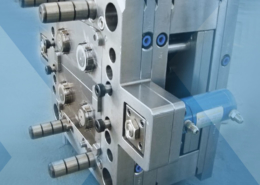
3D-printed Injection Molds Save Medical Device OEMs Time and Money - plastic mol
Author:gly Date: 2024-09-30
In booth 1911, Accumold will be showcasing some of the tiny titans it has produced to exacting specifications for medical device OEMs over its nearly 40-year history. A highlight are thin-walled cannulas that the company can now micro injection mold at volume.
With regard to machinery, there is a strong move towards “copy & paste” systems and processes in both Europe and North America. The global medical team at Sumitomo (SHI) Demag, led by business development director Anatol Sattel, are also noting more requests for remote system access to historical machine data. This is predominantly to assist with troubleshooting and monitoring validated process settings.
More recently, there is a stronger leaning in the medical market towards larger strategic and more complex projects, such as drug delivery devices and pen style injectors. This is predominantly due to the global growth in diabetes care, where demand for advanced glucose monitoring and insulin delivery devices is propelling innovation. Testament to demand, credible industry reports forecast that the diabetes device market will surpass $68.2 billion by 2032, almost triple its 2022 value.
Editor in chief of PlasticsToday since 2015, Norbert Sparrow has more than 30 years of editorial experience in business-to-business media. He studied journalism at the Centre Universitaire d'Etudes du Journalisme in Strasbourg, France, where he earned a master's degree.
For medical moulders already producing vital monitoring devices, including oxygen, weight, glucose and ECG devices, as well as infusion pumps and cannulas etc. and already meeting the exacting healthcare standards, the transition to homecare device production should be relatively seamless.
The company routinely molds cannulas at volume with outside diameters of 0.035 in. (0.889 mm), inner diameters of 0.027 in. (0.6858 mm), and wall thicknesses measuring 0.004 in.(0.1016 mm). “We have achieved this through attention to material choice, several critical design for manufacturing operations, assembly considerations, maintaining a balanced aspect ratio to avoid challenges associated with flow dynamics, cooling, structural integrity, and importantly through the use of our proprietary micro-molding presses,” explained Runyan. “Micro molding thin-walled cannulas is a game changer for medical device manufacturers, overcoming the labor-intensive, time-consuming, and expensive traditional thin-wall cannula manufacturing processes such as extrusion, tipping, and gluing to a metal hub.”
Vertical integration enables the company to operate as a one-stop partner in the development and manufacture of medical devices and components, added Runyan. “Under one roof, Accumold offers design and material assistance, micro tool fabrication, proprietary micro-molding services, cutting-edge metrology, assembly, and automation, and this facilitates the streamlining of customer’s medical product development process, and the attainment of optimal outcomes in terms of timeliness, cost, and accuracy.”
In 2023, the global medical injection moulding market size was estimated at $22.54 billion. It is expected to grow at a compound annual growth rate (CAGR) of 5.8% from 2024 to 2030. Much of this growth is being driven by advances in self diagnostics, the home healthcare sector, improved healthcare infrastructures in emerging economies, and an ageing population, which WHO predicts will double by 2050.
With significant access to start-up finding, telehealth is the boom-market to watch. It is current exhibiting a CAGR of 19.7% between now and 2030. Online video and audio consultations with physicians and medical consultants are increasingly being used to deliver quality healthcare while simultaneously reducing heavy work and cost burdens. The telehealth segment is split between services and products. Items such as wearable patient monitoring and telecommunication devices accounts for around one third of the market.
Exhibitor Accumold will explain how micro molding thin-walled cannulas reduces labor requirements and cost compared with conventional production methods.
To support these efforts, the company’s R&D team continues to develop an IoT dashboard to facilitate data analysis and visualisation, transfer and storage of know-how, as well as maintenance planning and prediction. Within this assistance system, additional autonomous and interconnected functions are being conceived to provide valuable insight into the machine performance and different production variables.
Now that NPE2024 is history, there are some admittedly smaller but still worthy trade shows on the horizon for sourcing suppliers of plastics processing services. One that you may want to consider attending is Plastec South, co-located with Medical Design & Manufacturing (MD&M) alongside packaging, automation, design and manufacturing, and Powder Bulk Solids trade shows under the IME South umbrella in Charlotte, NC. In particular, a pioneer of medical micro molding will be exhibiting at the event in June.
MedTech is a multi-billion-dollar manufacturing sector. Unsurprisingly, industry analysts are always keen to pinpoint the newest transformational medical and life science technologies that are expected to shape future treatment pathways.
The development of process optimisation systems, integrating material and knowledge with simulation tools is probably the most exciting development on the horizon, claims Sargisson. Such systems will enable processors to observe advanced settings and capture deeper processing insights.
In 2024, Sumitomo (SHI) Demag will host its inaugural productivity roadshow. With four stopovers planned for July in the UK and Ireland, including Limerick, customers will be invited to explore all the latest trends, productivity and profit-enhancing technologies.
To support these advances and in order to meet the explicit quality management and validation ISO 13485 standards for medical devices, Sumitomo (SHI) Demag introduced new machine user parameters, digital quality control and KPI analytics into its IntElect S medical production package. One of these advanced Med-Spec demo cells is now located in Limerick, Ireland. This will enable customers to perform validations, run tool trials and use the facility to provide valuable process optimisation training to technicians.
“Accumold is rightly today acknowledged as the world leader when it comes to the manufacture of extraordinarily small plastic parts that require extreme precision — typically measured in microns,” said Paul Runyan, VP of sales and marketing. “The company is adept at the production of small-sized parts with micro features from 5 cm to less than 1 mm, and has specific expertise in insert molding, two-shot molding, and cleanroom molding using an array of materials including PEEK, liquid crystal polymers, and most engineering thermoplastics.”
High profile acquisitions of diagnostics companies, IPO listings, strategic partnerships, and the rise of virtual care platforms provide further assurance that the diagnostics market is on the cusp of another huge growth curve. This all indicates that there are clearly exciting opportunities ahead for moulders operating in the high tech medical device and diagnostics product development and production space.
Regional medical director of the Sumitomo (SHI) Demag team Andrew Sargisson shares his industry insight and global predictions for the medical market, touching upon how these latest trends are influencing investments in medical injection moulding facilities worldwide.
The medical device industry demands absolute precision, totally repeatable manufacturing processes, and zero failure rates for products that are frequently used in safety-critical applications, notes Accumold in its announcement.
The company’s ultimate vision is an intelligent machine that can independently make predictions about part quality, machine wear and failures and deliver optimisations online. Enabling greater process consistency and allowing for real-time machine maintenance to be adjusted accordingly.
Thermoplastic and LSR moulding continues to be used extensively to manufacture a huge variety of everyday medical applications. The range is broad and can include implantable components, test tubes, petri dishes, PCR tubes, pipette tips and other labware, as well as medical monitoring devices, drug delivery components and surgical equipment.
The ISO 13485–certified company is sufficiently large to offer affordable pricing and the capacity and infrastructure to ramp up to full mass-volume manufacturing, he added.
The medical market, particularly diagnostics, was strongly influenced by the Coronavirus pandemic. As anticipated, there has been a natural levelling-off for pandemic-related consumables.
Also observed during the pandemic, larger scale adoption of home healthcare and smart diagnostic devices, continues to accelerate at pace.
IME South comes to the Charlotte Convention Center in Charlotte, NC, on June 4 to 6, 2024. In addition to more than 300 exhibitors on the show floor, the event features more than 40 educational sessions led by experts in 3D printing, medical technology, packaging, and smart manufacturing. A welcome reception is scheduled at the NASCAR Hall of Fame on June 4. Tickets are available for purchase when you register to attend.
GETTING A QUOTE WITH LK-MOULD IS FREE AND SIMPLE.
FIND MORE OF OUR SERVICES:
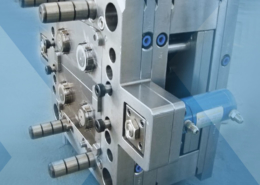
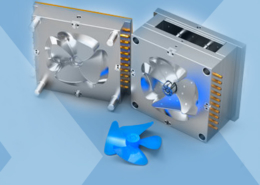
Plastic Molding

Rapid Prototyping
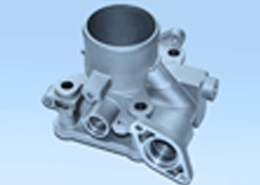
Pressure Die Casting
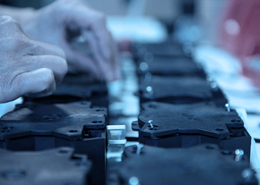
Parts Assembly
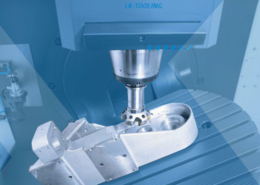