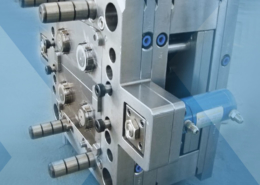
Prototype Plastic Injection Molding: Accelerating Innovation
Author:gly Date: 2024-06-08
Introduction
Prototype plastic injection molding stands as a vital tool in the product development process, facilitating the rapid iteration and refinement of designs before full-scale production. As industries become increasingly competitive and time-to-market pressures intensify, the ability to quickly produce functional prototypes is crucial for staying ahead of the curve. This article explores the world of prototype plastic injection molding, shedding light on its significance, capabilities, and impact on innovation.
Prototype plastic injection molding enables the production of functional prototypes and low-volume production parts using the same materials and processes as final production runs. This allows designers and engineers to validate designs, test functionality, and gather feedback early in the product development cycle, minimizing risks and accelerating time to market.
Speed and Efficiency
One of the primary advantages of prototype plastic injection molding is its ability to deliver functional prototypes quickly and efficiently. Traditional prototyping methods such as CNC machining and 3D printing may offer speed but often lack the material properties and surface finish required for accurate functional testing.
Quick Turnaround
Prototype plastic injection molding offers rapid turnaround times, with parts typically produced in days rather than weeks. This enables designers to iterate designs rapidly, incorporating feedback and making adjustments as needed to optimize product performance and manufacturability.
Cost-Effectiveness
Despite its speed and efficiency, prototype plastic injection molding remains cost-effective compared to traditional prototyping methods. The ability to produce multiple parts from the same mold reduces per-unit costs, making it an attractive option for small to medium-sized production runs and bridge manufacturing.
Material Selection
The choice of materials in prototype plastic injection molding is critical for achieving accurate functional prototypes that closely mimic the properties of final production parts. A wide range of engineering-grade thermoplastics is available, offering varying levels of strength, flexibility, and heat resistance.
Material Compatibility
Prototype plastic injection molding allows for the use of the same materials as final production runs, ensuring compatibility and consistency in material properties and performance. This enables designers to conduct accurate functional testing and validate design concepts with confidence.
Material Validation
By producing prototypes using production-grade materials, prototype plastic injection molding enables designers to validate material properties such as mechanical strength, chemical resistance, and thermal stability. This ensures that prototypes accurately reflect the behavior of final production parts under real-world conditions.
Design Optimization
Prototype plastic injection molding empowers designers to optimize designs for manufacturability, functionality, and performance early in the product development process. By leveraging the capabilities of injection molding, designers can refine designs to achieve optimal results.
Complex Geometries
Injection molding allows for the production of complex geometries and intricate details that may be challenging or impossible to achieve with other prototyping methods. This enables designers to explore innovative design concepts and push the boundaries of what is achievable in product development.
Tolerance Control
Prototype plastic injection molding offers tight tolerance control, ensuring that prototypes accurately reflect the dimensions and specifications of final production parts. This is essential for evaluating fit, form, and function and ensuring seamless integration with other components in the assembly.
Conclusion
Prototype plastic injection molding serves as a catalyst for innovation, enabling designers and engineers to bring their ideas to life quickly and efficiently. By providing fast, cost-effective access to functional prototypes, it accelerates the product development process, reduces time to market, and ultimately drives success in today's competitive landscape.
In conclusion, prototype plastic injection molding offers a strategic advantage in the product development process, providing a fast, cost-effective, and reliable means of validating designs and bringing products to market. As technology continues to evolve, the future of prototype plastic injection molding holds promise for even greater speed, efficiency, and innovation in product development.
GETTING A QUOTE WITH LK-MOULD IS FREE AND SIMPLE.
FIND MORE OF OUR SERVICES:
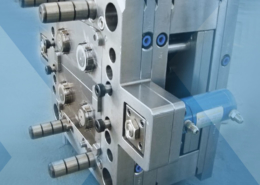
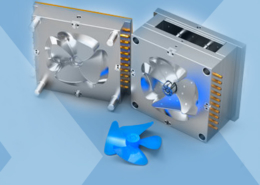
Plastic Molding

Rapid Prototyping
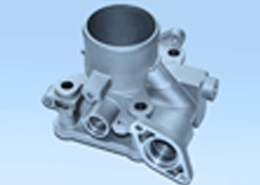
Pressure Die Casting
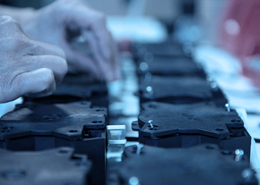
Parts Assembly
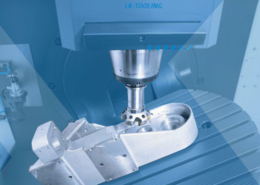