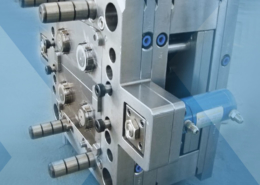
Exploring Plastic Molding for Wire 1 2: Crafting Precision Solutions
Author:gly Date: 2024-06-08
Plastic molding for wire 1 2 embodies a fascinating fusion of engineering prowess and material science, offering unparalleled precision and versatility in the fabrication of wire components. This innovative process holds immense potential across various industries, from electronics to automotive, revolutionizing manufacturing paradigms and enabling the realization of intricate designs. Let's embark on a journey to unravel the intricacies of plastic molding for wire 1 2, exploring its mechanisms, applications, and implications.
Introduction: A Prelude to Precision
Plastic molding for wire 1 2 represents a pinnacle of modern manufacturing, leveraging advanced techniques to mold plastic materials into intricate wire components with micron-level precision. Rooted in the principles of injection molding, this process entails the heating and injection of molten plastic into precisely crafted molds, where it assumes the desired shape and form. Its ability to accommodate complex geometries and tight tolerances makes it indispensable in the production of wire components for diverse applications.
Operating Mechanisms: Precision in Practice
At the heart of plastic molding for wire 1 2 lies a meticulously orchestrated sequence of operations designed to achieve optimal results. The process begins with the selection of suitable thermoplastic materials, chosen for their mechanical properties, thermal stability, and compatibility with the intended application. These materials are then subjected to controlled heating, transforming them into a molten state conducive to molding. Subsequently, the molten plastic is injected into precision-engineered molds under high pressure, ensuring uniform distribution and fidelity to design specifications. Post-molding, the components undergo cooling and solidification, culminating in the extraction of flawless wire products ready for further processing or assembly.
Applications Across Industries: Versatility Unveiled
Plastic molding for wire 1 2 finds myriad applications across a spectrum of industries, each harnessing its capabilities to address unique challenges and requirements. In the realm of electronics, it facilitates the production of miniature connectors, cable assemblies, and insulating components essential for the seamless functioning of electronic devices. In the automotive sector, it enables the fabrication of wire harnesses, sensor housings, and interior trim components, enhancing vehicle performance, safety, and aesthetics. Moreover, its versatility extends to the medical field, where it is utilized in the manufacture of surgical instruments, diagnostic devices, and implantable devices, leveraging biocompatible materials and precision molding techniques to ensure patient well-being and regulatory compliance.
Advancements and Innovations: Pioneering the Future
The landscape of plastic molding for wire 1 2 is continually evolving, driven by a relentless pursuit of innovation and excellence. Advancements in material science, such as the development of high-performance polymers and bio-based resins, expand the scope of applications while enhancing sustainability and environmental stewardship. Furthermore, the integration of digital technologies, such as computer-aided design (CAD) and simulation software, empowers designers and engineers to optimize mold designs, minimize cycle times, and mitigate defects. Additive manufacturing techniques, such as 3D printing, complement traditional molding processes, offering rapid prototyping and customization capabilities that accelerate product development cycles and foster creativity.
Quality Assurance and Compliance: Upholding Standards
In the realm of manufacturing, quality assurance is paramount, ensuring that products meet rigorous standards of performance, reliability, and safety. Plastic molding for wire 1 2 is no exception, subject to stringent quality control measures and regulatory requirements. Robust inspection protocols, including dimensional analysis, visual inspection, and mechanical testing, validate the integrity of molded components and detect any deviations from specifications. Moreover, adherence to industry standards and certifications, such as ISO 9001 and IATF 16949, instills confidence in the quality and consistency of manufactured products, fostering trust among customers and stakeholders.
Environmental Considerations: Toward Sustainable Solutions
As sustainability emerges as a focal point in manufacturing, plastic molding for wire 1 2 confronts the imperative of minimizing environmental impact and promoting resource efficiency. Manufacturers are increasingly embracing eco-friendly materials, recycling initiatives, and energy-efficient processes to reduce carbon footprint and waste generation. Furthermore, lifecycle assessments and eco-design principles guide product development, optimizing material usage and end-of-life management while mitigating environmental risks. By embracing sustainable practices and circular economy principles, the plastic molding industry can contribute to a greener, more sustainable future.
Future Outlook: Navigating Opportunities and Challenges
Looking ahead, the future of plastic molding for wire 1 2 brims with opportunities and challenges, beckoning industry stakeholders to embrace innovation and adaptation. Emerging trends, such as the rise of smart manufacturing and the Internet of Things (IoT), present new frontiers for integration and connectivity, driving demand for advanced wire components with enhanced functionality and performance. Moreover, the advent of Industry 4.0 technologies, such as artificial intelligence and robotics, promises to revolutionize production processes, unlocking unprecedented levels of efficiency, flexibility, and agility. However, amidst these technological advancements, the industry must grapple with issues of cybersecurity, intellectual property protection, and talent acquisition, safeguarding against potential risks and vulnerabilities.
Conclusion: A Tapestry of Innovation and Excellence
In conclusion, plastic molding for wire 1 2 stands as a testament to human ingenuity and technological prowess, shaping the fabric of modern manufacturing with its precision, versatility, and reliability. From its humble beginnings to its transformative impact on industries worldwide, it exemplifies the spirit of innovation and the relentless pursuit of excellence. As we navigate the complexities of an ever-evolving landscape, let us harness the power of plastic molding to craft a future defined by progress, sustainability, and shared prosperity. With creativity, collaboration, and unwavering dedication, we can unlock new horizons of possibility and forge a path toward a brighter tomorrow.
GETTING A QUOTE WITH LK-MOULD IS FREE AND SIMPLE.
FIND MORE OF OUR SERVICES:
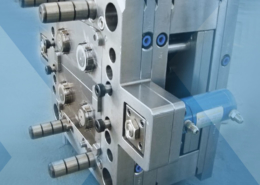
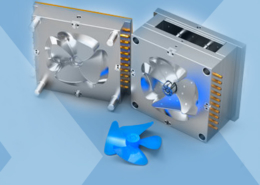
Plastic Molding

Rapid Prototyping
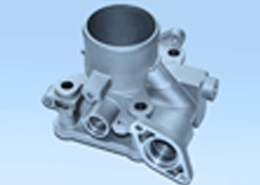
Pressure Die Casting
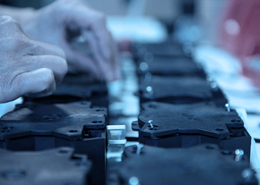
Parts Assembly
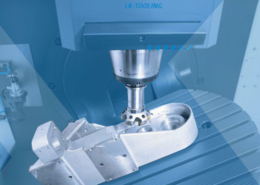