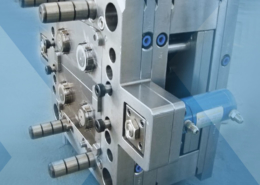
Exploring the Versatility of PCS Injection Molding
Author:gly Date: 2024-06-08
Introduction
PCS injection molding stands at the forefront of advanced manufacturing techniques, offering unparalleled versatility and precision in the production of plastic components. This article delves into the intricacies of PCS injection molding, unraveling its processes, applications, and significance in modern industry.
Understanding PCS Injection Molding
PCS (Polycarbonate/Siloxane Copolymer) injection molding is a specialized molding process that utilizes a unique blend of polycarbonate and siloxane copolymer resins. This innovative material combination imbues the final product with exceptional mechanical properties, including high impact strength, heat resistance, and chemical durability.
Process and Techniques
The PCS injection molding process involves melting the polycarbonate/siloxane copolymer blend and injecting it into a mold cavity under high pressure. Advanced techniques such as gas-assisted injection molding and multi-component molding enable the production of complex geometries and integrated features with precise control over material distribution and part properties.
Advantages and Benefits
PCS injection molding offers a myriad of advantages over conventional molding processes. The inherent properties of polycarbonate and siloxane copolymers, combined with the versatility of injection molding, result in parts with superior impact resistance, thermal stability, and dimensional accuracy. Additionally, the ability to incorporate multiple materials in a single process streamlines production and reduces assembly costs.
Applications Across Industries
The versatility of PCS injection molding finds applications across a diverse range of industries, including automotive, electronics, medical devices, and consumer goods. From automotive components and electronic enclosures to medical implants and household appliances, PCS injection molding enables the production of high-performance parts with precise tolerances and exceptional surface finish.
Technological Advancements
Technological advancements in PCS injection molding have led to continuous improvements in process efficiency, part quality, and material performance. Innovations such as in-mold sensing and real-time process monitoring enable tighter process control and quality assurance, resulting in enhanced productivity and reduced scrap rates.
Challenges and Solutions
Despite its numerous benefits, PCS injection molding presents challenges such as material handling, mold design complexity, and processing parameters optimization. However, collaborative research efforts between material scientists, mold designers, and process engineers have led to the development of novel solutions and techniques to overcome these challenges, further advancing the capabilities of PCS injection molding.
Future Perspectives
Looking ahead, the future of PCS injection molding holds immense promise. Continued research and development efforts aimed at enhancing material properties, process efficiency, and sustainability will drive further innovation in this field. Additionally, the integration of digital technologies such as artificial intelligence and machine learning may revolutionize the design and optimization of PCS injection molding processes, paving the way for new applications and advancements.
Conclusion
In conclusion, PCS injection molding stands as a testament to the convergence of material science, manufacturing technology, and engineering innovation. With its unique blend of polycarbonate and siloxane copolymer resins, coupled with the precision and versatility of injection molding, PCS injection molding offers unmatched capabilities and possibilities for product design and development. As the industry continues to evolve, PCS injection molding remains poised to play a pivotal role in shaping the future of manufacturing across diverse industries.
GETTING A QUOTE WITH LK-MOULD IS FREE AND SIMPLE.
FIND MORE OF OUR SERVICES:
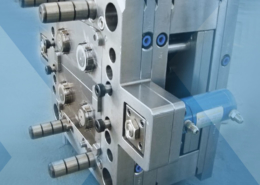
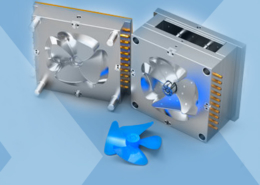
Plastic Molding

Rapid Prototyping
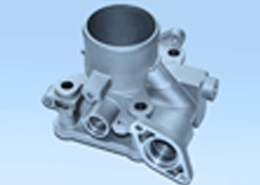
Pressure Die Casting
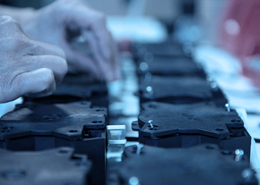
Parts Assembly
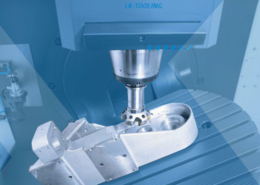