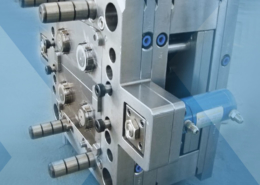
Functional Injection Molds (and More) from 3D Printed Metal Paste - injection mo
Author:gly Date: 2024-09-30
In this collection of content, we provide expert advice on welding from some of the leading authorities in the field, with tips on such matters as controls, as well as insights on how to solve common problems in welding.
In this collection of articles, two of the industry’s foremost authorities on screw design — Jim Frankand and Mark Spalding — offer their sage advice on screw design...what works, what doesn’t, and what to look for when things start going wrong.
Processors with sustainability goals or mandates have a number of ways to reach their goals. Biopolymers are among them.
Despite price increase nominations going into second quarter, it appeared there was potential for generally flat pricing with the exception of a major downward correction for PP.
After successfully introducing a combined conference for moldmakers and injection molders in 2022, Plastics Technology and MoldMaking Technology are once again joining forces for a tooling/molding two-for-one.
Start by picking a target melt temperature, and double-check data sheets for the resin supplier’s recommendations. Now for the rest...
Join KraussMaffei for an insightful webinar designed for industry professionals, engineers and anyone interested in the manufacturing processes of PVC pipes. This session will provide a comprehensive understanding of the technology behind the production of high-quality PVC pipes: from raw material preparation to final product testing. Agenda: Introduction to PVC extrusion: overview of the basic principles of PVC pipe extrusion — including the process of melting and shaping PVC resin into pipe forms Equipment and machinery: detailed explanation of the key equipment involved — such as extruders, dies and cooling systems — and their roles in the extrusion process Process parameters: insight into the critical process parameters like temperature, pressure and cooling rates that influence the quality and consistency of the final PVC pipes Energy efficiency: examination of ways to save material and energy use when extruding PVC pipe products
Resin drying is a crucial, but often-misunderstood area. This collection includes details on why and what you need to dry, how to specify a dryer, and best practices.
Exhibitors and presenters at the plastics show emphasized 3D printing as a complement and aid to more traditional production processes.
This is an issue whenever you change jobs to a new mold with a different resin. Are the two resins compatible or do they react with one another? No matter how hard you try to purge the previous resin from the system, small amounts will remain on the screw flights. Purging compound may help, but even a small residual amount of the previous resin can provide a catalytic effect. For example, if you accidently mix acetal (POM) with PVC, you and the rest of the people on the shop floor will have an extremely unpleasant emotional and physical experience. Small amounts of either of these two resins catalyzes the decomposition of the other polymer to gases.
The consolidation press developed by Engel in cooperation with its partner Fill (Gurten, Austria) can be used to consolidate fiber stacks with deliberate fiber orientation and different wall thicknesses. All process steps are automated. All told, the consolidation process integrates inserting the fiber stack into the mould, transferring the closed mold to the heating press, heating, transferring the mold to the cooling press, consolidation, cooling and transferring to the initial station, where the mold is opened, the consolidated semi-finished product (blank) removed and a new fiber stack inserted so that the cycle can start again.
While prices moved up for three of the five commodity resins, there was potential for a flat trajectory for the rest of the third quarter.
Gifted with extraordinary technical know how and an authoritative yet plain English writing style, in this collection of articles Fattori offers his insights on a variety of molding-related topics that are bound to make your days on the production floor go a little bit better.
Introduced by Zeiger and Spark Industries at the PTXPO, the nozzle is designed for maximum heat transfer and uniformity with a continuous taper for self cleaning.
Because of the growth of the plastics industry, there has been an uptick in number of new hires for processing plastics over the last few years. With new employees comes the challenge of training—not only on company policies and processing duties, but on safety. With that in mind, this column will focus on a topic I feel does not get sufficient attention. In fact, it is a topic on which most of us do not have all the details needed. In my experience, searches on the internet certainly proved inadequate. That topic is the mixing of different resins in the barrel, hot runners, and hot tips.
To be cost-effective in large-scale production, the stacks must be made and consolidated inline and within the cycle of the injection molding process. As a system supplier, Engel is in a position to offer integrated and fully automated solutions for the entire process – from individual tapes through to functionalisation in the injection moulding process – from a single source.
The aim of this presentation is to guide you through the factors and the numbers that will help you determine if a robot is a smart investment for your application. Agenda: Why are you considering automation? What problems are you trying to solve? How and why automation can help Crunch the numbers and determine the ROI
Multiple speakers at Molding 2023 will address the ways simulation can impact material substitution decisions, process profitability and simplification of mold design.
Additive technology creates air pockets in film during orientation, cutting down on the amount of resin needed while boosting opacity, mechanical properties and recyclability.
Join Wittmann for an engaging webinar on the transformative impact of manufacturing execution systems (MES) in the plastic injection molding industry. Discover how MES enhances production efficiency, quality control and real-time monitoring while also reducing downtime. It will explore the integration of MES with existing systems, emphasizing compliance and traceability for automotive and medical sectors. Learn about the latest advancements in IoT and AI technologies and how they drive innovation and continuous improvement in MES. Agenda: Overview of MES benefits What is MES? Definition, role and brief history Historical perspective and evolution Longevity and analytics Connectivity: importance, standards and integration Advantages of MES: efficiency, real-time data, traceability and cost savings Emerging technologies: IoT and AI in MES
Join Engel in exploring the future of battery molding technology. Discover advancements in thermoplastic composites for battery housings, innovative automation solutions and the latest in large-tonnage equipment designed for e-mobility — all with a focus on cost-efficient solutions. Agenda: Learn about cutting-edge thermoplastic composites for durable, sustainable and cost-efficient battery housings Explore advanced automation concepts for efficient and scalable production See the latest large-tonnage equipment and technology innovations for e-mobility solutions
Besides organic sheets, Engel’s organomelt technology is also suitable for unidirectional (UD) glass and/or carbon fiber reinforced tapes with thermoplastic matrixes. Tapes make it possible to design semi-finished products in line with requirements and thus make even better use of the components' lightweight design potential. The components are either partially reinforced with just a few tapes or are produced from tape stacks several millimeters thick.
This month’s resin pricing report includes PT’s quarterly check-in on select engineering resins, including nylon 6 and 66.
Mixed in among thought leaders from leading suppliers to injection molders and mold makers at the 2023 Molding and MoldMaking conferences will be molders and toolmakers themselves.
The two half-shells are produced in the same mold in a one-shot process. For this purpose, the two organic sheets are simultaneously heated in the IR oven, inserted into the mold, shaped there and directly “functionalized” by means of an injection molding process taking place in the same mold. The Tepex dynalite type organic sheets provided by Bond Laminates are based on glass fibers in a polypropylene matrix. Glass-fiber reinforced polypropylene is also used for overmolding.
Stephen has been with PlasticsToday and its preceding publications Modern Plastics and Injection Molding since 1992, throughout this time based in the Asia Pacific region, including stints in Japan, Australia, and his current location Singapore. His current beat focuses on automotive. Stephen is an avid folding bicycle rider, often taking his bike on overseas business trips, and is a proud dachshund owner.
Plastics Technology covers technical and business Information for Plastics Processors in Injection Molding, Extrusion, Blow Molding, Plastic Additives, Compounding, Plastic Materials, and Resin Pricing. About Us
Implementing a production monitoring system as the foundation of a ‘smart factory’ is about integrating people with new technology as much as it is about integrating machines and computers. Here are tips from a company that has gone through the process.
Mold maintenance is critical, and with this collection of content we’ve bundled some of the very best advice we’ve published on repairing, maintaining, evaluating and even hanging molds on injection molding machines.
ABOUT THE AUTHOR: John Bozzelli is the founder of Injection Molding Solutions (Scientific Molding) in Midland, Mich., a provider of training and consulting services to injection molders, including LIMS, and other specialties. Contact john@scientificmolding.com; scientificmolding.com.
You will hear true stories of hoppers being blown to and through roofs, endcaps blown through walls, etc. The gases produced upon resin decomposition generate extreme pressures, which can and do blow injection molding machine barrels into shrapnel. The accompanying photo shows the front zone of a machine barrel that blew into pieces. Imagine the damage if it had hit someone! This may not happen often, but it does occur, and you need to be aware its possibility.
The processing and functionalization of thermoplastic continuous fiber-reinforced semi-finished products, such as thermoplastic fabrics or UD tapes, using the Engel organomelt process will be one key focus at Engel's trade fair stand this year at Composites Europe 2018. The world's first large-scale application has been launched in the US. Valeo Front End Modules manufactures front-end carriers with integrated air ducts for a renowned German OEM in Smyrna, Tennessee, believed to be Volkswagen in Chattanooga, Tennessee. In July of this year, the structural components won an Automotive Award from the Society of Plastics Engineers (SPE) for their innovative production based on organic sheets and its outstanding properties. The parts contain a high organic sheet fraction, resulting in significant weight savings and improved crash performance. In addition, it was possible to integrate the air ducts directly into the support using a double-shell structure.
Plastics Technology’s Tech Days is back! Every Tuesday in October, a series of five online presentations will be given by industry supplier around the following topics: Injection Molding — New Technologies, Efficiencies Film Extrusion — New Technologies, Efficiencies Upstream/Downstream Operations Injection Molding — Sustainability Extrusion — Compounding Coming out of NPE2024, PT identified a variety of topics, technologies and trends that are driving and shaping the evolution of plastic products manufacturing — from recycling/recyclability and energy optimization to AI-based process control and automation implementation. PT Tech Days is designed to provide a robust, curated, accessible platform through which plastics professionals can explore these trends, have direct access to subject-matter experts and develop strategies for applying solutions in their operations.
Of course, safety in injection molding extends beyond material compatibility. High temperatures and pressures of 20,000 to 45,000 psi are needed to melt and inject plastic into complex shapes. While these machines are built robustly to handle these temperatures and pressures, it’s best take a serious look at the equipment on a regular basis and not assume all is OK. Do you review the machine/mold upon startup or during production to make sure these pressures and temperatures do not reach out and touch you or a coworker? For example, does the nozzle tip mate properly with the sprue bushing? Is a temperature zone overriding?
At Composites Europe 2018, Engel is setting a further milestone on the road to economical production of thermoplastic composites: The Engel organomelt process is being used for the first time world-wide in the large-scale production of front-end carriers with integrated air ducts.
Sustainability continues to dominate new additives technology, but upping performance is also evident. Most of the new additives have been targeted to commodity resins and particularly polyolefins.
The tape stacking cell developed by Engel uses high-resolution camera technology to produce precise stacks from tape blanks.
The consolidation press can be seamlessly integrated into the overall process, which significantly increases efficiency in the production of tailor-made tape solutions.
Join this webinar to explore the transformative benefits of retrofitting your existing injection molding machines (IMMs). Engel will guide you through upgrading your equipment to enhance monitoring, control and adaptability — all while integrating digital technologies. You'll learn about the latest trends in IMM retrofitting (including Euromap interfaces and plasticizing retrofits) and discover how to future-proof your machines for a competitive edge. With insights from industry experts, it'll walk you through the decision-making process, ensuring you make informed choices that drive your business forward. Agenda: Maximize the value of your current IMMs through strategic retrofitting Learn how to integrate digital technologies to enhance monitoring and control Explore the benefits of Euromap interfaces and plasticizing retrofits Understand how retrofitting can help meet new product demands and improve adaptability Discover how Engel can support your retrofitting needs, from free consultations to execution
Determining the source of streaking or contamination in your molded parts is a critical step in perfecting your purging procedures ultimately saving you time and money.
Pick-and-place stacking technology with optical image processing offers highly flexible use. The tapes can have almost arbitrary widths and contours. Because the stacks obtain their shape required for the component during stacking, consolidation can be followed by forming and functionalisation in the injection moulding step without the need for intermediate trimming. Engel is already using this kind of solution for the manufacturing of its own products. The rotation arm of the e-pic robot consists of carbon fiber reinforced tapes.
While the major correction in PP prices was finally underway, generally stable pricing was anticipated for the other four commodity resins.
I’ve developed a list of plastics that I know could possibly react with one another. My bet is there are others that I do not know about. If you know of any others, please let me know.
technotrans says climate protection, energy efficiency and customization will be key discussion topics at PTXPO as it displays its protemp flow 6 ultrasonic eco and the teco cs 90t 9.1 TCUs.
Coverage of single-use plastics can be both misleading and demoralizing. Here are 10 tips for changing the perception of the plastics industry at your company and in your community.
Extrusion simulations can be useful in anticipating issues and running “what-if” scenarios to size extruders and design dies for extrusion projects. It should be used at early stages of any project to avoid trial and error and remaking tooling.
In this collection, which is part one of a series representing some of John’s finest work, we present you with five articles that we think you will refer to time and again as you look to solve problems, cut cycle times and improve the quality of the parts you mold.
Ultradent's entry of its Umbrella cheek retractor took home the awards for Technical Sophistication and Achievement in Economics and Efficiency at PTXPO.
This Knowledge Center provides an overview of the considerations needed to understand the purchase, operation, and maintenance of a process cooling system.
Across the show, sustainability ruled in new materials technology, from polyolefins and engineering resins to biobased materials.
The resulting acrid odor is well known to Crusty Sr., my archetype of the grizzled processor. Find someone who has some experience processing PVC or acetal; ask about his or her experiences.
Successfully starting or restarting an injection molding machine is less about ticking boxes on a rote checklist and more about individually assessing each processing scenario and its unique variables.
Thousands of people visit our Supplier Guide every day to source equipment and materials. Get in front of them with a free company profile.
In this three-part collection, veteran molder and moldmaker Jim Fattori brings to bear his 40+ years of on-the-job experience and provides molders his “from the trenches” perspective on on the why, where and how of venting injection molds. Take the trial-and-error out of the molding venting process.
Discover how artifical intelligence is revolutionizing plastics processing. Hear from industry experts on the future impact of AI on your operations and envision a fully interconnected plant.
While the melting process does not provide perfect mixing, this study shows that mixing is indeed initiated during melting.
Rising costs of resins and additives, along with higher demands for quality and use of regrind, place a premium on proficient blending. Here are some steps to get you there.
While prices moved up for three of the five commodity resins, there was potential for a flat trajectory for the rest of the third quarter.
The Plastics Industry Association (PLASTICS) has released final figures for NPE2024: The Plastics Show (May 6-10; Orlando) that officially make it the largest ever NPE in several key metrics.
Mike Sepe has authored more than 25 ANTEC papers and more than 250 articles illustrating the importance of this interdisciplanary approach. In this collection, we present some of his best work during the years he has been contributing for Plastics Technology Magazine.
Second quarter started with price hikes in PE and the four volume engineering resins, but relatively stable pricing was largely expected by the quarter’s end.
Take a deep dive into all of the various aspects of part quoting to ensure you’ve got all the bases—as in costs—covered before preparing your customer’s quote for services.
The tape-stacking cell was developed by Engel. In order to achieve the shortest possible cycle times here too, it relies on the pick-and-place principle. This means that tapes can be deposited and spot-welded together at three-second intervals. Since the quality of the stack depends on the accuracy of the tape positioning, Engel has equipped the stacking cell with a measuring system comprising high-resolution camera technology. The measuring system delivers data that is used for actively intervening in the depositing process, thus guaranteeing the greatest possible depositing accuracy.
Two systems are used for the production of the blanks. A pick-and-place tape stacking cell with optical image processing and a consolidation press, which Engel will be presenting for the first time at Composites Europe. "With this new development, we have succeeded in consolidating stacks of fiber-reinforced thermoplastic tapes in the injection moulding cycle," says Dr. Norbert Müller, head of Engel’s center for lightweight composite technologies. "The consolidation press can be seamlessly integrated into the overall process, which significantly increases efficiency in the production of tailor-made tape solutions."
Baystar's Borstar technology is helping customers deliver better, more reliable production methods to greenhouse agriculture.
Across all process types, sustainability was a big theme at NPE2024. But there was plenty to see in automation and artificial intelligence as well.
This reproducible thermoplastic approach enables integration of the forming process and functionalization, and to merge the supporting structure and functional elements in an adhesive manner. "The fully automated one-shot process contributes considerably to the low unit costs required by the automotive industry," emphasizes Christian Wolfsberger, Business Development Manager Composite Technologies at Engel's headquarters in Schwertberg, Austria. A further benefit: the exclusive use of thermoplastic polymers simplifies the development of recycling strategies with the aim of returning the components to the material cycles at the end of their service life. "We can see that thermoplastic-based composite lightweight design is increasingly becoming the focus of product developers, both in the automotive and aircraft industries," stresses Wolfsberger.
The fully automated, large-scale production system solution supplied by injection machine builder Engel consists of a duo 1700 injection moulding machine with 17,000 kN clamping force, three easix articulated robots for the preparation of multiple metal inserts as well as for the handling of the organic sheet, a viper 90 linear take-out robot and a size 5 IR oven. Engel provides this cell as a system solution all from a single source.
Learn about sustainable scrap reprocessing—this resource offers a deep dive into everything from granulator types and options, to service tips, videos and technical articles.
Core Technology Molding turned to Mold-Masters E-Multi auxiliary injection unit to help it win a job and dramatically change its process.
The question of resin compatibility is not well publicized and rarely comes up out on the shop floor. So, any time you purge to change resins, you need to ask the question: Are these resins compatible or do they react like PVC and acetal?
When, how, what and why to automate — leading robotics suppliers and forward-thinking moldmakers will share their insights on automating manufacturing at collocated event.
August 29-30 in Minneapolis all things injection molding and moldmaking will be happening at the Hyatt Regency — check out who’s speaking on what topics today.
If the same machine barrel and screw must process both these resins, disassemble and clean them properly before resuming processing. Even small residues can be hazardous.
Formnext Chicago is an industrial additive manufacturing expo taking place April 8-10, 2025 at McCormick Place in Chicago, Illinois. Formnext Chicago is the second in a series of Formnext events in the U.S. being produced by Mesago Messe Frankfurt, AMT – The Association For Manufacturing Technology, and Gardner Business Media (our publisher).
In a time where sustainability is no longer just a buzzword, the food and beverage packaging industry is required to be at the forefront of this innovation. By adopting circular packaging processes and solutions, producers can meet regulatory requirements while also satisfying consumer demand and enhancing brand reputation. Join Husky to learn more about the broader implications of the circular economy — as well as how leading brands are leveraging this opportunity to reduce costs, increase design flexibility and boost product differentiation. Agenda: The cost and operational benefits of embracing circularity Key materials in circular packaging — including rPET and emerging bioplastics How to design a circular food and beverage package Strategies for selecting sustainable closures to future-proof packaging solutions Optimization and streamlining of production processes for enhanced efficiency How Husky Technologies can enable your sustainable success
Say “manufacturing automation” and thoughts immediately go to the shop floor and specialized production equipment, robotics and material handling systems. But there is another realm of possible automation — the front office.
GETTING A QUOTE WITH LK-MOULD IS FREE AND SIMPLE.
FIND MORE OF OUR SERVICES:
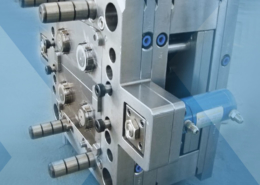
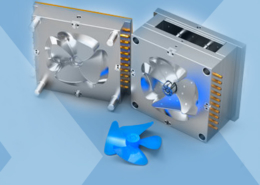
Plastic Molding

Rapid Prototyping
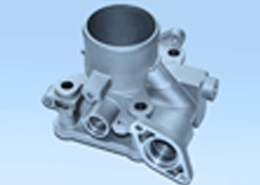
Pressure Die Casting
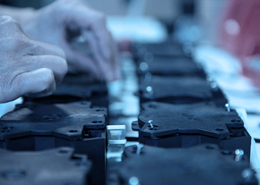
Parts Assembly
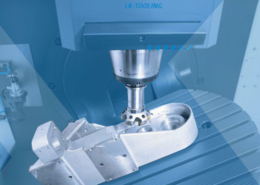