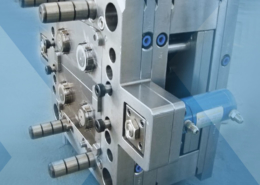
Exploring Peek Molding: Revolutionizing Plastic Manufacturing
Author:gly Date: 2024-06-08
Peek molding stands at the forefront of modern plastic manufacturing techniques, captivating engineers and designers alike with its versatility and efficiency. Originating from the acronym for Polyether Ether Ketone, PEEK is a high-performance thermoplastic polymer known for its exceptional mechanical properties and chemical resistance. In the realm of molding, PEEK has emerged as a game-changer, offering unparalleled precision and durability in the production of intricate parts and components. This article delves into the intricacies of Peek molding, exploring its applications, advantages, challenges, and future prospects.
Advantages of Peek Molding
High Precision and Complex Geometry
Peek molding enables the creation of parts with intricate geometries and tight tolerances, a feat that traditional molding techniques struggle to achieve. The material's excellent flow characteristics, coupled with advanced molding technologies such as injection molding, allow for the production of highly complex components with consistent quality.
Superior Mechanical Properties
One of the key attractions of Peek molding is the exceptional mechanical properties imparted by the material. PEEK exhibits high tensile strength, stiffness, and creep resistance, making it ideal for applications subjected to harsh operating conditions, including aerospace, automotive, and medical devices. Moreover, Peek's resistance to wear and abrasion ensures longevity and reliability in demanding environments.
Chemical Resistance and Stability
Peek possesses remarkable chemical resistance, rendering it unaffected by a wide range of chemicals, solvents, and hydrocarbons. This property makes Peek molding suitable for applications where exposure to aggressive substances is common, such as chemical processing, oil and gas, and semiconductor manufacturing. Additionally, Peek's inherent stability at high temperatures ensures dimensional stability and performance consistency over time.
Challenges and Considerations
High Cost
One of the primary challenges associated with Peek molding is its relatively high cost compared to conventional plastics. The raw material cost of PEEK is substantially higher, primarily due to its exceptional properties and limited availability. Additionally, Peek's processing requirements, including elevated temperatures and specialized equipment, contribute to higher manufacturing expenses.
Processing Challenges
Peek's high melting point and thermal stability pose challenges during processing, necessitating robust equipment and precise control parameters. Achieving optimal melt flow and minimizing thermal degradation require sophisticated molding techniques and extensive process optimization. Furthermore, Peek's tendency to absorb moisture can affect dimensional accuracy and surface finish if not properly managed during molding.
Tooling and Mold Design
Designing molds for Peek molding requires careful consideration of material properties, part geometry, and manufacturing constraints. The high temperatures and pressures involved demand durable tooling materials capable of withstanding prolonged exposure to aggressive conditions. Moreover, mold design optimization is crucial to ensure uniform filling, minimal defects, and efficient cooling for optimal part quality and cycle times.
Future Perspectives and Innovations
Peek molding continues to evolve with ongoing advancements in material science, processing technologies, and design methodologies. Research efforts are focused on enhancing Peek's processability, expanding its application range, and reducing production costs through innovative approaches such as additive manufacturing and hybrid molding processes. Furthermore, the integration of computational modeling and simulation techniques enables virtual prototyping and optimization, facilitating faster development cycles and improved part performance.
Conclusion
In conclusion, Peek molding represents a paradigm shift in plastic manufacturing, offering unparalleled precision, performance, and versatility. Despite facing challenges such as high costs and processing complexities, the benefits of Peek molding outweigh the drawbacks, making it a preferred choice for demanding applications across various industries. As research and innovation continue to drive advancements in material science and processing technologies, Peek molding is poised to play an increasingly pivotal role in shaping the future of manufacturing.
Through this exploration, we have gained insights into the transformative potential of Peek molding and its implications for the industry. As we look ahead, continued collaboration between researchers, engineers, and manufacturers will be essential to unlock new possibilities and address existing challenges. By harnessing the power of Peek molding and embracing innovation, we can propel the evolution of plastic manufacturing towards greater efficiency, sustainability, and excellence.
GETTING A QUOTE WITH LK-MOULD IS FREE AND SIMPLE.
FIND MORE OF OUR SERVICES:
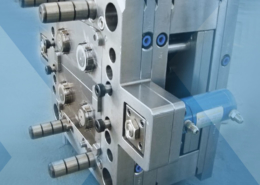
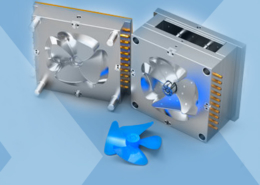
Plastic Molding

Rapid Prototyping
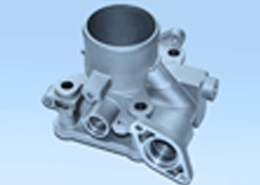
Pressure Die Casting
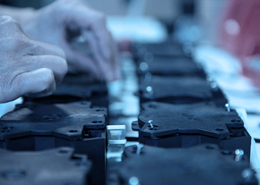
Parts Assembly
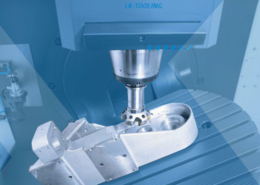