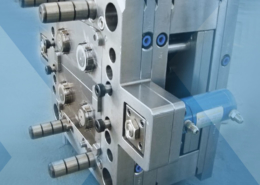
Functionalization in the Injection Molding of Thermosets - thermoset plastic mol
Author:gly Date: 2024-09-30
A longtime supplier of cyclic olefin copolymers under the Topas brand to the medical technology sector, the Polyplastics Group has added Duracon polyoxymethylene/acetalis (POM) to its medical-grade polymers portfolio. The Duracon POM PM series is now commercially available globally for medical applications.
Both grades meet medical device manufacturers’ key requirements and are targeted for a range of applications including drug contact and delivery. The materials are in compliance with ISO 10993 and USP Class VI for biocompatibility and cytotoxicity, have been submitted to FDA’s Drug Master File (DMF) and Device Master File (MAF), and comply with EU 10/2011 and FDA food contact 21 CFR 177.2470. The materials withstand hot steam and ethylene oxide (EtO) sterilization.
Polyplastics’ two acetal grades include standard viscosity PM09S01N, which delivers the reliable mechanical properties and moldability expected from POM, and PM27S01N, a high-flow grade that enables wall-thinning, miniaturization, and lightweighting of medical devices.
The PM series adheres to strict quality management systems including conformity to the VDI 2017 medical-grade polymers standard. Full traceability of processes and products, and production management based on GMP principles are ensured.
"Rodon’s cleanroom is the latest investment in reshoring manufacturing in the critical healthcare supply chain,” explains Michael Araten, company president. "Rodon has been committed to American manufacturing for almost 70 years, and our team is excited to couple our ISO 13485 certification with our cleanroom to bring advanced precision manufacturing solutions to our customers.”
The modular cleanroom utilizes an HVAC system with a HEPA filter, enabling Rodon to modify the room’s particulate level and class based on a project’s requirements. Clients can choose the cleanroom class that meets their needs and budget, ranging from Class 8 to a white space. Allowing for flexible equipment arrangement, Rodon can also scale operations up or down, fitting six to 15 injection molding presses in the room or incorporating additional work cells.
Building, certifying, and maintaining a controlled cleanroom environment in a manufacturing facility can be quite costly. To help clients capitalize on cleanroom manufacturing without investing that time and expense or having to send work overseas, The Rodon Group has built an ISO Class 8-capable cleanroom for its injection molding operations.
The company uses FDA-grade materials and operates over 115 presses and robotic systems in its Hatfield, Pennsylvania, facility. In addition to cleanroom manufacturing, Rodon’s services range from toolmaking and mold design to high-volume custom injection molding.
This article is sponsored by The Rodon Group, a company specializing in custom plastic injection molding and precision manufacturing solutions since 1956.
"Now more than ever, it’s imperative that we bring manufacturing back to the U.S.,” says Dave Steen, Rodon’s QC manager. "With Rodon’s state-of-the-art Class 8 cleanroom — now a Class B modular cleanroom — we can help do just that, not only for medical device, pharmaceutical, and food and beverage companies but anyone who needs a clean-environment part for secondary operations.”
GETTING A QUOTE WITH LK-MOULD IS FREE AND SIMPLE.
FIND MORE OF OUR SERVICES:
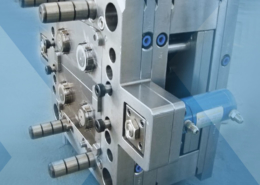
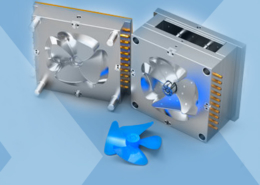
Plastic Molding

Rapid Prototyping
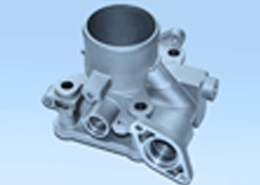
Pressure Die Casting
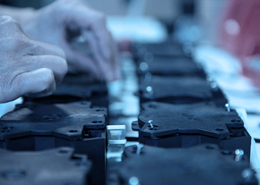
Parts Assembly
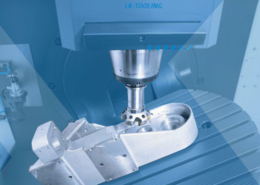