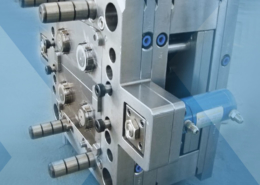
Homemade EDM Machine Moves From Prototype To Production - edm injection molding
Author:gly Date: 2024-09-30
Traditionally, 90% of parts weighing more than 100 g at Ecrimesa Group are manufactured by investment casting, since, at that size, the cost of the fine powders used in the MIM process is high, as well as the energy/time required to sinter them. However, due to the experience the group has accumulated in MIM, and the performance of the materials used, more and more parts weighing more than 100 g are being produced by MIM. The supply of the tooling required for MIM has also improved, allowing the technology to be used in wider range of cases. There are, of course, limits: using investment casting, parts weighing up to 25 kg can be produced, whereas, with MIM, the maximum realistic weight of a part is around 250 g.
HP’s Metal Jet has undergone significant refinement in the years since it was first unveiled in 2018. Now, by incorporating nearly the whole Bind...»
Compared to investment casting, which represents one of the oldest applied metal forming processes, Metal Injection Moulding is a relatively new technology, first commercialised in the 1980s and seeing wider adoption in the 1990s. To this day, investment casting is still one of the most widely used precision forming technologies, with MIM remaining far less known and, where it is applied, primarily being used for the manufacture of small parts.
With newer solutions coming to market and proving out their claims, injection molding is poised to lose some of its dominance in production.
As with any tool in a toolbox, nuance is vital to the appropriate application of solution to challenge. When all you have is a hammer, after all, everything looks like a nail. Today’s toolbox is substantially more robust, leaving us with options and the wherewithal to make informed decisions: When do I need a hammer? When do I need something else?
Today, Ecrimesa is comprised of three companies: its investment casting segment, Ecrimesa; the MIM company Mimecrisa; and machining company Mecansa. The companies are located across seven locations in Santander, on the northern Spanish coast. The three companies work closely together, benefitting from one another’s capabilities and expertise; for example, the tool shop at Ecrimesa provides toolmaking and tool maintenance services to Mimecrisa, along with access to its metallurgical and measuring labs, while Mecansa carries out finishing operations for Ecrimesa and Mimecrisa as required, and both Mimecrisa and Mecansa make use of Ecrimesa’s heat treatment facilities.
In 2021, in response to increasing demand for its MIM parts, the group invested €2 million in the commissioning of a new continuous MIM production line as part of its 2021/22 investment plan, to include a new continuous debinding and sintering furnace from Cremer, and injection moulding machines from Arburg, bringing its total installed MIM capacity to fourteen machines across four continuous lines and two vacuum sintering lines. The new line was scheduled to go into operation in the first quarter of 2022 and would allow Mimecrisa to process over 250 tons of MIM feedstock per year.
Ecrimesa Group, with facilities for both investment casting and MIM, used this expertise to fully understand the limitations and advantages of each process during the design transition, and bring this expertise to the customer. By taking advantage of the synergies between its different manufacturing capabilities, the group was able to accompany and support the customer across the full redesign and manufacturing process, from conception to finishing.
Finally, there are some additional criteria for deciding between investment casting and MIM. In general, it can be said that the development and production process of new parts is shorter with MIM, since there is no obligation to make multiple moulds and prototypes before starting production, which may be necessary when working with investment casting. In addition, the part design that a user begins with in the MIM process is generally closer to the final part, and machining processes are saved. Typically, parts manufactured by MIM have a very high surface quality without the need for finishing processes.
Tritone’s MoldJet is unique as an Additive Manufacturing process – not Binder Jetting, Material Extrusion, nor Material Jetting, the MoldJet pr...»
Injection molding is a well-understood and go-to manufacturing process, but naturally isn’t without its limitations. The learning curve and expense of setting up an IM installation are significant, as is the ramp-up time to actually producing a new design.
Mass production with 3D printing is making inroads in areas where it commercially makes sense, with hearing aids the most significant area of early widespread adoption. Consumers are walking on shoes with 3D printed midsoles, purchased at retail, or with personalized insoles made to fit their feet via a smartphone app. Medical products, like prosthetics and orthotics, can also be made specifically for a wearer. Produced together with traditional techniques, 3D printing supplements an overarching process to create next-generation end-use products.
Since the very first PM Titanium conference in Brisbane, Australia, in 2011, the PMTi series has been the essential meeting point where technical a...»
What had been overblown promises about a decade ago are now deliverables: Production, scale, quality, validation, and volume are now end-use realities.
3D printing’s sweet spot is in high-value, low-volume production, the opposite of injection molding. Here’s the good, bad, and ugly of both technologies, and advice on when it makes sense to pivot from one to the other.
Establishing and understanding the break-even point of cost-versus-quantity will often inform the decision for when to adopt which manufacturing process. Considerations obviously differ from batch sizes of 2 to 25 to 250 to 250,000.
The typical sintering conditions in Mimecrisa’s furnaces are suited to low-alloy steels, low-carbon FN08, low-alloy steel with elevated carbon 4605, 42CrMo4, 100Cr6, 17-4 PH and 316L stainless steel. A large proportion of its products are made from heat treated steels that require a higher carbon content; the production of these carbonaceous sintered steels poses a special challenge for many MIM manufacturers, as these materials require very precise control of the sintering atmosphere. In many cases, components made from these materials are hardened and tempered following sintering – an area in which Mimecrisa has a large deal of experience. Three carburising furnaces are available for case hardening and quench-and-temper heat treatments, with fine-tuned programs for MIM materials and small parts.
The new kid on the production block, 3D printing, can be an exciting meet-cute — new shapes, complex forms, high-value/low-volume production, all built layer by layer to increasingly exacting standards. Ideated since the 19th century, with modern patents tracing to the 1980s, 3D printing rethinks manufacturing from the first layer. More oversight, standards, and validation are seeing the technology move more into the production world and finally, finally begin fulfilling what had been overblown early promises.
A quick checklist of when it makes sense to pivot production toward AM would include parts that fall under some of these categories:
Reach a truly international audience that includes component manufacturers, end-users, industry suppliers, analysts, researchers and more.
Sarah Goehrke is the founder of AM-specific contract services company Additive Integrity and sits on the Board of Advisors for the Additive Manufacturing Coalition. She focuses in the additive manufacturing industry on advances in diversity, sustainability, and ecosystem positioning with a heightened focus on messaging. Goehrke has been a leader in the 3D-printing industry since 2014, previously serving as the Managing Editor of Fabbaloo; Editor-in-Chief of 3DPrint.com; and Senior Director, Strategic Communications and Ecosystems at ultrafast 3D-printing leader Nexa3D. Through Additive Integrity, she has worked with more than two dozen companies across the industry, contributed to publications including Forbes.com, and keynoted across three continents. She is deeply and actively passionate about advancing diversity, equity, and inclusion in the 3D-printing industry. Goehrke holds bachelor’s degrees in English and Theatre from Muskingum College, as well as a certificate in Diversity & Inclusion for HR from Cornell University.
The production floorspace at Mimecrisa is about 6,000 m2, staffed by around fifty employees, and all injection moulding machines are equipped with pick-and-place systems, some robotic. Using these pick-and-place systems, green parts are transferred to trays that fit into sinter boxes specifically designed for MIM-Master furnaces, meaning that green parts do not have to be handled until they exit the sintering furnace. In some cases, parts are placed on specially shaped ceramic supports, or setters, for improved dimensional stability. These supports are manufactured in-house.
Some preliminary ceramic setters were also used to support the green part during sintering (Fig. 5). Coining – the final operation to ensure flatness – was carried out on internally developed coining devices (Fig. 6). This step is necessary, even if sintering setters are optimised, to achieve narrow tolerances and avoid machining. Ecrimesa’s experience, gained from investment casting, helped the team to develop this coining device in house.
Sarah Goehrke is the founder of AM-specific contract services company Additive Integrity; serves on the Board of Directors and as the Head of DEI at Women in 3D Printing; and sits on the Board of Advisors for the Additive Manufacturing Coalition. She focuses in the additive manufacturing industry on advances in diversity, sustainability, and ecosystem positioning with a heightened focus on messaging. Goehrke has been a leader in the 3D-printing industry since 2014, previously serving as the Managing Editor of Fabbaloo; Editor-in-Chief of 3DPrint.com; and Senior Director, Strategic Communications and Ecosystems at ultrafast 3D-printing leader Nexa3D. Through Additive Integrity, she has worked with more than two dozen companies across the industry, contributed to publications including Forbes.com, and keynoted across three continents. She is deeply and actively passionate about advancing diversity, equity, and inclusion in the 3D-printing industry. Goehrke holds bachelor’s degrees in English and Theatre from Muskingum College, as well as a certificate in Diversity & Inclusion for HR from Cornell University.
Both technologies are applied to manufacture small parts that are generally more complex in design and, therefore, processes such as forging cannot be used. One of the main differences between investment casting and MIM is the range of materials that can be processed. In general, investment casting allows for a wider variety of materials, as the MIM process can only be performed with alloys of a higher melting temperature. Materials such as aluminium, for example, do not work efficiently with MIM.
Extensive MIM, CIM industry and sinter-based AM industry news, plus the following exclusive deep-dive articles and reports:
Founded in 1964 in Santander, Spain, the family-owned Ecrimesa Group began life as an industrial casting foundry. The name Ecrimesa is a compound of the Spanish Electro Crisol Metal S.A., translating as ‘Electric Metal Melting Crucible.’ The company was originally established for the production of steel and aluminium investment castings, but by 1994, Metal Injection Moulding was being developed at the location using the world’s first MIM-Master continuous furnaces for catalytic debinding and sintering, in collaboration with feedstock supplier BASF SE and the furnace’s manufacturer, Cremer Thermoprozessanlagen GmbH. MIM now comprises a major portion of the group’s offering.
The first versions of the MIM part that were injected and sintered showed some flow lines as a result of high binder levels. Some changes were needed following this first trial run to improve feedstock flow and avoid phase demixing, mainly at the injection areas with thin walls. Penetrant tests, used internally at Ecrimesa as a process control step during development, identified porosity areas in the first iteration of the part due to demixing and sintering deformation, pointing to the need to improve the strength of the green part using some additional ribs and extra wall thickness (Fig. 4).
Both the customer and Mimecrisa knew when this product was highlighted for transitioning to MIM that some work would be needed to optimise the part for the MIM process. Initially, the lack of obvious injection points was a particular challenge. Another consideration in the design’s adaption was the addition of ribs in place of some of the thin walls featured in the original design in order to lightweight the component and reduce material costs.
Overall, IM can reliably produce parts with known quality at high quantity — but it takes a while. When lower-volume end-use product runs are required, injection molding may add time and molding costs that counterbalance desirable ROI.
The biggest pro for additive manufacturing is perhaps also its biggest con: The sweet spot is in high-value, low-volume production. This is counterbalanced by injection molding’s sweet spot, which is just the opposite.
For all the new materials coming into AM — with giants like Arkema, BASF, Evonik, Henkel, Sabic, and many more dipping their toes in the 3D-printed waters — the overall portfolio is exponentially smaller compared to what’s available for traditional manufacturing.
Discover suppliers of these and more in our advertisers’ index and buyer’s guide, available in the back of PIM International.
Mimecrisa’s MIM plant operates fourteen injection moulding machines of different sizes, most of them electrical; four continuous MIM-Master debinding and sintering furnaces; and two batch vacuum furnaces and CIM furnaces. The facility also includes a fully equipped metallurgical and dimensional laboratory, and the principles of LEAN manufacturing and Industry 4.0 are evident throughout the business’s workflows.
Well-known as it may be, the design for manufacturing process for IM is lengthy and often non-linear. As a molding-based technology, IM relies on removable molds, which stifle the ability to design for low part counts and complex internal geometries. Further, creating those molds can add weeks to months to a production timeline.
Scale, speed, uniformity — injection molding ticks the right boxes for high-volume production. Able to reliably handle a huge array of materials, injection molding offers predictability and quality.
The use of Additive Manufacturing technologies for prototyping, such as metal MEX or metal Binder Jetting, is expected to help further speed up the development of such complex parts. While filament-based MEX techniques are not accurate enough to accurately replicate the finest design features, they can be of help in carrying out sintering tests prior to production. Binder Jetting can more closely match the MIM design as a ‘brown part’ with just a ‘backbone’ binder (though potential demixing or ‘injection memory’ issues will not be highlighted in such prototypes). In future, Ecrimesa plans to utilise these techniques for prototyping new MIM parts. Simulation techniques can also offer some capability to predict the injection path inside the mould, but some other important aspects are not covered by these techniques.
In this case study, Mimecrisa was tasked with transitioning a pair of door hinges from die casting to MIM. These corrosion-resistant hinges were originally manufactured from a zinc alloy. For safety reasons, the hinges must be able to open at up to 270° and, for cosmetic reasons, they need to be polished to a mirror finish.
The strongest use case for any manufacturing process is, at its heart, straightforward. Use what makes sense. There is no single solution to meet every challenge. Each part, each end-use product, has unique specifications and, in an ideal world, should be approached individually. Take the time to understand the exact needs, explore available solutions, and narrow down to what makes the most sense for your application in terms of expense, time, expertise, and final product.
The external face of the part was not changed during these modifications. The first iteration, with a 4 g weight increase from the original part, was good enough to be functional, but the customer ultimately preferred a bigger fatigue margin. The final iteration, taking into account the necessary changes, saw a weight increase of 2 g, necessary to avoid defects in the thin walls, increasing the fatigue life of the product whilst remaining compatible with the hinge’s function.
Today’s 3D printing is an indisputably industrial suite, though, with attainable production-level efficiency. Together with the processes, the ways in which we refer to the technology have matured. No longer is “3D printing” or the original “rapid prototyping” the phrase bandied about in most professional labs; now, “additive manufacturing” or, more casually, AM, is the go-to terminology, placing these layer-by-layer processes squarely in the manufacturing realm.
With capabilities in polymers, metals, pastes, and even bio-materials, there are few material areas that 3D printing hasn’t begun to explore. There is, naturally, a hefty chasm between lab exploration and real-world application, and that’s one that 3D printing has begun to bridge tidily.
Ecrimesa is one of the few companies to be able to offer its customers a choice of between investment casting, machining and MIM. This brings the opportunity to truly find the best process for an application, or to offer a wider choice of solutions as a part’s specifications evolve.
In many instances, a design developed for a conventional manufacturing process may be better suited for production by MIM. For example, a part previously produced by plastic injection moulding or die casting may no longer offer the required strength as the demands of the application increase. In cases such as these, Mimecrisa is able to offer increased value to the customer and increase MIM’s market share by employing its expertise to transition suitable parts made by competing technologies to MIM.
By 1997, Ecrimesa’s MIM operation had gown to such an extent that the company’s management took the decision to establish the independent company Mimecrisa, which would be responsible for the group’s MIM production facilities and workforce. In 2005, Ecrimesa Group bought out one of its machining suppliers in order to increase the added value of its production in investment casting and MIM. In summer 2015, this machining plant was moved to its own building.
While the original parts weighed around 100 g, and the MIM part close to 130 g, the cosmetic and mechanical properties achieved by transition to MIM allowed the customer to bring the product to higher quality markets. By cooperating closely with the customer, Mimecrisa was able to bring together the part’s necessary functionality with the required expertise in designing for MIM, and achieve the common goals of both parties. Where customer requirements can be fully agreed upon during the design phase, time to market and iteration cost can be reduced compared to collaboration carried out during the sampling process. The final assembled hinge set is shown in Fig. 7.
3D printing first made headlines as a half-Star Trek, half-everyman technology that brought science fiction to the kitchen table. Gassed-up media reports positioned the technology as an “anyone can make anything” process. Unsurprisingly, no such process exists with push-button precision. Mainstream perceptions dimmed, dismissing the technology.
As some of today’s largest applications, like the adidas 3D-printed midsole, highlight, the best ultimate solution is to use the technologies that make sense where they make sense. Often, this is a complementary, rather than an either-or, solution. 3D-printed injection molds, for instance, offer an interesting combination of desirable traits for an overall fitting solution.
The 2023 International Conference on Injection Moulding of Metals, Ceramics and Carbides (MIM2023), organised by the Metal Powder Industries Federa...»
In this case study, a part produced via die casting, typically produced with low-melting point alloys, was highlighted as a potential MIM candidate thanks to the customer’s need for higher mechanical and aesthetic properties. In order to transition the part successfully, a high degree of design work and process expertise was required in order to take full advantage of MIM’s capabilities and satisfy all of the customer’s requirements.
For better shape retention during sintering, the parts were produced using feedstock based on 316L master alloy powder. After considering the results of mechanical and dimensional trials on the first sintered samples with the customer, MIM moulds were modified in house to meet the part specifications. Throughout this process, cosmetic and assembly limitations were identified and noted for the next modification of the MIM parts.
The AM benefits for production are many. Complex internal structures can be incorporated directly into a single finished piece as the full product is produced at one time, reducing part counts as well as weak points of connection. Lightweighting, such as with lattice structures or simply through reduced part count, is desirable in weight-conscious industries like aerospace and automotive, where every ounce matters. A faster time-to-market is also a prime consideration as 3D printers can localize production. Importantly, 3D printing also forestalls the need for tooling, removing a time-intensive stage of many manufacturing processes. More validated materials are coming to market all the time, as well, bringing familiar materials to a new stable.
For higher-weight glass doors requiring a stronger hinge, a stainless steel version was developed for production by MIM (Figs. 2 and 3). A number of changes were made to adapt the design to MIM, focusing on the internal faces of the parts, which would not be visible to the user. These hinges are at the upper range of MIM’s size capabilities, with a typical weight of 50–80 g, and have very thin walls with a large surface area.
In 2020, Ecrimesa added Additive Manufacturing to its available technologies, enabling customers to manufacture wax prototypes for investment casting with short lead times, or additively manufacture parts using Fused Deposition Modelling (FDM), a form of Material Extrusion (MEX). The resulting parts can be sintered in Ecrimesa furnaces.
The free-to-access PIM International magazine archive offers unparalleled insight into the world of MIM, CIM and sinter-based AM from a commercial and technological perspective through:
Standards, while also coming more into play, are also lagging. Many potential adopters cannot even consider 3D printing, as defense and other government-mandated organizations are limited in the scope of processes on the table. Until more standards are recognized and more support comes from all levels — such as with President Biden’s 2022 AM Forward initiative expanding reach nationally, locally, and internationally — adoption will remain lower than theoretically possible.
The single most important thing to keep in mind when adopting AM is a simple one: Just because you can doesn’t always mean you should. It makes the most sense to stick with injection molding for:
Almost exclusively commercially available feedstocks, designed for catalytic debinding, are used, avoiding the need to invest in and maintain equipment for feedstock preparation, or the specific knowledge and expertise that goes along with this. All incoming feedstock deliveries are checked for compliance with specifications in the company’s materials laboratory, where chemical composition is analysed and standard samples are used to determine shrinkage. Differential thermal analysis equipment is also used to analyse binder decomposition rates and the amount of binder in the feedstock.
Tried and true, injection molding (IM) has made its stand for decades. Patented in the late 1800s, IM boomed decades later as WWII demanded low-cost, high-volume production. It can hardly be said to have slowed since. Nearly ubiquitous in modern manufacturing environments, IM is perhaps best described as the devil you know; it has its kinks and limitations, but it’s familiar and generally reliable. Could IM, though, be displaced by newcomer AM?
Aside from the choice of materials you want to work with, the decision between investment casting and MIM depends on other primary factors: the size of the part, the complexity of the part and the tolerances required, as well as the number of parts you want to manufacture. The ideal part for the MIM process has a length of less than 100 mm and is produced in batches of more than 5,000 pieces.
Don't miss any new issue of PIM International, and stay up to date with the latest industry news. Sign up to our fortnightly newsletter.
Further, bridge production is increasingly showing its value as 3D printing begins what injection molding can finish at scale. Especially critical during early days of the COVID-19 pandemic, when personal protective equipment (PPE) and necessary parts for ventilators were in short supply and need-it-now high demand, 3D printing stepped up to outfit medical professionals and patients with what they needed while IM ramped up to meet broader demand. Some remain in use, as 3D printing may have enhanced testing devices’ efficacy.
In general, most parts with a final weight of less than 15 g produced by Ecrimesa are – depending on the material – produced by MIM, since this technology allows thinner structures and is more material and energy efficient. However, there are still designers who, even for smaller parts, have a preference for investment casting.
While an IM setup can be a huge upfront investment, the ROI is huge as its use scales. Indeed, peer-reviewed research indicates that “Injection molding is the best way to mass-produce small, precise polymer components with complex shapes.”
AM remains a nascent technology, for all its recent growth and maturation. Adopting the technology for the first time requires a major learning curve as product designers well versed in DFM have a new skill set to gain in DfAM — design for additive manufacturing. Risk-averse sectors where validation is critical and new installations expensive in terms of training and investment are hesitant to adopt before they understand a full ROI. Often, adoption relies on a single internal champion, and AM-using departments tend to run as something of a startup inside an established company.
In so many ways, AM remains an unknown quantity. Fewer materials, lower adoption, less training, and slower absolute per-part speeds combine into a difficult formula for adoption. The perception for some “big players” to keep their AM investment and use close to the vest as a “secret sauce” competitive secret also holds back the capability for many AM suppliers to tout their biggest success stories.
GETTING A QUOTE WITH LK-MOULD IS FREE AND SIMPLE.
FIND MORE OF OUR SERVICES:
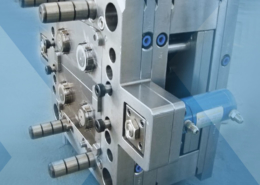
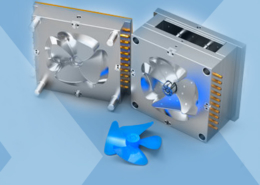
Plastic Molding

Rapid Prototyping
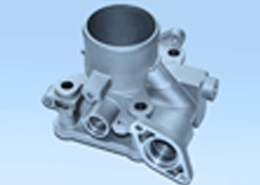
Pressure Die Casting
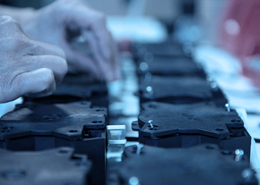
Parts Assembly
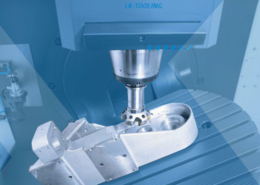