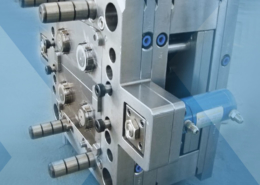
Are all-electric machines more eco-friendly than hydraulic options? - injection
Author:gly Date: 2024-09-30
There are also opportunities for the MIM industry in the growth of metal Additive Manufacturing, in particular Binder Jetting technology. The source of everything is powder and binder, and for each of these technologies is only a matter of combining these materials. We have to understand these powders and feedstocks in a scientific way to achieve the best results in any of these processes. Striving forward with countless materials, mathematics is our only stalwart – including, of course, our diligence and tireless efforts.
MIM’s fruitful results in Greater China are due to the concerted efforts of the global MIM industry and the large number of orders from customers. At this time, even if the MIM industry is affected by uncertainties in the post-smartphone era, the outlook is bright. We sincerely welcome friends from all over the world to come and see the changes in MIM which have taken place in Greater China over the past thirty years, which has seen us using more advanced equipment and more cost-effective metal powder, making more precise MIM parts, and changing human civilisation.
Don't miss any new issue of PIM International, and stay up to date with the latest industry news. Sign up to our fortnightly newsletter.
The manufacturing of golf club heads is of growing interest, and the MIM process can be better utilised than traditional manufacturing processes to provide enhanced surface effects and detailed features. This has reached the point where the United States Golf Association (USGA) now considers the MIM process to be a standard golf head manufacturing process.
Taiwan’s HTC, which was acquired by Google in 2017, began to use MIM to produce the main body of the SIM card tray, which indirectly began a trend amongst domestic smartphone brands, starting with Huawei, before extending to OPPO, Vivo, and Xiaomi. MIM components in smartphones now included camera lens protection rings and covers, side buttons for volume and power, the connector interface of I/O port, and so on (Fig. 2). From 2018, domestic Chinese smartphones producers also started to use micro gear reducers featuring many MIM parts for motorised ‘telescopic’ camera modules. MIM parts gradually reached their peak usage in smartphones.
He has a fair point. It doesn’t make sense to run a simple problem in more complicated simulation programs. Setting up the program, exporting the files and fixing the geometry can take hours before you even run the simulation. In SolidWorks it will take no more than 5 minutes. Additionally, subsequent simulation set up is as simple as altering the CAD model.
Based on customer demand, the use of magnetic functional materials produced via MIM has greatly increased. This has included the application of soft magnetic materials and magnetic permeable materials, the introduction of cobalt elements (e.g., Fe-50Co and F75) into the MIM process. There are a large number of applications in the magnetic guidance, electromagnetic interference shielding of electronic products.
In addition, the promotion of titanium and titanium alloys in the past three years has also achieved positive results in domestic production, spurring on the creation of titanium and titanium alloy feedstocks and accelerating the MIM process for these materials.
The ability to change from W-Ni-Cu heavy alloy, which is difficult to control during sintering, to W-Ni-Fe has also been advantageous. With production in graphite vacuum sintering furnaces operating at 1480-1500°C, the risks of using hydrogen atmospheres in sintering is eliminated and the efficiency and safety of production greatly increased.
A deeper exploration of what MIM can offer to customers has begun, with success for hinges of 3C devices (Fig. 3), sewing machine components, fasteners and tags for luxury bags and goods, kitchen knives, nail clippers, jigs and tools, and golf club heads. MIM has even begun to be put into some internal components of electric vehicles – for example in transmissions and the lithium battery pack, thus changing the nature of MIM components from something with a low cost and necessarily short lifespan, such as fashion, where the lifecycle of a garment isn’t equal to the lifecycle of its parts, to something intended to last as long as possible.
However, this package can be extended with additional analysis types available in SolidWorks Simulation Professional and SolidWorks Simulation Premium, like fatigue, frequency, nonlinear and dynamic analysis.
At the beginning of the third stage, MIM part producers in Greater China were already feeling the winds of change. Those MIM makers that originally supplied domestic smartphone producers saw demand plummet to the point that some companies had no orders to fulfil; they needed to change direction to survive. As a result, the following developments have emerged.
Additionally, tools like linked multiphysics can certainly ensure that the final designs are completely optimized for final users. However, setting up such an analysis can take time and skills of a full simulation analyst.
Discover suppliers of these and more in our advertisers’ index and buyer’s guide, available in the back of PIM International.
“There is a productivity boost,” said Whyte. “If you are doing an analysis that fits in the assumptions made by the linear static stress analysis, which is 80% of the analysis done out there today, tools like the analysis capabilities we have in SolidWorks Premium are the most productive way to get a result, and our Simulation Professional and Simulation Premium packages can then take you a little further.”
In March 2007, the very first issue of PIM International featured a review of Metal Injection Molding in Asia. China’s MIM industry was estimated...»
Simulation at the start of the design process, however, means that you are able to test every decision along the development cycle. Design engineers are no longer over engineering a piece to ensure it passes the analyst’s muster. Instead through quick guess and check, they are optimizing the material, manufacturing process, cost, and even environmental impact by performing simple simulations.
No one is going to tell you that SolidWorks Simulation is a simulation powerhouse; it isn’t trying to be. The key to the software’s success isn’t eye popping feats like multiphysics, high cell counts, adjunct solvers, or fancy meshing tools seen in COMSOL, STAR-CCM+, ANSYS, and Simulia. SolidWorks Simulation instead brings the power of simulation into a CAD environment and therefore the initial design stages. This offers simple, cheap, quick methods for designers and design engineers to make more informed early decisions producing an overall more optimized product. After all, sometimes it’s David that really beats Goliath.
The ability to produce these high-strength precision gears by MIM to the American Gear Manufacturers Association’s (AGMA) Q9 class accuracy is significant. Tempering after H900 heat treatment with 17-4PH significantly increases the wear resistance of the gear, allowing MIM to replace traditional PM gears and brass cut gears. As shown in Fig. 5, the technology of insert moulding plastics with MIM has also been adopted. Overall, technological improvements have enabled MIM to expand its offerings in a wider range of directions, a key to the success of MIM companies, as noted above.
Type 420 martensitic stainless steel covers a wide carbon range of 0.15% to 0.45%. Demand for this material from the 3C, automotive, biomedical and...»
In terms of known data, the combined revenue from MIM part sales in Greater China (Mainland China and Taiwan) surpassed North America, Europe, and Japan in 2011. By 2020, it past US $1.5 billion (CNY ¥10 billion) and the number of MIM factories had increased from fewer than fifty to over 200. China had become the country with the largest number of MIM applications in the world, as well as supporting a thriving industry for MIM processing equipment such as feedstock pelletisers, injection moulding machines and catalytic debinding and sintering furnaces.
“Our developers have made a conscious decision to utilize easy to mesh element types and algorithms. We have five different mesh elements we can use but most solid body analysis is done with tetrahedrons. They get good results in most situations and they are very easy to write meshing algorithms for … We also retain control with adaptive meshing techniques where the mesh will change dependent on the stress gradients,” said Whyte.
The weight of MIM parts ranges from less than 10 g to more than 500 g, and MIM parts are now gradually replacing parts made by investment casting and die casting. There are two favourable factors influencing this. Firstly, China’s environmental policy now strictly controls polluting wax-based casting and forging factories, which restricts the development of these industries. Secondly, China’s metal powder production industry has invested in increasing capacity. Because China’s general stainless steel production usage is high, the wide availability of stainless steel scrap for recycling and atomisation has reduced powder prices. In this way, it has become more economical to produce larger parts with MIM. As an example, the average price of MIM 304 stainless steel powder is slightly less than US $6/Kg (<40 RMB/Kg), which is close to the typical price of the same powder for conventional press and sinter PM. As time goes on, MIM 201 powder is expected to cost less than US $4.5/ kg (< 30 RMB/kg), again allowing it to directly replace the traditional low-cost stainless steel powder used in PM.
Whyte said that SolidWorks Simulation “goes into some fair depth like non-linear dynamic analysis and it has a very capable CFD tool. We can draw different stratification for CFD and see how things will stack up differently. But when you go into highly non-linear, multiphysics, and highly dynamic problems we get close to the limit of our solver’s abilities. This is when you pick up ABAQUS, LS-Dyna, or Marc”
Reach a truly international audience that includes component manufacturers, end-users, industry suppliers, analysts, researchers and more.
At this point, Apple began to use the MIM cobalt-chrome-molybdenum alloy, F75, to make the rear camera frames of smartphones and tablets. Unfortunately, this was also when domestic smartphone producers began to eliminate the MIM process, citing cost considerations. What compounded the situation was that the top ten MIM suppliers were contracted with Apple with very strict specifications on production equipment, quality and specifications, so many MIM producers could not compete for business. Non-Apple smartphones switched from MIM to sheet metal and plastic products. However, the arrival of COVID-19 increased the demand for laptops and, in combination with the emergence of folding smartphones with their complex MIM hinges, a deeper slump in sales was prevented.
The expansion of MIM materials expands the application range of products, from traditional materials as iron-nickel alloys (Fe-2, 4, 8Ni to 50Ni), 304/316, 304L/316L, 420J2/440C stainless steels, W- Ni-Cu, expanded to 201, 430, 17-4PH and PANACEA® stainless steels, Fe-50Co (HiperCo®), Fe-3Si, W-Ni-Fe, etc.
“There are three other simulation technologies,” explains Whyte. “Flow Simulation is a CFD tool used for fluid flow and heat transfer. It has some extensions for electronics, and the HVAC industry. We also have a simple first pass life cycle assessment tool to determine the environmental impact of the materials and manufacturing choices. Finally, we have a plastic injection molding tool to detect potential injection molding defects … Generally we don’t like to bundle things. Typically you want to be able to buy what you want.”
The free-to-access PIM International magazine archive offers unparalleled insight into the world of MIM, CIM and sinter-based AM from a commercial and technological perspective through:
Apple began to use MIM parts in its smartphones. This is the era when the MIM industry began to take off in China, with the demands of Apple being met by MIM factories such as TPT Technology, the former parent company of Suzhou CPT Technology, and Shanghai Future High-Tech. At that time, the main components were the SIM card tray ejector mechanisms and various internal parts of the phones. With the investment of Taiwan’s SZS, the hinges on Apple’s laptops also gradually switched to MIM.
Fig. 1 shows total annual MIM sales in Greater China as well as a breakdown of the total sales of 3C (Computer, Communication and Consumer Electronics) MIM parts used in smartphones, tablets, laptop PCs, desktops PCs and servers, and smart wearable devices. The three bold numbers in Fig. 1 identify the start of three distinct stages of MIM’s usage in smartphones.
Eliminating these tools may hurt the ability to completely optimize the problem but they are necessary to ensure designers and design engineers can use simulation properly. Besides, these “frills” fulfill a task much farther down the development cycle than initial design. At the initial design stages performing separate quick and easy physics simulations can be useful to limit the final designs destined for analysts to a short list saving time and money.
“When analysis started hitting the mainstream in the 80’s, it was something done at the end of the process,” said SolidWorks Simulation expert Glenn Whyte, a Simulation Product Manager at Hawk Ridge Systems. “You build the plane at Boeing and just before your flight you run an analysis that was pass or fail. Pass you are good to go; fail you move right back to the start again.”
The technological improvement of MIM materials and equipment has allowed precision MIM components to replace CNC and other high-accuracy processes. As an example, Donggung Yujia Precision Technology Co., Ltd. (a branch of Hongkong Vigor Precision Co., Ltd., the world’s largest toy gearbox manufacturer) produces small module gears by MIM (diameter ~ 3-30 mm/m=0.1~1 mm), and has received interest from the leading international robotic vacuum cleaner manufacturer. In the future, heavy-duty ‘wet and dry’ cleaners and next-generation robots will feature MIM components.
MIM producers in Greater China anticipated a downward trend since the beginning of the COVID-19 pandemic. To combat this, many adopted the following strategy changes:
Again, SolidWorks Simulation isn’t the tool for complicated high level simulations. But that weakness has been turned into a strength. This barebones simulation tool will ensure that your designers and design engineers will pass on fewer partly optimized designs to analysts and simulation engineers.
For over 10 years, Shawn Wasserman has informed, inspired and engaged the engineering community through online content. As a senior writer at WTWH media, he produces branded content to help engineers streamline their operations via new tools, technologies and software. While a senior editor at Engineering.com, Shawn wrote stories about CAE, simulation, PLM, CAD, IoT, AI and more. During his time as the blog manager at Ansys, Shawn produced content featuring stories, tips, tricks and interesting use cases for CAE technologies. Shawn holds a master’s degree in Bioengineering from the University of Guelph and an undergraduate degree in Chemical Engineering from the University of Waterloo.
He wasn’t exaggerating. During a live demo two engineers in training, with little experience in SolidWorks Simulation, were able to run about a dozen simulations each in an optimization challenge. Having applied their knowledge of the CAD environment they were able to optimize the safety factor of a camera mount by limiting the mass of the mounting panel. Meanwhile, a chart kept track of results of each simulation run.
Tritone’s MoldJet is unique as an Additive Manufacturing process – not Binder Jetting, Material Extrusion, nor Material Jetting, the MoldJet pr...»
As seen in the chart below, perhaps the most confusing thing about the SolidWorks packages is the naming convention. Though Dassault Systemes’ top design tool SolidWorks Premium does include simulation, it is the basic version which only includes linear static simulations in assemblies and time based motion simulations.
However, after almost five years of observation, I found that at the start of the COVID-19 epidemic at the end of 2019, orders for MIM parts for smartphones manufactured in China declined significantly. Then, in early 2023, I learned that the rear camera frame of Apple’s iPhone 15 may have eliminated the use of MIM, which undoubtedly will be a major concern amongst China’s MIM producers. So, after the huge successes of the past decade, how should MIM companies progress into their post-smartphone era?
Extensive MIM, CIM industry and sinter-based AM industry news, plus the following exclusive deep-dive articles and reports:
“We look in the industry and see differences in expertise requirements from designers, to design engineers, to full time simulation engineers and pure analysts. We see SolidWorks as a design to engineering tool. One of the main advantages of it is that it is integrated into CAD during the design workflow. This will shorten the learning curve. We explain to our customers that have never done analysis before that they can analyze 4-5 different scenarios in an hour. Just by manipulating the CAD, processing the analysis, and keeping track of what those changes mean physically. Simulations are also completely integrated with the CAD model, if you make a design change then it is ready to analyze without intermediate steps like file exporting. It will also use the existing mesh settings to re-mesh the model,” said Whyte.
However, Whyte was quick to note that the other benefit is cost: “though only a sales team can give you a final quote, you can get SolidWorks Simulation at a fraction of the cost of other simulation tools.” This means companies can reduce the licenses of other costly heavy lifting simulation tools, which are far too advanced for designers anyway, and limiting those licenses to analysts and simulation engineers. This can ensure designers are able to perform simple simulations on a lower budget.
Potentially with a more universal appeal, at least four MIM factories in the southern Chinese city of Yangjing make kitchen knives from MIM 420/440 stainless steel and produce more than 10 million MIM nail clippers per year; these have become staple products both domestically and overseas (Fig. 4).
A technical session, comprising three papers, at the Euro PM2021 Virtual Congress, organised by the European Powder Metallurgy Association (EPMA) a...»
This year marks the year after MIM’s fiftieth anniversary. In 1972, the technology’s developer, Parmatech, could not have imagined the breadth of MIM’s future adoption, nor that manufacturers in the Greater China region would so fully embrace the process. We are very grateful to those pioneers for bringing this new technology to the world and we now strive to make the MIM process the norm in metal processing, along with casting, forging, machining, and press and sinter Powder Metallurgy.
GETTING A QUOTE WITH LK-MOULD IS FREE AND SIMPLE.
FIND MORE OF OUR SERVICES:
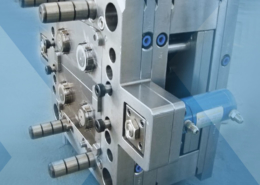
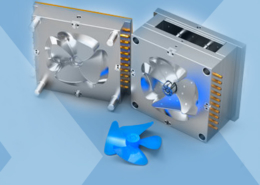
Plastic Molding

Rapid Prototyping
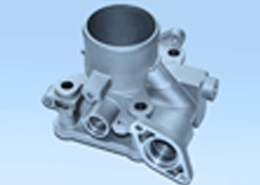
Pressure Die Casting
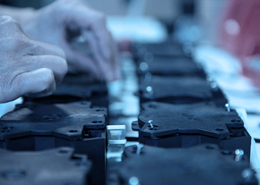
Parts Assembly
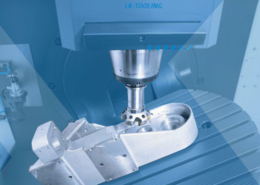