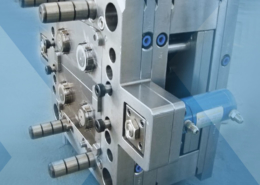
Are 3D printed molds ready for prime time? - low volume plastic injection moldin
Author:gly Date: 2024-09-30
“When you need to introduce a robot into that cycle, the robot needs to break into that molding process in order to go into the mold safely, extract the plastic parts, and then get out of there safely to allow the mold to shut again,” Buse explained. “That is what the Euromap 67 plug interface is doing. Users can control the sequence through the cobot’s teach pendant on the screen. The software is already embedded — all you have to do is turn it on when you install the line. When you get the inputs and outputs between both machines, you can start programming.”
"We set out to create the best lightweight performance gaming mouse," said Barrie Ooi, Head of Razer's PC Gaming Division. "We went beyond our usual design process to look at material selection and alternate industrial designs to create an ultra-durable magnesium alloy exoskeleton chassis in the fan-favorite Viper Mini shape. As a result, the Viper Mini Signature Edition is just 49 grams light with no compromises, making it our lightest mouse ever."
Integrating UR cobots with IMMs is as simple as installing the IMMI plug on the cobot’s controller and running a cable between the injection molder and the cobot, Buse explained. The Euromap 67 IO communication protocol means the IMMI runs on all brands of contemporary IMMs; some older machines can be retrofitted.
When connected, the UR cobot is integrated with the IMM’s safety features, including emergency stop circuits and safety doors. As the injection molding machine is running, it tells the cobot exactly what’s going on in real time so the cobot can perform its functions safely at just the right time.
UR’s Injection Molding Machine Interface (IMMI) has provided a new level of automation connectivity to the plastics industry since its introduction in 2020, said Christopher Buse, application engineer for UR. Because of the pandemic hiatus, NPE2024 was the first time the IMMI was shown at an NPE.
Razer unveiled a brand new gaming mouse for the hardcore gamer who wants to compete in fashion with the Viper Mini Signature Edition. Boasting that this is the lightest mouse the company has ever crafted (weighing in at just 49 grams), the design has been made to provide wireless performance filled with the company's best-in-class tech. It comes with an ultra-durable magnesium alloy exoskeleton chassis that matches the form factor of the standard Viper Mini, but sets it apart in design and specs in every way. We have more about the mouse below as it is currently up for sale for $280.
"The Viper Mini Signature Edition represents the most ambitious design and engineering project we've ever undertaken," said Charlie Bolton, Head of Industrial Design at Razer. "We wanted to push beyond the traditional honeycomb design, and this required a material with an outstanding strength-to-weight ratio. After evaluating plastics, carbon fiber, and even titanium, we ultimately chose magnesium alloy for its exceptional properties."
"Engineered for the gamers that dare to want it all, the Viper Mini Signature Edition is the pinnacle of gaming mouse performance. Weighing an astonishing 49 grams, gamers can experience true perfection with a master-grade gaming peripheral packed with our best-in-class technologies, all in one perfect form. The use of magnesium alloy and injection-molding techniques enabled significant weight reduction in the mouse without compromising on durability, while still allowing for a comfortable grip in the popular Viper Mini design. These choices enabled the Viper Mini Signature Edition to remain hyper-lightweight at just 49 grams while still delivering world-class performance. Crafted from high-grade magnesium alloy, the Viper Mini Signature Edition features an exceptional weight-to-strength ratio, owing to a new intricate, ultra-durable design created using an injection molding technique."
Geoff Giordano is a tech journalist with more than 30 years’ experience in all facets of publishing. He has reported extensively on the gamut of plastics manufacturing technologies and issues, including 3D printing materials and methods; injection, blow, micro and rotomolding; additives, colorants and nanomodifiers; blown and cast films; packaging; thermoforming; tooling; ancillary equipment; and the circular economy. Contact him at [email protected].
UR cobots are light enough to be wheeled from machine to machine, as required, Buse added, so users can “treat the cobot more as an operator.” And because UR cobots can be positioned flexibly simply by specifying an orientation through the control screen, users can bolt them to the platen of a press, on the side, or “in any orientation you can think of.”
Further, because the cobot can operate without protective shielding, molders don’t have to sacrifice precious manufacturing space.
"Each unit of the Viper Mini Signature Edition is created with an injection-molded exoskeleton that is then CNC machined, and polished. The exoskeleton shell then undergoes passivation to reduce any susceptibility to corrosion, after which it is painted and assembled. At each step, each unit is meticulously inspected to uphold only the highest quality. Boasting the Razer Focus Pro 30K Optical Sensor, Razer Optical Mouse Switches Gen-3, and HyperPolling Wireless with true 4000 Hz wireless polling rates, the Viper Mini Signature Edition features the fastest wireless gaming technology from Razer for higher speeds and stable performance. In addition, the Viper Mini Signature Edition can fully charge in under 90 minutes thanks to a 2C charging rate, which is four times the peak charging capacity of most other wireless mice. The Viper Mini Signature Edition comes with a pre-paired Razer HyperPolling Wireless Dongle, a set of Corning Gorilla Glass 3 Mouse Feet, a microfiber cleaning cloth, 2 Razer Mouse Grip Tape sets, and two alcohol prep pads."
Cobots offer injection molders unique benefits over traditional gantry robots, Buse continued. For instance, manufacturers with more compact production floors and low ceilings can’t always accommodate tall gantry robots.
Universal Robots (UR) is giving injection molders an easy-to-use interface that seamlessly connects its cobots to injection molding machines (IMMs) — a capability made possible thanks to the standardization of IMMs through the Euromap 67 standard.
And, a cobot allows for “cageless automation” — taking parts out of the dangerous, guarded production environment, then reaching outside that area into an unguarded area like a conveyor belt. Users can also program the cobot to perform secondary operations like degating from the runner or presenting parts to a laser marker.
While UR’s UR10 cobot is the most popular among injection molders, Buse said, the IMMI is compatible with all UR cobots, including the UR20 and new UR30. UR’s newest generation of cobots offer more extensive reach into bigger presses up to 750 tons at least. More commonly, machines of 400 tons or less are automated with UR cobots, Buse noted.
GETTING A QUOTE WITH LK-MOULD IS FREE AND SIMPLE.
FIND MORE OF OUR SERVICES:
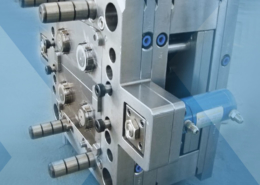
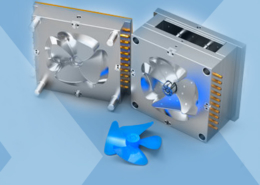
Plastic Molding

Rapid Prototyping
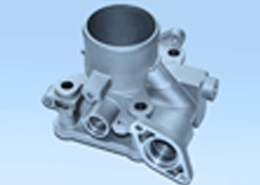
Pressure Die Casting
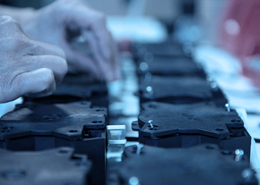
Parts Assembly
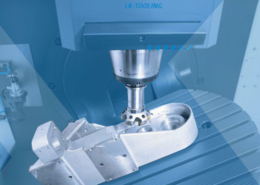