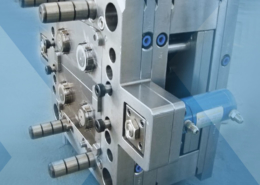
Unveiling the World of Products Made with Injection Moulding
Author:gly Date: 2024-06-08
The realm of products made with injection moulding unveils a world of innovation, efficiency, and versatility. From everyday household items to intricate automotive components, injection moulding plays a pivotal role in shaping the modern manufacturing landscape. This article aims to provide readers with an insightful exploration into the realm of products crafted through injection moulding, offering a comprehensive understanding of its applications, benefits, challenges, and future prospects.
Exploring Injection Moulding: An Introduction
Injection moulding stands as one of the most prevalent manufacturing processes globally, renowned for its ability to produce high volumes of intricate parts with exceptional precision and consistency. By injecting molten material into a mould cavity, this process enables the creation of a wide range of products with varying complexities, sizes, and materials.
Applications Across Industries
Automotive Sector
In the automotive industry, injection moulding plays a crucial role in manufacturing interior and exterior components, such as dashboards, bumpers, and interior trim. The process offers automotive manufacturers the advantage of producing lightweight yet durable parts with intricate designs and superior surface finishes.
Consumer Electronics
Products made with injection moulding dominate the consumer electronics sector, encompassing everything from smartphone cases to intricate components within electronic devices. The process enables manufacturers to meet the demands for sleek, lightweight, and aesthetically pleasing products while ensuring structural integrity and functionality.
Medical Devices
Injection moulding revolutionizes the production of medical devices, including syringes, IV components, and surgical instruments. With stringent requirements for biocompatibility, sterility, and precision, injection moulding allows for the fabrication of medical-grade products that meet the highest regulatory standards.
Advantages and Challenges
Advantages
Injection moulding offers numerous advantages, including high production efficiency, cost-effectiveness, design flexibility, and minimal material waste. Its ability to accommodate a wide range of materials, from thermoplastics to elastomers, further enhances its versatility and applicability across industries.
Challenges
Despite its many benefits, injection moulding presents certain challenges, such as initial tooling costs, design limitations, and environmental concerns related to material waste and energy consumption. Addressing these challenges requires continuous innovation in material science, process optimization, and sustainable practices.
Future Perspectives and Recommendations
Looking ahead, the future of products made with injection moulding holds immense potential for innovation and advancement. Emerging technologies, such as 3D printing and advanced materials, are poised to redefine the capabilities and sustainability of injection moulding processes. Collaboration between industry stakeholders, academia, and policymakers is essential to drive research and development initiatives aimed at addressing current challenges and unlocking new opportunities in the field.
In summary, products made with injection moulding embody the pinnacle of modern manufacturing, offering unparalleled efficiency, precision, and versatility across diverse industries. By understanding its applications, advantages, challenges, and future prospects, stakeholders can navigate the evolving landscape of injection moulding with confidence and foresight.
GETTING A QUOTE WITH LK-MOULD IS FREE AND SIMPLE.
FIND MORE OF OUR SERVICES:
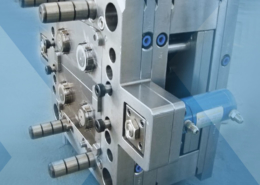
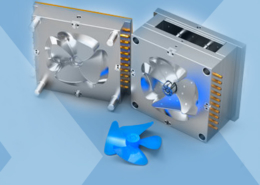
Plastic Molding

Rapid Prototyping
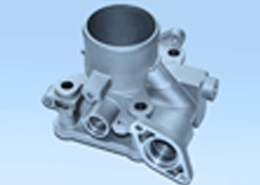
Pressure Die Casting
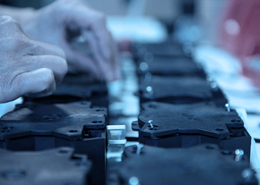
Parts Assembly
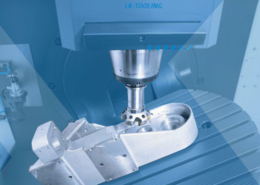