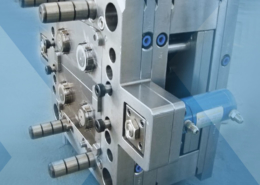
Home Plastic Injection Molding Offered on Kickstarter - small run injection mold
Author:gly Date: 2024-09-30
This study was also supported by companies including iQTemp, Deutsche Edelstahlwerke, 3D Laser BW, and Siemens NX, as well as institutes, such as Fraunhofer ILT and ACAM.
Once selected, AddUp and its partners evaluated each injection mould to determine how it could be optimised with Additive Manufacturing. Each part was then redesigned for AM, optimised for conformal cooling, and manufactured on AddUp’s 4-laser FormUp 350 Laser Beam Powder Bed Fusion (PBF-LB) Additive Manufacturing machine at AddUp’s AM Tooling Competence Centre in Aachen.
Reach a truly international audience that includes component manufacturers, end-users, industry suppliers, analysts, researchers and more.
Traditionally, manufacturers using injection moulding must contend with certain constraints that are inherent to the moulding process. Specifically, the mould’s performance is directly related to its ability to cool the injected parts. However, AM technology can be used to create complex cooling channels that are positioned as close as possible to the mould walls. By adapting the shape of these channels to cool the surface of the part more homogeneously, manufacturers can improve the quality of their products and experience higher productivity, as well as reduced cooling and cycle times.
AddUp SAS, headquartered in Cébazat, France, has partnered with WBA Aachener Werkzeugbau Akademie (WBA), in Aachen, Germany, to demonstrate the advantages of metal Additive Manufacturing for the mould making industry. After launching a Tooling Study in January 2023, the team found six tool-making companies that each identified existing moulds to be tested. AddUp and WBA have now produced the first prototypes of these injection moulds, all with optimised internal cooling channels.
Discover suppliers of these and more in our comprehensive advertisers’ index and buyer’s guide, available in the back of Metal AM magazine.
Given these convincing results and overall customer satisfaction, a strategic partnership between the two companies is ready to go live. Anna Bartz again: “Our growth and the success story with Kistler are just about to take off. With Kistler’s help, we can offer our clients solutions they didn’t even know before. For example, we’re already looking into projects for our large parts business, and there’s an upcoming opportunity with a big and globally present medical device supplier where we can count on Kistler – for sure.”
The companies selected for the Tooling Study were Pöppelmann, Siebenwurst, Harting, Zahoransky, GIRA, and Framas. They were given the opportunity to test the introduction of Additive Manufacturing into their workflow, and specifically implement the technical and economic advantages that AM technology brings to their injection moulds.
Meanwhile, injection moulding as a technology is certainly not standing still: at EVCO, engineers are looking into ways of continuing to improve traceability, down to each single part and its manufacturing footprint (including a complete record of conditions) – even for high-volume lots with millions of parts. “Here, we already acquire valuable data from the ComoDataCenter, but there’s still some way to go before we can assign that data to every single produced part – with a QR code, for example,” Busser explains. Liquid Silicone Rubber (or LSR) is another innovation that EVCO is pursuing. This material offers new opportunities for industry in general and the medtech sector in particular. “There are plenty of possible applications, but also a lot of skepticism in the market because of the difference in technology. But – with Kistler as an asset in our pocket – we’re optimistic that we will overcome the remaining obstacles and go to market.” Busser concludes.
For the project, post-processing was completed by the tooling company itself or by the WBA. Each of these ready-to-use moulds is now being sampled on the respective tooling company’s production lines, and the comparative data will be provided to WBA. The final results of the Tooling Study will be presented and published at the WBA’s General Assembly in late 2023.
AddUp explained that the choice of material is critical for tool makers, as moulds must meet high requirements, especially in terms of corrosion resistance, heat conductivity, and fatigue. Leveraging its twenty years of experience in AM, AddUp used Maraging 300, a material successfully used in series production by Michelin to manufacture over a million tyre mould sipes per year. In addition to Maraging 300, AddUp recently announced build parameters for AISI 420, a corrosion-resistant tool steel also known as 1.2083 in the German standard. It is expected that this new material will enable tooling manufacturers produce even more complex and efficient moulds.
Our audience includes component manufacturers, end-users, materials and equipment suppliers, analysts, researchers and more.
Technological advances are accelerating the journey towards zero-defect production in almost every industry. This is certainly true in the injection moulding sector, where manufacturers can exploit opportunities for optimisation and added-value manufacturing by instrumenting a mould with cavity pressure sensors and process monitoring equipment. EVCO Plastics is an expert in injection moulding and many additional technologies.
AddUp plans to launch a follow-up Tooling Study this autumn, and is inviting any tool makers interested to get in touch.
Don't miss any new issue of Metal AM magazine, and get the latest industry news. Sign up to our twice weekly newsletter.
Mike Busser had his own plastics company for micro-precision parts before joining EVCO, where he has now been in post as innovation center manager for over three years. He reports: “Requirements in medical device manufacturing are exceptionally high in terms of norms and regulations. We want to offer our customers added-value solutions: the trend is clearly towards zero defect – and that’s where Kistler comes in.” The two companies first made contact at K 2019 in Düsseldorf, where EVCO was in search of optimisation potential for their medtech projects. At this trade fair, they were introduced to cavity pressure sensors from Kistler as well as its ComoNeo process monitoring and control system – including ComoNeoMULTIFLOW, a feature that enables hot runner balancing for multi-cavity molds based on precise cavity pressure measurement. “MULTIFLOW detects the different filling statuses in each cavity, and automatically adapts the temperature of the injection nozzles,” Busser explains. “We’re currently using the system for zero-defect manufacturing of a component for a medical diagnostic kit. But in principle, all our molds now have a pocket for Kistler sensors. Now that the Kistler team in the US has supplied us with the portable ComoNeo, we’re able to use it flexibly for different projects.”
In addition to providing extensive industry news coverage, Metal AM magazine is known for exclusive, in-depth articles and technical reports.
Metal AM magazine, published quarterly in digital and print formats, is read by a rapidly expanding international audience.
This family-run business – founded in Wisconsin in 1964 – has a workforce of over 1,800 employees spread across eleven facilities in the US, China and Mexico. Anna Bartz, director of communications at EVCO said: “Together with our customers and partners, we take plastics processing to the next level. Following some recent growth, we now operate more than 260 moulding machines. But we not only offer excellence in injection moulding – in terms of state-of-the-art technology, close cooperation, tight tolerances and high quality demand – but also technologies and services across the entire value chain, such as automation, packaging, labelling and more.”
AddUp established its AM Tooling Competence Centre in Aachen, in partnership with WBA, in early 2023. This facility, which also serves as AddUp’s German subsidiary, gives tooling manufacturers access to AddUp’s Additive Manufacturing machines. Users can also submit application cases for evaluation and study of all aspects of their project, from the design when applied to PBF-LB, to profitability analysis and study of series production.
The current solution at EVCO operates with sixteen 9011C load cell washers from Kistler – one for each cavity at end-of-fill, mounted indirectly using a sleeve. Connecting cables can be exchanged independently of the sensor in case of damage or transmission problems, and non-compliant parts are separated robotically for each cavity. The team of process engineers, headed by Mike Busser, also installed a diagnostic tool that can monitor the status of the mould and its integrated Kistler measurement system at any time. Busser said: “This unique solution has truly helped us to achieve zero defect for our customer. It wouldn’t have been possible without the tremendous support of Kistler US – namely Jim Flom, Curtis Krick and Mike Prisby, who are now part of the family. By using ComoNeo, we’ve not only eliminated challenges with core shift, but also ramped up productivity and reduced cycle time.”
Precision Molding is one of EVCO's four main divisions, with products and solutions covering diverse industries ranging from agriculture and powersports to packaging and consumer goods. “We’re involved in just about everything except automotive parts and implantable devices – but medical technology is an important business for us, accounting for roughly 20% of our annual sales,” Bartz continues. Consequently, two EVCO sites are equipped with an ISO Class 8 Clean Room: EVCO headquarters in Deforest, Wisconsin, and the Chinese production facility in Dongguan.
Another key element of a joint approach from EVCO and Kistler will be customer education. Kistler solutions are not yet as well known or widely present in the US as in other markets, so a Tech Center demonstrating all the technologies and opportunities both parties can offer to a larger audience would be a major step forward for injection moulding and plastics processing in general. As Busser notes, this could leverage huge potential for EVCO clients in the Americas and beyond. “We can do more – that’s always our attitude and message towards our customers. Together with Kistler, we’re able to offer them solutions for needs they didn’t know they had – but, of course, this requires some education beforehand.” James Flom, field sales engineer Plastics at Kistler, comments: “We embrace the idea of jointly educating new and existing clients, and we’re excited about the many new opportunities and programs”.
For a current project in the medical sector, EVCO has opted for cavity pressure sensors from Kistler together with the ComoNeo process monitoring system – and in this application, ComoNeo's MULTIFLOW feature plays a particularly important part.
The free to access Metal Additive Manufacturing magazine archive offers unparalleled insight into the world of metal Additive Manufacturing from a commercial and technological perspective through:
GETTING A QUOTE WITH LK-MOULD IS FREE AND SIMPLE.
FIND MORE OF OUR SERVICES:
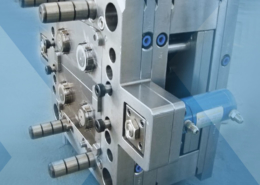
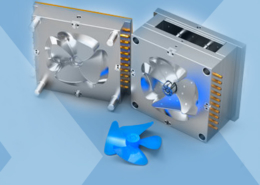
Plastic Molding

Rapid Prototyping
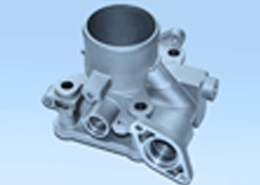
Pressure Die Casting
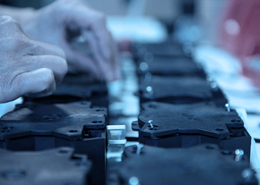
Parts Assembly
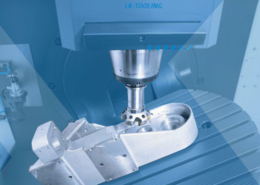