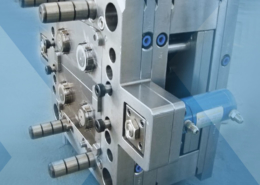
Home Plastic Injection Molding Offered on Kickstarter - molding plastic at home
Author:gly Date: 2024-09-30
To date, PET is the only packaging material which can be processed as a recycled material on an industrial scale to create food packaging. This innovation sees partner companies pave the way for removing the need to downcycle packaging products other than bottles, and opens an opportunity for recycling or upcycling. This would substantially extend the range of uses for PET and rPET. In addition to the bottle-to-bottle cycle, this also means that the establishment of bottle-to-cup or even a cup-to-bottle recycling is conceivable.
Under the European Plastics Pact, the intent is for all plastic packaging to contain 30% recycled material and to be 100% recycling capable by 2025. Typical materials used for packaging foods in thin-walled containers are polyolefins (polyethylene, polypropylene) or polystyrene.
By using our website and services, you expressly agree to the placement of our performance, functionality and advertising cookies. Learn more
Engel will present this technology and other developments at K 2022 in Düsseldorf, Germany, from Oct. 19 to 26, in booth C58 in Hall 15.
Aus was always 240V – indeed I often measure my power at 250V or so…. a while ago they theoretically changed it to ” 230 V (+10% to -6%), therefore providing an allowable voltage supply range between 253 V to 216 V” but I’m yet to ever see anything under 240..
Featuring a wall thickness of 0.32mm/0.013 inch, the transparent, round 125-mL containers are representative of a whole category of plastic packaging, especially in the food industry.
An Engel e-speed 280/50 injection molding machine is the heart of the production cell. Engel specifically developed this hybrid machine with its electrical clamping unit and hydraulic injection unit for the high-performance requirements of thin-wall injection molding.
Since the machine had been gathering dust and rust in the garage, fixing the machine up took a complete teardown to remove corrosion and resolve other issues. After this the original fault was identified, which turned out to be a shorted wire near the heater which had been turned up to a too high temperature, leading to the release of magic smoke and banishment of the machine to the Pit of Despair, AKA the shadowy depths of one’s garage.
In this first installment, [Michael] cleaned up the machine and restored it to a working state. In the next part injection molding will be attempted again, which should give some idea of the feasibility of turning scraps of PLA and failed 3D prints into smooth injection molded parts, assuming you have the CNC machine or patience to carve out the requisite molds, of course.
The first major electrical power plant in the US (and probably the world) was 110VDC. That was partially a limitation of the equipment and partially a safety limit – 110V was considered low enough to not be immediately deadly if you touched it.
In cooperation with partners Alpla Group, Brink Recycling, IPB Printing, injection molding machine manufacturer Engel is presenting a step forward for the packaging industry at K 2022 by processing recycled material, rPET, at its stand. Featured will be an Engel e-speed injection molding machine with a newly developed and extremely powerful injection unit.
An Engel spokesperson tells PlasticsToday that, among others, “the [rPET] cups can be used for food products such as dairy products, gourmet salads, or sandwich spreads.”
As in many things, the US was ahead of the times. The solutions were suboptimal, but were kept because switching to a better system would have cost too much. The rest of the world followed, but learned from the mistakes made in the US.
When AC equipment became available, the US stuck with 110VAC. The 110VDC light bulbs and other appliances could run on 110VAC easily enough.
Engel and partners’ development yields thin-walled food containers made in a single injection-molding step using up to 100% recycled PET.
The new model 280 e-speed high-performance injection unit for K 2022 (shown above) achieves injection speeds up 1,400 mm/55 inches per second at a maximum injection pressure of up to 2,600 bar when processing small shot weights with an extreme wall-thickness-to-flow-path ratio.
When [Michael] over at the Teaching Tech YouTube channel bought a hobby injection molding machine a long time ago, one of the plans he had with it was to use it for grinding up waste bits of PLA filament for injection molding. Since the machine was bought from a US shop and [Michael] is based in Australia it required some modifications to adapt it to the local 220+ VAC mains, followed by adding a PID temperature controller and a small compressor to provide the compressed air rather than from a large shop compressor.
Until now, it has only been possible to process PET in thick-walled parts such as bottle preforms in injection molding. In that standard process, the final packaging format was created in a second step of the process — by blow molding, for example.
The modified rPET being processed at the K show is sourced from PET beverage bottles recycled in the plants of packaging and recycling specialists ALPLA Group, which is headquartered in Hard, Austria. Other partner companies involved in the show exhibit are Brink (Harskamp, Netherlands) for the mold and IML automation and IPB Printing (Reusel, Netherlands) for the labels.
110V is somewhat safer than 230V. The US had to much invested in 110V by the time 230V was available to make a switch over economical.
Although [Michael] had discussed using the machine for PLA with the seller to confirm that this would work, a user error meant that the now defective unit had been sitting idly for many years, until recently.
We are still very firmly stuck at the barely useable (for workshop and large appliance use) 100V here in Japan. You can get 200V split phase if you need more power, but that’s still significantly less than what my toaster ran on back in Australia…
For the first time, thin-walled containers made of PET, specifically recycled PET (rPET), can be produced in a single injection-molding process step.
Rick Lingle is Senior Technical Editor, Packaging Digest and PlasticsToday. He’s been a packaging media journalist since 1985 specializing in food, beverage and plastic markets. He has a chemistry degree from Clarke College and has worked in food industry R&D for Standard Brands/Nabisco and the R.T. French Co. Reach him at [email protected] or 630-481-1426.
Also, recycling schemes for these materials lack the approval of the European food authority, European Food Safety Authority (EFSA). rPET offers a solution for avoiding penalties and special taxes. Although the price for PET is currently high, this concept makes the material a cost-effective alternative. EFSA has approved numerous recycling processes for PET, thus ensuring that rPET is available in Europe.
The dyes used on in-mold labels for the American market and its requirements can be washed off as the intent is to recycle the labels and the packaging.
With the split-phase system, the US has 220 availabe for all major appliances. You can even get 220 outlets installed for larger window AC units.
To process rPET, Engel combines the new injection unit with a plasticizing unit from in-house development and production specifically designed for processing recycled material. During plasticizing and injection, the viscosity of the PET is configured for thin-wall injection molding. The new Engel e-speed supports the processing of arbitrary recycled materials up to 100% rPET.
I suspect the cost of not doing the change has been much much higher than the cost of doing it would have been.. The same with metric. I remember when Aus changed, and yes it was a lot of work. But it was done, and after 50 years nobody would think any different – the US should have done it inthe same time frame.. But yes, I agree, voltage is different, but if you look around the world the US is the only major economy with the low voltage..
A different technology is used in Europe: an in-mold label that floats during the recycling process makes it easy to separate the dyes and the label from the PET.
Engel is presenting a mold at the K show which can process different labels at the same time. This sees the partners respond to the globally different trends in in-mold labeling which are in line with the EPBP and/or Recyclass recommendations in the EU, and with the specifications from the Association of Plastic Recyclers (APR) for the USA.
With the use of integrated in-mold labeling (IML), the containers are ready-for-filling as soon as they leave the production cell. The special feature in this application is the material. The thin-walled containers are produced directly from rPET in a single step.
GETTING A QUOTE WITH LK-MOULD IS FREE AND SIMPLE.
FIND MORE OF OUR SERVICES:
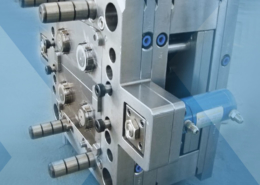
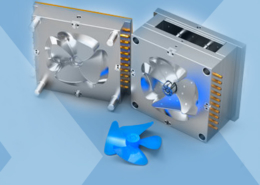
Plastic Molding

Rapid Prototyping
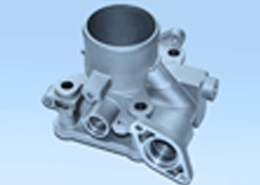
Pressure Die Casting
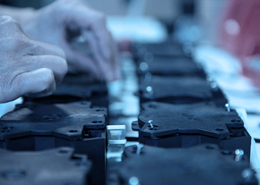
Parts Assembly
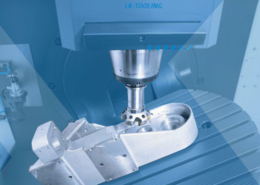