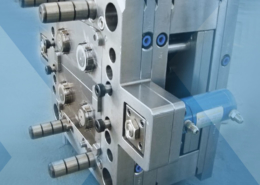
Exploring PBT Injection Molding: Unleashing the Potential of Engineering Plastic
Author:gly Date: 2024-06-08
PBT injection molding stands as a hallmark of modern engineering plastics manufacturing, captivating industry professionals with its versatility, durability, and dimensional stability. PBT, or Polybutylene Terephthalate, is a high-performance thermoplastic polymer renowned for its excellent mechanical properties, chemical resistance, and electrical insulation. In the realm of injection molding, PBT has emerged as a preferred material for producing intricate parts and components across various industries. This article delves into the intricacies of PBT injection molding, exploring its applications, advantages, challenges, and future prospects.
Introduction to PBT Injection Molding
PBT injection molding involves the process of injecting molten PBT resin into a mold cavity at high pressure, where it solidifies to form the desired shape. This method offers numerous advantages, including high precision, repeatability, and efficiency, making it suitable for mass production of complex parts with tight tolerances. With its exceptional mechanical properties, chemical resistance, and dimensional stability, PBT injection molding finds applications in automotive, electrical and electronics, consumer goods, and beyond.
Advantages of PBT Injection Molding
Excellent Mechanical Properties
PBT exhibits superior mechanical properties, including high tensile strength, stiffness, and impact resistance, making it suitable for demanding applications where strength and durability are paramount. The inherent toughness of PBT allows for the production of robust components capable of withstanding mechanical stress, vibration, and impact, ensuring long-term reliability and performance.
Chemical Resistance and Stability
One of the key attractions of PBT is its exceptional chemical resistance and dimensional stability over a wide range of temperatures and environmental conditions. PBT resists degradation when exposed to oils, fuels, solvents, and harsh chemicals, making it ideal for applications in automotive under-the-hood components, electrical connectors, and industrial equipment where exposure to aggressive substances is common.
Electrical Insulation Properties
PBT possesses excellent electrical insulation properties, making it a preferred material for manufacturing electrical and electronic components such as connectors, switches, and insulating enclosures. Its high dielectric strength, low moisture absorption, and thermal stability ensure reliable performance in demanding environments, reducing the risk of electrical failures and malfunctions.
Challenges and Considerations
Processing Challenges
PBT injection molding presents challenges related to material handling, mold design, and processing conditions. PBT's relatively high melt viscosity and tendency to crystallize quickly require precise control of injection parameters, mold temperature, and cooling rates to avoid defects such as warpage, sink marks, and voids. Moreover, PBT's hygroscopic nature necessitates proper drying to minimize moisture content and ensure consistent part quality.
Tooling and Mold Design
Designing molds for PBT injection molding requires careful consideration of material shrinkage, flow characteristics, and part geometry to achieve optimal performance and dimensional accuracy. The selection of mold materials, surface finishes, and gating designs influences cycle times, part quality, and production costs, highlighting the importance of collaboration between mold designers, toolmakers, and injection molders.
Future Perspectives and Innovations
The future of PBT injection molding holds promising opportunities for innovation and advancement in materials, processes, and applications. Research efforts are focused on enhancing PBT's processability, incorporating sustainable additives, and developing novel composites to expand its application range and improve performance. Furthermore, advancements in digital design, simulation, and additive manufacturing technologies enable faster prototyping, optimization, and customization of PBT components, driving efficiency and innovation in product development and manufacturing.
Conclusion
In conclusion, PBT injection molding represents a cornerstone of modern engineering plastics manufacturing, offering unparalleled versatility, durability, and performance for a wide range of applications. Despite facing challenges such as processing complexities and tooling considerations, the benefits of PBT injection molding outweigh the drawbacks, making it a preferred choice for industries seeking high-quality, reliable, and cost-effective solutions. As we look to the future, continued investment in research, development, and collaboration will drive innovation and propel the evolution of PBT injection molding towards greater efficiency, sustainability, and excellence.
Through this exploration, we have gained insights into the transformative potential of PBT injection molding and its significance in advancing manufacturing technologies and applications. By embracing innovation and collaboration, we can unlock new opportunities and address existing challenges, ensuring that PBT injection molding remains at the forefront of materials science and engineering excellence in the years to come.
GETTING A QUOTE WITH LK-MOULD IS FREE AND SIMPLE.
FIND MORE OF OUR SERVICES:
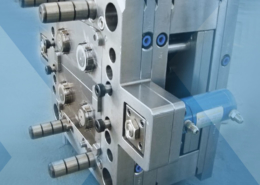
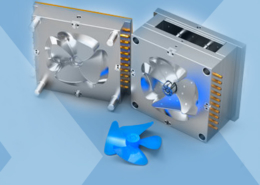
Plastic Molding

Rapid Prototyping
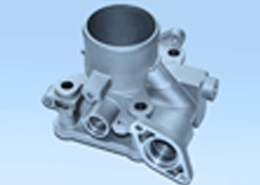
Pressure Die Casting
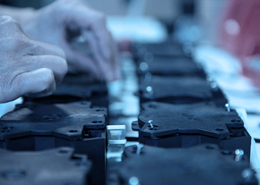
Parts Assembly
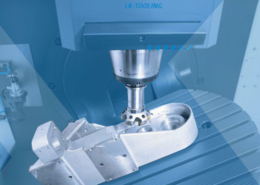