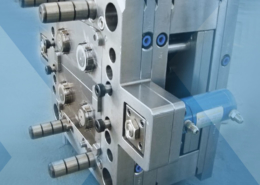
Plastic Molding Cost: Unraveling the Economics Behind Production
Author:gly Date: 2024-06-08
Plastic molding cost stands at the forefront of manufacturing considerations, wielding significant influence over product viability, pricing strategies, and overall profitability. As industries increasingly turn to plastic molding for its versatility and efficiency, understanding the intricacies of its cost dynamics becomes imperative. This article delves into the multifaceted landscape of plastic molding cost, exploring its determinants, implications, and strategies for optimization.
Determinants of Plastic Molding Cost
Plastic molding cost is shaped by a multitude of factors, each exerting varying degrees of influence on the overall expense. Material selection, tooling expenses, production volume, and design complexity emerge as pivotal determinants.
Material Selection:
The choice of plastic material significantly impacts molding cost, with commodity plastics offering affordability but limited performance, while engineering-grade polymers command higher prices due to superior properties such as strength and heat resistance.
Tooling Expenses:
Tooling, comprising molds and dies, constitutes a substantial upfront investment in plastic molding. The complexity of the part design, mold material, and required precision dictate tooling costs, often necessitating a balance between quality and affordability.
Production Volume:
Economies of scale play a crucial role in molding cost, with higher production volumes amortizing fixed expenses over a larger output, thereby reducing per-unit costs. Conversely, low-volume production tends to incur higher costs per unit due to the inability to leverage scale advantages.
Design Complexity:
The intricacy of part geometry directly correlates with molding complexity and, consequently, cost. Simple, uniform designs facilitate streamlined molding processes, whereas complex geometries necessitate specialized techniques and additional processing steps, driving up expenses.
Strategies for Cost Optimization
Despite the inherent complexities of plastic molding cost, manufacturers can adopt strategic approaches to mitigate expenses and enhance competitiveness.
Material Optimization:
Careful selection of plastic materials based on performance requirements and cost considerations can yield substantial savings without compromising product quality. Engaging in material substitution or utilizing recycled plastics presents viable avenues for cost reduction.
Tooling Efficiency:
Investing in high-quality, durable molds and adopting advanced tooling technologies optimizes production efficiency and minimizes downtime, thereby maximizing the return on tooling investment over the long term.
Process Optimization:
Streamlining manufacturing processes through automation, lean principles, and continuous improvement initiatives enhances operational efficiency, reduces cycle times, and lowers per-unit production costs.
Design for Manufacturability (DFM):
Collaboration between design engineers and molders early in the product development phase facilitates the creation of designs optimized for manufacturability, thereby minimizing molding complexities and associated costs.
Implications of Plastic Molding Cost
The ramifications of plastic molding cost reverberate throughout the manufacturing ecosystem, influencing pricing strategies, supply chain dynamics, and market competitiveness.
Pricing Strategies:
Molding cost directly influences product pricing strategies, necessitating a delicate balance between cost recovery and market competitiveness. Manufacturers must factor in both internal cost structures and external market dynamics to establish pricing models that ensure profitability while remaining attractive to consumers.
Supply Chain Dynamics:
Fluctuations in molding cost can disrupt supply chain dynamics, impacting supplier relationships, lead times, and inventory management strategies. Proactive risk mitigation measures, such as diversifying sourcing options and maintaining strategic supplier partnerships, can mitigate the adverse effects of cost volatility.
Market Competitiveness:
The ability to effectively manage molding cost confers a competitive advantage in the marketplace, enabling manufacturers to offer quality products at competitive prices while safeguarding profit margins. Continuous cost optimization efforts ensure sustained competitiveness amidst evolving market conditions.
Conclusion: Navigating the Economics of Plastic Molding Cost
In conclusion, plastic molding cost stands as a pivotal consideration in manufacturing, exerting profound influences on product economics, operational efficiency, and market competitiveness. By understanding the determinants, implications, and strategies for cost optimization, manufacturers can navigate the complexities of plastic molding cost effectively, driving sustainable growth and profitability in an increasingly competitive landscape. As industries continue to innovate and evolve, ongoing research and investment in cost-saving technologies and methodologies will be critical to achieving long-term success in plastic molding operations.
GETTING A QUOTE WITH LK-MOULD IS FREE AND SIMPLE.
FIND MORE OF OUR SERVICES:
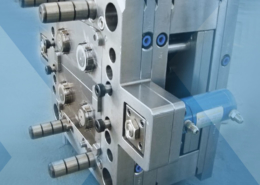
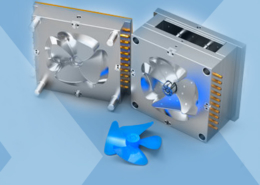
Plastic Molding

Rapid Prototyping
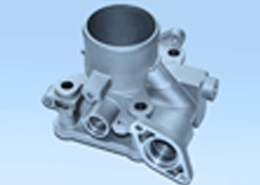
Pressure Die Casting
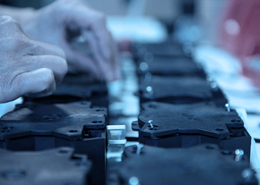
Parts Assembly
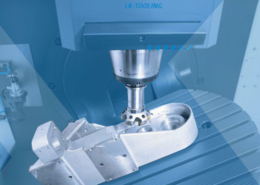