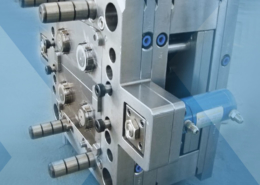
3D Printing With Foam – The Ultimate Guide - 3d printed soft plastic mold
Author:gly Date: 2024-09-30
“We’ve not eliminated jobs and, in fact, automation has increased the number of jobs we have,” said Ignatowski. He acknowledges that the jobs are more technical in nature: “The people who run the plants are called Process Technicians. Robotics do the repetitive tasks while people perform the technical jobs, [but] we have never replaced a person because of the implementation of technology,” stressed Ignatowski.
At the upcoming Fakuma trade show in Friedrichshafen (Germany), Swiss injection molding machine manufacturer Netstal will be presenting what the company says is a “world first”: injection compression molding on a stack mold. Netstal will be demonstrating the new technology at its booth in hall A7 (7303/7304), where a 15oz (425g) margarine tub made from PP and weighing only 10.7 g will be molded on a hybrid Elion injection press equipped with a four-by-four stack mold.
One advantage of Prism’s operating philosophy is that it has allowed the company to build its human resource requirements around its installed automation technology. Ignatowski explained that while some companies might hire a large number of people at first, then decide to automate and lay off 80% of their work force, Prism deployed automation technology from the get go.
Those are just two examples of how Prism’s Technology First approach solves problems, but the benefits are far reaching. It helps Prism maintain lean operational costs, which allows the company to compete on a global scale and win back jobs back from Europe, China and Mexico.
“Because of NAFTA, we’re in great shape and can boast that our components are 100% made in the USA,” Ignatowski added. “We can compete with low-cost countries because of our approach to technology, lean operations and designing in quality throughout the process. In fact, while others are shipping parts from China, we’re shipping products to China.”
Technology has also brought another benefit to Prism. Because of its rapid growth, the company identified a need for additional warehouse space. While some companies might knock out a wall and add on a brick-and-mortar solution, Prism resolved its problem with technology. “We came up with the Very Narrow Aisle Racking system that greatly reduced the space separating rack units,” Ignatowski explained. “Pallets are placed and retrieved using an automated forklift that follows an embedded wire in the floor. An operator drives the fork lift, but in the aisle they can only go forward and backward. That system allows us to have three inches of clearance on the fork lift in the aisle. We implemented this in Chesterfield and the new acquisition in Pennsylvania, as well.”
Until she retired in September 2021, Clare Goldsberry reported on the plastics industry for more than 30 years. In addition to the 10,000+ articles she has written, by her own estimation, she is the author of several books, including The Business of Injection Molding: How to succeed as a custom molder and Purchasing Injection Molds: A buyers guide. Goldsberry is a member of the Plastics Pioneers Association. She reflected on her long career in "Time to Say Good-Bye."
Ignatowski told of a recent high-level meeting with a customer in Prism’s Texas plant. The customer told Prism that it was “one of the best suppliers but that it wanted to put as much business in Mexico, as possible.” They wanted us to site a plant in Mexico, said Ignatowski. “I told them we’ll do that, but we’ll have to add cost to the components because we have no labor content at the Texas plant, which means we won’t realize any labor savings, and the infrastructure costs are higher in Mexico. We’re now getting a significant amount of business from the customer as it localizes its requirements in Texas, and we’re shipping parts to its plant in Mexico. We’re able to do that because of our automation and subsequent quality record. It comes down to the right jobs for the right work.
Moreover, using a stack mold significantly increase productivity, while the technology reduces material costs by up to 20%, in addition to providing total flexibility in terms of shape, appearance and decoration of the manufactured part.
At the upcoming Fakuma trade show in Friedrichshafen (Germany), Swiss injection molding machine manufacturer Netstal will be presenting what the company says is a “world firstâ€: injection compression molding on a stack mold. Netstal will be demonstrating the new technology at its booth in hall A7 (7303/7304), where a 15oz (425g) margarine tub made from PP and weighing only 10.7 g will be molded on a hybrid Elion injection press equipped with a four-by-four stack mold.The innovative technology is the result of a collaboration between mold manufacturer Plastisud, automation specialist Machines Pagès and Netstal. While the stack mold with 4+4 cavities is impressive enough, turning out standard-sized margarine with IML decoration in a cycle time of five seconds, the truly revolutionary aspect of the whole process is hidden from view, according to Markus Dal Pian, Vice President, Sales & Marketing at Netstal.“The polypropylene packaging is not injection molded but manufactured in an injection compression molding process," he explained. "This combination of injection compression molding and stack mold is a complete novelty in the industrial production of packaging."The cavities are partially filled in only 100 ms with extremely even results and the process is performed at a low pressure to prevent tension in the material. The high quality of the platen parallelism guarantees a synchronicity of 99.98 % between the mold, machine and automation system.The stack mold, especially adapted to the requirements of the new production process, was developed in a few short months by Plastisud. The unique injection compression molding technology guarantees perfectly balanced parting planes with an extremely low dispersion rate."The special design of the stack mold developed by Plastisud plays a key role in this application,†Thomas Iten, PAC Application Engineer at Netstal emphasized. Machines Pagès provided specific know-how in the area of handling systems for in-mold labeling (IML) to ensure that the automation process has been adapted perfectly to the machine and mold.According to Iten, this configuration, in which the injection compression molding process is combined with a specially balanced stack mold, is “a genuine innovative leap." The fundamental benefits of injection compression molding include narrow wall thicknesses and a lighter product resulting in lower unit costs. Furthermore, the end product (lids in particular) shows fewer signs of distortion and has a greater dimensional accuracy due to the lower stresses placed on the material.
Currently, Prism operates four molding facilities: In addition to the plant at its Chesterfield headquarters, the company has a molding footprint in Port Huron, MI; Harlingen, TX; and Meadville, PA. Prism serves the automotive and industrial markets with various components including safety parts, connectors and sensors, electronics housings and steering and drivetrain parts.
As manufacturing became global, Prism relied on its automation technology to remain competitive. Under the Technology First banner, the company has removed almost all manufacturing labor costs from its cost model. “We’re not showing labor in our cost model breakout—that is what technology has done for us,” said Ignatowski.
The “Technology First” mindset has been a constant at Prism Plastics (Chesterfield, MI ) since the day the custom injection molding company was founded in 1999. “That was a time when molders were plentiful,” said Jeff Ignatowski, Director of Marketing, during a phone interview with PlasticsToday. “We decided then that we’d use technology. We chose the highest technology available in molding machines and robotics. We then standardized equipment: By blending automation and the human element, we have become efficient and cost effective. That mindset exists across the board, so that each of our plants operates exactly the same way.”
The company’s “Technology First” approach allows it to compete on a global scale and win back jobs from Europe, China and Mexico.
As Prism wins more programs, keeping manufacturing on American soil, the result is more high-tech jobs for skilled American workers.
Prism recently installed a new molding line with three collaborative robots. One robot hands a part to another robot, which hands it off to a third robot, which performs a final inspection and places the part in a box.
GETTING A QUOTE WITH LK-MOULD IS FREE AND SIMPLE.
FIND MORE OF OUR SERVICES:
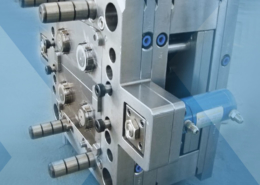
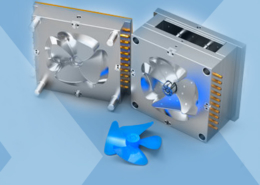
Plastic Molding

Rapid Prototyping
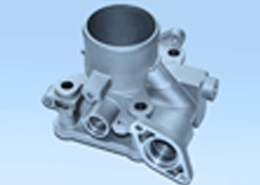
Pressure Die Casting
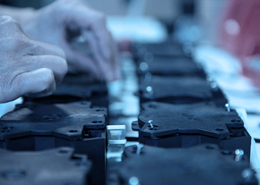
Parts Assembly
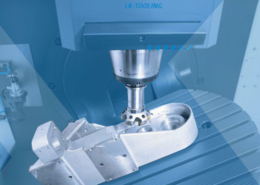