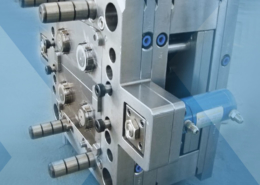
Exploring Plastic Molding: Revolutionizing Manufacturing
Author:gly Date: 2024-06-08
Introduction
Plastic molding stands as a cornerstone in modern manufacturing, revolutionizing the production of countless everyday items. From the ubiquitous plastic bottles to intricate automotive components, plastic molding techniques have reshaped industries worldwide. Understanding the intricacies of plastic molding not only unveils the engineering marvels behind mass production but also sheds light on the environmental and economic implications of this technology.
The Evolution of Plastic Molding
Plastic molding has evolved significantly since its inception. Initially, limited to basic shapes and materials, it has now transcended boundaries, enabling the creation of complex geometries with a myriad of polymers. With advancements in materials science and manufacturing technologies, modern plastic molding techniques offer unparalleled precision and efficiency.
Plastic molding has diversified into various methods, including injection molding, blow molding, and compression molding. Each technique caters to specific requirements, offering unique advantages in terms of production speed, cost-effectiveness, and design flexibility.
Injection Molding: Precision Engineering at Scale
Injection Molding Process
Injection molding dominates the landscape of plastic manufacturing due to its versatility and efficiency. The process involves injecting molten plastic into a mold cavity, where it solidifies to form the desired shape. This method excels in producing intricate parts with high precision and repeatability, making it indispensable in industries ranging from consumer goods to medical devices.
Advancements in Injection Molding
Recent advancements in injection molding technology have further enhanced its capabilities. From multi-material molding to micro-injection molding, manufacturers can now achieve unprecedented levels of complexity and functionality in their products. Moreover, innovations such as in-mold labeling and overmolding have opened new avenues for product design and customization.
Sustainability in Injection Molding
While injection molding offers unparalleled efficiency in mass production, it also poses environmental challenges due to the reliance on petroleum-based plastics. However, the industry is actively embracing sustainable practices, with initiatives like recyclable materials and energy-efficient processes gaining traction. By prioritizing sustainability, injection molding can continue to thrive while minimizing its ecological footprint.
Blow Molding: Shaping the Future of Packaging
Blow Molding Techniques
Blow molding specializes in the production of hollow objects, such as bottles and containers, by inflating a heated plastic parison within a mold cavity. This process ensures uniform thickness and strength, making it ideal for packaging applications where durability and aesthetics are paramount.
Advantages of Blow Molding
The inherent advantages of blow molding, including lightweight construction and excellent barrier properties, have cemented its position as the preferred choice for beverage and food packaging. Furthermore, advancements in material formulations have expanded the scope of blow molding to encompass eco-friendly alternatives like bioplastics, paving the way for a more sustainable future.
Innovations in Blow Molding
Continual innovation drives the evolution of blow molding, with developments such as extrusion blow molding and stretch blow molding pushing the boundaries of what is achievable. These techniques enable manufacturers to produce complex shapes and incorporate features like handles and threads directly into the mold, streamlining production and enhancing functionality.
Conclusion
In conclusion, plastic molding stands as a testament to human ingenuity, facilitating the creation of diverse products that enrich our daily lives. By delving into the intricacies of injection molding and blow molding, we gain insight into the symbiotic relationship between technology, sustainability, and innovation. As we navigate the challenges of the 21st century, embracing the principles of responsible manufacturing will be pivotal in shaping a more resilient and equitable future.
Through continuous research and collaboration, we can unlock new frontiers in plastic molding, addressing pressing issues such as material waste and energy consumption. By harnessing the power of technology and sustainability, we can propel the manufacturing industry towards greater efficiency and environmental stewardship, ensuring a legacy of progress for generations to come.
GETTING A QUOTE WITH LK-MOULD IS FREE AND SIMPLE.
FIND MORE OF OUR SERVICES:
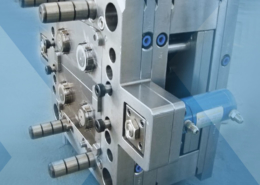
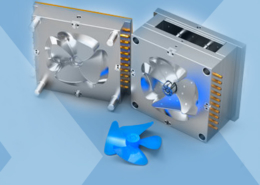
Plastic Molding

Rapid Prototyping
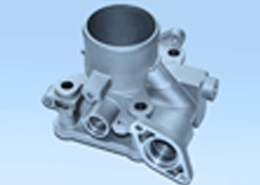
Pressure Die Casting
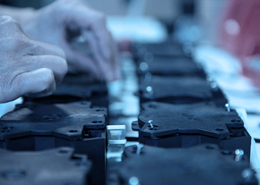
Parts Assembly
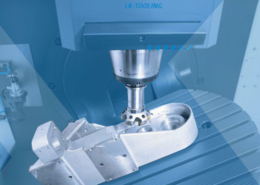