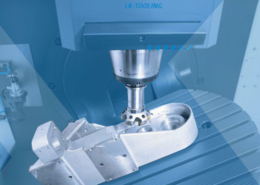