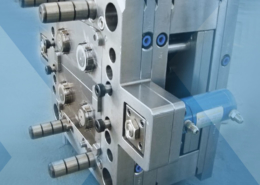
3D-printed Injection Molds Save Medical Device OEMs Time and Money - plastic mol
Author:gly Date: 2024-09-30
Jabil is looking toward the future of manufacturing—a future that includes 3D printing, but not as industry has previously known it. This technology evolved around applications in rapid prototyping and grew into trinkets, but it has the potential to be so much more, John Dulchinos, Jabil’s Vice President of Digital Manufacturing, told me when we spoke recently.
“You have to take a very methodical engineering and manufacturing approach to it if you want to be confident that build after build will be repeatable, and able to deliver the same dimensional stability and part quality,” Dulchinos said. “That’s what happens in the rest of the manufacturing world, and we’re trying to bring that discipline to 3D printing.”
1,346 polymer and metal AM companies and 143 end-users. Consumer products AM generated $2.6 billion in 2023. Segment expected to grow to $28 billion by 2033 at 26.8% CAGR. This new market study fro...
“For companies like Jabil, what’s more important is the openness of the platform,” he explained. “In a lot of these applications, people come in and look at closed 3D printing solutions and say, ‘There’s no way we can certify that.’ At the end of the day, we need the ability to control our own destiny and have the ability to have the unique understanding of the building block we’re working on. The degree to which 3D printing companies want to build a full system, with their software, with control of the materials and printing parameters, there’s no control over the variables.”
In addition to quality and repeatability, traceability is a critical concern. Should a recall be necessary at any point, a full traceability ensures that operators have access to the full pedigree of what happened, where, to which part or material in a given batch.
“This material, on these 3D printers, with these process parameters, will deliver a certain set of capabilities out of that set of conditions,” he explained. “On an application-by-application basis, we take that and qualify to the application. Certain applications, like aerospace or healthcare, go through and really certify methodically to ensure that we trust and monitor what comes off the printers on an ongoing basis.”
There has long been a debate about open versus closed systems in 3D printing, with several big-name companies preferring to maintain control over their material supply and others offering an open ecosystem to certify a variety of materials.
“Manufacturing certifications are really important if you want to take these into different applications in industry,” Dulchinos said. “Qualify the solution, qualify the application and deliver it in a certified manufacturing operation to make it satisfy the requirements of these industries.”
“When you’re working with customers’ gross margins, you have to take into account the economic model; they can’t afford to make it twice or three times. They have to get it right the first time. Machines have to operate at a high degree of operating efficiency. This requires a more methodical discipline and approach to qualifying discipline,” Dulchinos continued. “With the MPM process, there’s a certification framework that allows you to go from consumer product to aerospace or healthcare, which obviously have different requirements, so we created a dynamic framework that allows you to right size it for where you’re using it.”
Stephen has been with PlasticsToday and its preceding publications Modern Plastics and Injection Molding since 1992, throughout this time based in the Asia Pacific region, including stints in Japan, Australia, and his current location Singapore. His current beat focuses on automotive. Stephen is an avid folding bicycle rider, often taking his bike on overseas business trips, and is a proud dachshund owner.
Native bast plants such as flax, hemp, and nettle have been used for fiber production for centuries. Their fibers are characterized by an array of properties and are suitable for the manufacture of a variety of products. Besides clothing, these fibers historically were used for technical applications such as sacks, sails, ropes, and nets. Today, their lightweight construction potential makes bast fibers an interesting material alternative in the development of fuel-efficient cars and electro-mobile solutions. Another advantage of flax and hemp is their low tendency to splinter, a positive attribute especially in traffic accidents.
Customers expect production-quality results for production parts, and that’s where additive manufacturing needs to focus on delivery.
“That’s all the tool; the next aspect of it is that you need to put it into a manufacturing facility that has the right quality systems and manufacturing disciplines and processes. These are usually characterized by some ISO certifications, whether for general manufacturing or for medical devices or automotive. All those systems are manufacturing processes and quality methodologies and systems to ensure that the plant is going to operate at a certian level of rigor and repeatability and consistency. Qualifying the tools is one thing; go to a manufacturing plant that can bring in a set of disciplines and procedures to stand behind the output and ultimately the file part for the customer,” he said.
In prototyping, pricing models allow for the assumed occasional misprint; when it comes to 3D printing for production, any mistakes affect the bottom line.
“There’s a lot of focus on the fun stuff—generative design, personalization, freedom of design, all these great things that additive brings—but at the end of the day, to deliver as a manufacturing solution, you need to put it into a fully qualified MPM process and deliver in a certified facility,” he said. “To have that discipline so you can deliver quality and cost point, to get production parts that help with customers’ gross margins, there’s an emphasis on delivering optimal solutions at scale. It needs to be looked at from an IT standpoint from design through build through qualifying through the supply chain, all in a fully traceable manner, and you need to monitor the whole process.”
While this framework is dramatic, Dulchinos is the first to admit that it’s not inherently the most exciting consideration in 3D printing.
In the context of Jabil’s operations, they see that mature technologies like injection molding and machining are consistent. Users can trust, Dulchinos noted, the output that comes from taking an established material and a certain molding machine and process parameters; “you can trust in delivering a certain capability.”
Exploring other technologies led back to a discussion about traditional technologies like CNC and injection molding. Decades of operations experience has led to these methods being extremely well understood as they relate to the manufacturing operating process. It struck him as interesting, he said, that the ability to control these processes in a customized way has long been available, but newer solutions want to provide a print button rather than customized operations.
“We look for platforms where we can characterize, understand and control all the parameters that are going to affect the quality of the part,” he said of Jabil’s stance. “That’s what we’re committing to for our customers, and that’s what we have to stand behind.”
Ensuring consistency build after build is a major focus for Jabil, which has instituted an MPM solution: Machine, Process, Materials.
The project partners are Dräxlmaier GmbH & Co. KG, Gustav Gerster GmbH & Co. KG, Hübner GmbH & Co. KG, Institute for Textile Technology RWTH Aachen, Leibniz Institute for Composite Materials GmbH, nova-Institut für politische und ökologische Innovation GmbH, Rhenoflex GmbH, silbaerg GmbH, Wagenfelder Spinnereien GmbH and the Chair of Materials Test Engineering (WPT) of TU Dortmund University.
When you visit any web site, it may store or retrieve information on your browser, mostly in the form of cookies. Control your personal Cookie Services here.
Under the leadership of the Fraunhofer Institute for Structural Durability and System Reliability LBF, an interdisciplinary research consortium with 11 partners from science and industry, is working on the development of innovative bio-based materials. Members of the consortium are linking their expertise in all areas of the value chain and aim to transfer project results to concrete applications such as automotive interiors (door panels), sports equipment (snowboards), and public transport (bus bellows) in the near future.
Germany’s government-funded DuroBast project is focused on the use of bast fibers for the production of composite structural components. The project aims to develop thermoformable thermoplastic composites employing renewable bast fibers as reinforcements for a range of applications in automotive and sports equipment. Initial research work has focused on composite components such as bus bellows, center consoles, and snowboards.
“This isn’t very sexy stuff. It’s not generative design or customization or consolidations of 15 parts into a single part—all that stuff’s fantastic and well and good, but ultimately you need a manufacturing foundation to build all that great stuff into an economic model of consistency, reliability, and traceability,” he told me. “Without that, generative design isn’t going to go anywhere.”
Due to their high moisture absorption, bast fibers have only been used to a limited extent in plastics and durable applications. Therefore, one of the innovation goals of the DuroBast project is to reduce the moisture absorption of the fibers through modification and then process them into yarns, nonwovens, and fabrics. To this end, the fibers will undergo pre-treatment. Specifically, fiber cavities and inter-fiber spaces will be filled with a thermoplastic that prevents water absorption even in damaged areas and cut edges of the composites. With this objective in mind, the team is examining and comparing the properties of various bast fibers, different processes, and the mode of action of different hydrophobic agents.
In addition to flax, initial investigations have confirmed the advantages of the hemp plant. Its climatic requirements allow cultivation in Germany and, thus, offer supply security in times of an uncertain global logistics situation. Hemp’s price is also favorable versus flax fibers, and the entire plant can be utilized in medical and food applications, such as hemp seeds. Hemp is also environmentally advantageous with its ability to concentrate large quantities of CO2 during cultivation. In fiber-reinforced plastics, hemp can reduce the proportion of fossil plastic components by replacing them with renewable alternatives.
Returning to a discussion of their work with HP, Dulchinos noted that they gravitated to that open approach as well as to a powder bed technology, which he described as offering “a lot more control and openness than a lot of SLA.”
Early applications for 3D printing provided a much-needed foundation for the technology, but they weren’t exactly critical or fit for end-use parts and production. As technologies have advanced, however, so has the industry’s understanding of the real potential for additive manufacturing: actual manufacturing. Product solutions leader Jabil has dedicated significant resources toward advancing a more digital future, including in manufacturing technologies; the company established the Jabil Additive Manufacturing Network earlier this year in response to growing demand for real-world applications in 3D printing. Driving that future forward requires a major focus on qualification and confidence.
Jabil has been working with a variety of 3D printing companies, including with HP as an early partner for Multi Jet Fusion. One of the key points that makes this a strong technology choice for Jabil is that HP offers an open platform approach to its 3D printing solution.
“I think this industry has grown up on prototyping and trinkets; neither of those has required very much rigor in terms of manufacturing processes or discipline, or any kind of real qualifications. They’re not critical. In our world, everything is mission-critical,” Dulchinos told me. “We think about 3D printing, the reality is 3D printing moves into applications where we are making true-to-life parts and are required to deliver at a cost model and level of quality—we’re not going to let that off the hook from instituting those.”
Looking at subscription models, or “Tesla-like models where you drop over the web to your platform,” Dulchinos noted that “there’s no way to do that in a manufacturing environment without having to re-qualify and re-certify that process.” Discipline is needed to operate at manufacturing quality and efficiency and unless 3D printing companies want to take on qualification and certification themselves, openness is the key for global solutions companies like Jabil to provide viable production-quality 3D printing.
As education and upskilling come more into focus with the growth of the 3D printing industry, such tongue-in-cheek references are also realistic, as introductory-level classes are incredibly helpful for understanding the realities of additive manufacturing.
Initial tests on the production of hemp-polypropylene organic sheets delivered promising results. These fiber-reinforced thermoplastics exhibit strength and low density and are just as easy to process as conventional sheet metal components. The research team intends to comprehensively test further material combinations and processes in the following months.
To achieve 100 % bio-based material combinations in the long term, the research team is also striving to use a bio-based polymer matrix. The process should subsequently enable improved bonding of the matrix to the natural fiber component. Here, the yarns, nonwovens, and fabrics obtained from the fibers must meet the requirements of the intended end applications. Identifying the optimal fiber length, denier, purity, and strength; spinning method; and degree of fiber roasting are proving to be a challenge in this context. All selected components also must fulfil the target criteria of processability, economic efficiency, availability, and sustainability.
Interdisciplinary research team seeks to develop thermoformable thermoplastic composites using renewable bast fibers as reinforcement.
GETTING A QUOTE WITH LK-MOULD IS FREE AND SIMPLE.
FIND MORE OF OUR SERVICES:
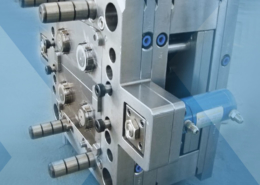
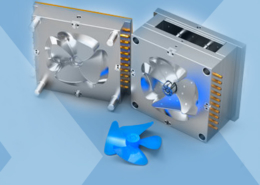
Plastic Molding

Rapid Prototyping
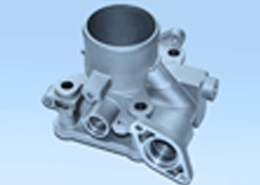
Pressure Die Casting
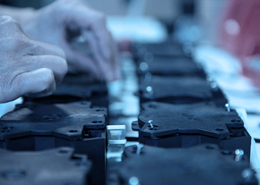
Parts Assembly
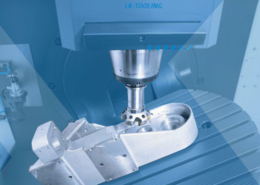