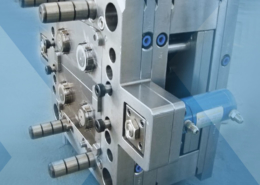
Functional Injection Molds (and More) from 3D Printed Metal Paste - 3d printed s
Author:gly Date: 2024-09-30
The transformation of the Columbus-East facility will occur over a four-year period, and the company plans to continue manufacturing its current pre-fillable glass syringe production lines while the facility undergoes its transformation.
KraussMaffei has set up a rather remarkable example of closed-loop circularity at booth 600 in the west hall at NPE2024.
The investment will add 69,000 sq. ft. to the facility and transform it into one of the largest and most sophisticated plastic molding plants in the world, said BD in a news release. A majority of the molding work currently undertaken by third-party manufacturers in North America will be transferred in house by BD, which reportedly is one of the largest users of molded plastic products in the world. The company said that more than 700 billion units are manufactured each year for use in its medical devices.
Editor in chief of PlasticsToday since 2015, Norbert Sparrow has more than 30 years of editorial experience in business-to-business media. He studied journalism at the Centre Universitaire d'Etudes du Journalisme in Strasbourg, France, where he earned a master's degree.
Blood-collection vials made from medical-grade polypropylene are injection molded on the show floor, transported via a series of what look like pneumatic tubes to a shredder, upcycled via a twin-screw extruder, processed with various additives, and injection molded anew to produce the bottle opener pictured here. The process is apparently seamless.
Late last month, BD also announced that it will acquire C.R. Bard Inc., a medical technology company specialized in the fields of vascular, urology, oncology and surgical products for $24 billion. The combination will create a highly differentiated medical technology company uniquely positioned to improve both the process of care and the treatment of disease for patients and healthcare providers, said the company in a news release published on April 23.
The vials are first molded using ExxonMobil PP 9074 MED on an all-electric PX 251-1400 injection molder. Thirty-two vials are produced per shot. For the purposes of this demonstration, the vials are transported to a grinder via the tubes and transformed into pellets in a matter of minutes.
BD plans to invest $7 million to retain and retrain its associates for the different skill sets needed for plastic molding manufacturing or to facilitate their transfer to its other manufacturing facility in Columbus or other sites across the BD network. BD is working with local and state officials to develop the necessary training programs and curriculum to be administered in educational institutions in the Columbus area.
In September, BD announced a $100 million investment in its Holdrege, NE, facility to expand capacity for its insulin syringe manufacturing operations, bringing BD’s total commitment to Nebraska to $160 million in the past eight months alone. In addition to Columbus and Holdrege, BD also has operations in Broken Bow, NE, and employs approximately 2,500 people across the state.
They are then processed with a ZE 28 BluePower twin-screw extruder and, following the mixing and blending of adhesive and liquid color additives, the compound is sent to an all-electric PX 81-180 press, where the bottle opener is molded. The PX 81-180 is equipped with APCplus, which compensates for process fluctuations that may result from recyclates with different viscosities.
“Columbus is home to BD’s largest and longest-running manufacturing facility in the world, and we are excited to bring cutting-edge technology and production to the area,” said Steve Sichak, Executive Vice President and Chief Integrated Supply Chain Officer. “Columbus will be the centerpiece for our plastic molding manufacturing strategy for North America, supporting multiple business units in the U.S. and around the world.”
Medical technology company BD (Becton, Dickinson and Company; Franklin Lakes, NJ) has announced it will invest $60 million to turn its facility in Columbus, NE, into a plastic injection molding manufacturing center of excellence by 2021.
This allows components to be produced with consistently high quality and little waste, another important contribution to greater sustainability, said KraussMaffei.
The company will add 69,000 sq. ft. to its Columbus, NE, facility, which it intends to transform into a plastic injection molding manufacturing center of excellence by 2021.
A system of this type in a real-world application might be a bit of a stretch, but it is quite stunning to witness the metamorphosis of a plastic vial into a bottle opener in such an all-encompassing manner.
Watch the circular economy in action at booth W600 at NPE, running through May 10 at the Orange County Convention Center in Orlando, FL.
GETTING A QUOTE WITH LK-MOULD IS FREE AND SIMPLE.
FIND MORE OF OUR SERVICES:
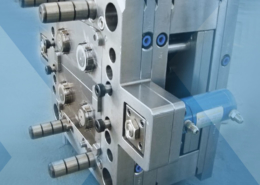
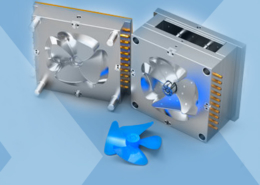
Plastic Molding

Rapid Prototyping
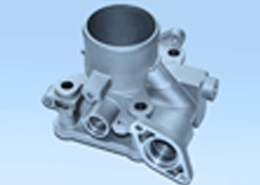
Pressure Die Casting
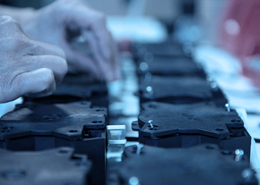
Parts Assembly
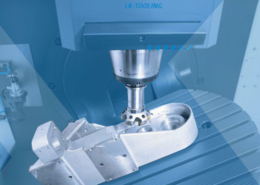