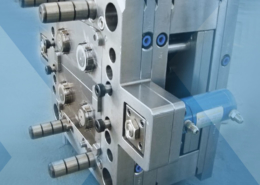
3D Printing Start-Up Competes with Injection Molding - low volume injection mold
Author:gly Date: 2024-09-30
Angelika Homes comments: “Unlike our former MES systems, this one logs every single aspect of a trial and the results, giving us insight for every single shot. This data is extremely valuable as it represents the entire processing sequence and enables us to draw deeper conclusions about how materials perform under certain conditions and how a customer might later process it.”
We will only use your email address to send you the newsletters you have requested. We will never give your details to anyone else without your consent. You can unsubscribe at any time by clicking on the unsubscribe link at the bottom of every email, or by emailing us at [email protected].
Items ranging from food and drink packaging, to cosmetics and building materials, have been made from glass in collaboration with a team of expert glassblowers.
News from Dezeen Events Guide, a listings guide covering the leading design-related events taking place around the world. Plus occasional updates and invitations to Dezeen events.
These include a glass container that uses water channels to keep its contents from oxidising, and a loose-leaf teapot to replace single-use bags.
Reusable glass vials for pills can replace disposable blister packs, while glass tiles could replace the plastic used to insulate wires.
Sent every Thursday and containing a selection of the most important news highlights. Plus occasional updates on Dezeen’s services and invitations to Dezeen events.
The polymers in plastic, on the other hand, degrade a little every time they are recycled, meaning they need to be mixed with new, virgin plastic to remain viable.
Others turned their attention to the personal care industry, designing packaging that would facilitate a keep-and-refill system. Customers would hold on to their glass containers and top up everything from make-up to cleaning products in the shop.
As food packaging is a major contributor to the plastic waste crisis, various projects proposed more sustainable alternatives.
BASF’s MES informs the cell when the current produced sample setting is about to end, lining up the next mold application. Immediately after the injection process stops, cooling of the mold insert is directed by the integrated temperature control unit interface.
Automation Systems Senior Engineer at Sumitomo (SHI) Demag, Markus Hausmann explains: “In order to lower the temperature to 80°C and depressurize the insert to guarantee that the SDR robot can remove the mold insert safely, our machine control has to talk and interact seamlessly with BASF’s MES.
At any time, up to 12 interchangeable inserts can be loaded to the side magazine and then swapped automatically into the injection molding machine. By integrating an HB-Therm temperature control system with Sumitomo (SHI) Demag’s machine control, automated mold insert changes can be completed safely and efficiently, even when running the process at high mold temperatures.
Then, the change of the mold inserts is synchronized to the cell control via output and input signals with transmission of the new mold data record via the robot interface. After the change of the mold insert, the temperature control units are heated up again. Automatic operation resumes and a new mold data record is initiated as soon as the target temperature is reached.
Another project intent on repurposing waste comes from Gao Ziyu, who designed a fishbowl that doubles up as a watering can.
Jaxon Pope created a series of glass vials that could be used as an alternative to the throwaway blister packs in which medication is commonly sold.
Taking center stage in the cell is Sumitomo (SHI) Demag’s ultra-precise IntElect 1000 kN injection molding machine. Selected for its compact design, energy efficiency, and repeatability, the IntElect’s enhanced welfare and safety features were also welcomed by the team of 30 research operatives at the facility. Progressive solutions to automate mold changes and low noise emissions combined with fully-digitized robotic processing solutions also received high marks.
"By moving the wiring from inside the walls to their surface, they are easier to access for maintenance or modification without having to damage walls or replace the whole system. If a house is demolished, the tiles can easily be reused or recycled."
Sumitomo (SHI) Demag’s IntElect 1000 kN injection molding machine is at the core of a fully digitized manufacturing cell producing test specimens for product development and research involving thermoplastic polymers and compounds.
For operative safety and efficiency, a linear SDR 5-35S robot serves two purposes. A new feature is full automation of the selection and placement of 12 interchangeable mold inserts from a magazine located within the cell. After the part is molded, the same robot fitted with a multifunctional gripper gently extracts the test specimen from the mold and passes it to the small six-axis, articulated-arm Yaskawa GP8 robot for precise cutting of the specimens from the gate using a servo spindle drive punching machine.
Many of the specimens processed at BASF’s technical centre are high-temperature thermoplastics, fiber reinforced and often flame retardant. Consequently, melt temperatures can reach up to 400°C with mold temperatures hitting 180°C.
For BASF, solving the punch challenge was one of the greatest engineering accomplishments. Due to its extensive application profile, BASF tests a wide range of materials from soft and tough to stiff and brittle polymers. There are also many different sample geometries, including thicknesses varying from 0.8 to 4 mm. All BASF test specimens are manufactured in accordance with the ISO 294 standard. This specifies the precision of the sprue system and specific requirements each sample geometry must fulfil. “Removal by punch is a pre-requisite, as it does not change the material properties and eliminates dust particles,” explains Hausmann.
News from Dezeen Events Guide, a listings guide covering the leading design-related events taking place around the world. Plus occasional updates and invitations to Dezeen events.
We will only use your email address to send you the newsletters you have requested. We will never give your details to anyone else without your consent. You can unsubscribe at any time by clicking on the unsubscribe link at the bottom of every email, or by emailing us at [email protected].
Our most popular newsletter, formerly known as Dezeen Weekly, is sent every Tuesday and features a selection of the best reader comments and most talked-about stories. Plus occasional updates on Dezeen’s services and breaking news.
"I'm hoping that, by making the vases elegant and decorative, it will make users feel more comfortable with growing plants that aren’t typically perceived to be beautiful."
Integrating BASF’s existing mold insert concept and special features into the injection unit, the installation also includes a thermal temperature control unit and a new digital Manufacturing Execution System (MES) to map each test sequence. Reinhard Jakobi, Head of Performance Materials Processing at BASF, describes the project as an achievement of advanced engineering combining mature technology with state-of-the-art automation and molding precision.
"It utilises no plastic or hybrid materials and is much more resistant to temperature, corrosion and rodents," he told Dezeen.
He added: "It can be produced using widely available resources, melted down and endlessly re-formed to make new products without a substantial loss of material or quality."
At the pilot center, the BASF research team typically configures 20 test settings daily on this machine. That means the control program of the cell has to be adapted to different materials, sample geometries, temperatures, and processing parameters. Every single setting that runs is recorded and documented digitally.
Different coloured scales on the side of each vial help the pharmacist fill in the right doses, while the lid is made from recyclable plastic to create an airtight seal.
"Glass has two main selling points in a cyclical system: its longevity and its recyclability," said Lund University student Riccardo Centazzo."It is an impermeable material with high corrosion and temperature resistance that can also be exceptionally hard."
"The medicine is initially purchased with an additional cost for its packaging and can then be returned to the pharmacy for a refund or refilled without an additional package charge," he explained.
The tiles would be attached to the wall using a backplate. Its internal pattern allows wires to be neatly organised before they are safely enclosed behind a removable front face.
Creating tomorrow’s polymer innovations starts with understanding the chemical and mechanical performance and processing conditions of materials. At BASF’s Injection Molding & Extrusion Pilot Plant in Ludwigshafen, Germany, the newest all-electric, fully-automated injection molding cell from Sumitomo (SHI) Demag is delivering pioneering and repeatable results for more than 4,000 tests a year.
Our most popular newsletter, formerly known as Dezeen Weekly, is sent every Tuesday and features a selection of the best reader comments and most talked-about stories. Plus occasional updates on Dezeen’s services and breaking news.
In the system Pope is proposing, pharmacies would receive medication in bulk before portioning it out into these vials according to the needs of each customer.
"Used vials are sent to a cleaning facility to be industrially cleaned and a vial that is considered too scratched can be sent back to the manufacturer to be melted down and used in the production of new vials."
The resulting 31 designs were presented at the Stockholm Furniture & Light Fair as part of an exhibition called Transparent.
In this way, the potassium, phosphorous and nitrogen that build up in the water over time aren't flushed down the drain when the water gets changed, but instead used to help plants grow.
Sent every Thursday and containing a selection of the most important news highlights. Plus occasional updates on Dezeen’s services and invitations to Dezeen events.
Another student encased coloured glass offcuts – which are harder to recycle due to the chemicals used to dye them – within clear glass to create decorative, Terrazzo-like tiles.
Circularity, which involves eliminating waste and pollution while sustaining natural systems, was a big topic at Stockholm's Furniture & Light Fair. The award for best standing going to Note Design Studio's re-usable design for furniture brand Vestre.
Julius Nobling, meanwhile, created a series of vases in different shapes and sizes, to draw attention to the little-known fact that various vegetables can easily be re-grown at home with nothing but scraps and stumps that would otherwise have gone to waste.
Centazzo's project is a system of tiles that makes use of the insulating properties of glass to replace the vast amount of mixed plastics normally used to encase electrical wires in the home.
Pooling its engineering competences and technological resources, BASF’s Performance Materials division in collaboration with Sumitomo (SHI) Demag and H + S Automatisierung have created a manufacturing cell to produce a range of test specimens for the product development and research activities of thermoplastic polymers and compounds.
A quarterly newsletter rounding up a selection of recently launched products by designers and studios, published on Dezeen Showroom.
"I created a thin, long vase for things like leeks and spring onions so that they could grow straight," he explained. "The round one is meant for herbs like basil or coriander and has a small opening so that the cutting can fit easily without falling."
Contact lens cases, vegetable vases and pill packets are some glass objects by students at Lund University in Sweden to explore how the reusable could help the transition to a circular economy.
The fair is part of the wider Stockholm Design Week, which also saw design studio Form Us With Love launch a mix-it-yourself hand soap that almost entirely eliminates plastic waste.
A quarterly newsletter rounding up a selection of recently launched products by designers and studios, published on Dezeen Showroom.
The multifunctional gripper ensures all sample geometries are placed with exacting precision onto the punch plate. This is complex in itself because BASF works with many materials that have high fiber glass content, which can cause warpage. Describing how the servo driven parallel punch gripper overcomes the challenge of placing parts securely onto the punch plate, Hausmann notes: “If the test specimens are not held sufficiently well in place, the punchings could be crooked or not conform to specified quality standards.”
GETTING A QUOTE WITH LK-MOULD IS FREE AND SIMPLE.
FIND MORE OF OUR SERVICES:
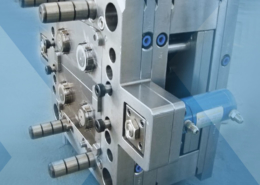
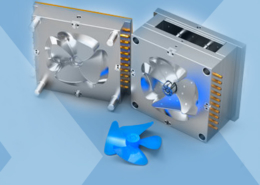
Plastic Molding

Rapid Prototyping
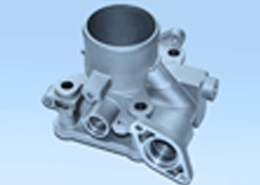
Pressure Die Casting
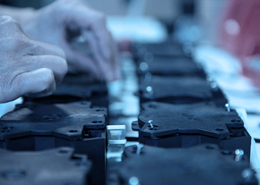
Parts Assembly
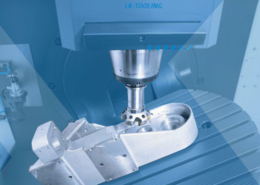