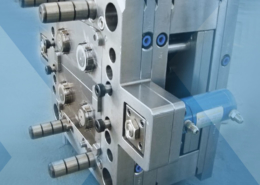
Exploring Precision Plastic Molding: Revolutionizing Manufacturing
Author:gly Date: 2024-06-08
Precision plastic molding stands as a cornerstone in modern manufacturing, heralding a new era of efficiency, precision, and versatility in the production of plastic components. This article aims to delve into the intricacies of precision plastic molding, providing readers with a comprehensive understanding of its processes, applications, and significance in contemporary manufacturing landscapes.
Introduction: Unveiling Precision Plastic Molding
Precision plastic molding, also known as injection molding, is a manufacturing process wherein molten plastic material is injected into a mold cavity under high pressure. Upon cooling and solidification, the molded plastic takes the shape of the mold cavity, resulting in the production of precise and intricate plastic components. This process has revolutionized the manufacturing industry by enabling the mass production of plastic parts with consistent quality and dimensional accuracy.
1. Evolution and Advancements
The evolution of precision plastic molding traces back to the early 20th century, with the advent of industrial plastics and the development of rudimentary molding techniques. Over the years, advancements in materials, mold designs, and process technologies have propelled precision plastic molding into a highly sophisticated and precise manufacturing method. From conventional hydraulic molding machines to state-of-the-art electric and hybrid machines, the industry has witnessed remarkable progress in terms of efficiency, speed, and precision.
2. Design and Engineering Excellence
The success of precision plastic molding hinges upon meticulous design and engineering. Engineers leverage advanced CAD software to create intricate mold designs with precise geometries and features. Finite element analysis (FEA) and mold flow simulation tools are employed to optimize mold designs and predict potential manufacturing challenges such as warpage and shrinkage.
Furthermore, the selection of materials plays a critical role in the performance and longevity of the mold. High-grade tool steels, such as P20, H13, and S136, are preferred for their excellent wear resistance and thermal properties. Advanced surface treatments and coatings enhance the durability and surface finish of the mold, ensuring optimal performance over prolonged production runs.
3. Process Optimization and Efficiency
Process optimization is paramount in precision plastic molding to achieve consistent part quality and minimize production costs. Parameters such as injection speed, pressure, temperature, and cooling time are meticulously controlled to achieve optimal part filling and minimize cycle times. Additionally, automation and robotics have streamlined production processes, reducing labor costs and increasing throughput.
The implementation of Industry 4.0 technologies, such as IoT-enabled machines and real-time monitoring systems, has enabled manufacturers to collect and analyze data to improve process efficiency and quality control. Predictive maintenance algorithms identify potential equipment failures before they occur, minimizing downtime and maximizing productivity.
4. Diverse Applications and Impact
Precision plastic molding finds applications across a myriad of industries, including automotive, aerospace, electronics, medical devices, and consumer goods. In the automotive sector, it is used to manufacture interior and exterior components, such as dashboards, bumpers, and door panels, with high precision and durability. In the medical field, it facilitates the production of intricate medical devices and implants with biocompatible materials.
The impact of precision plastic molding extends beyond production efficiency and cost reduction. It enables the realization of complex designs and innovative product concepts, driving advancements in product functionality, aesthetics, and performance. Moreover, the lightweight nature of plastic components contributes to fuel efficiency and sustainability in automotive and aerospace applications.
Conclusion: Paving the Way for Future Innovation
In conclusion, precision plastic molding stands as a testament to human ingenuity and technological advancement in the manufacturing industry. Its evolution from a rudimentary process to a highly sophisticated manufacturing method has reshaped the landscape of modern production. As we look towards the future, continued research and innovation in precision plastic molding hold the key to unlocking new possibilities in product design, manufacturing efficiency, and sustainability. By embracing emerging technologies and collaborative partnerships, we can propel the industry towards greater heights of innovation and excellence.
GETTING A QUOTE WITH LK-MOULD IS FREE AND SIMPLE.
FIND MORE OF OUR SERVICES:
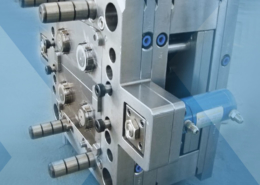
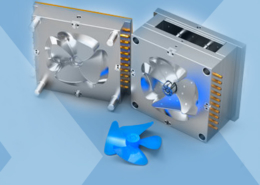
Plastic Molding

Rapid Prototyping
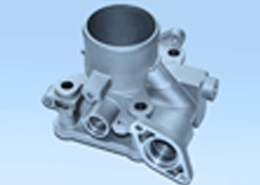
Pressure Die Casting
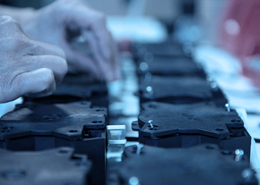
Parts Assembly
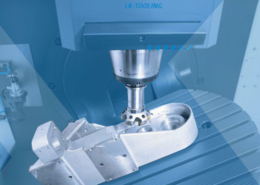