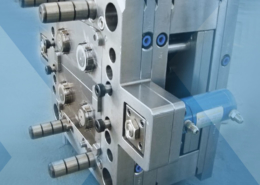
2022 Top Shops Benchmarking Survey: Cost Conquerors - top plastic injection mold
Author:gly Date: 2024-09-30
Editor in chief of PlasticsToday since 2015, Norbert Sparrow has more than 30 years of editorial experience in business-to-business media. He studied journalism at the Centre Universitaire d'Etudes du Journalisme in Strasbourg, France, where he earned a master's degree.
General Pattern, a fourth-generation, woman-owned low- to medium-volume plastics processor, adopted Mantle’s technology to enhance flexibility in building production tools at prototype lead times and minimize the need to build entire tools by toolmakers. Cost, lead time, and labor were significantly reduced: Using Mantle’s technology, the company was able to shave off 3.5 weeks of lead time in tooling fabrication and required just four active hours of a toolmaker’s time.
The Series C funding round was led by Schooner Capital, a Boston-based private investment firm, joined by its largest existing investors, including Fine Structure Ventures, Foundation Capital, Corazon Capital, 11.2 Capital, and Build Collective.
Continued reshoring of manufacturing coupled with the skilled labor shortage in the United States has created a uniquely attractive business opportunity for Mantle’s TrueShape technology.
Mantle, an innovator in applying metal 3D-printing technology to the fabrication of precision tooling, reports that it has reached a significant milestone by securing $20 million in Series C funding. This raises the company’s total funding to more than $61.5 million and marks a crucial step toward widespread adoption of its precision metal manufacturing technology, the company said in the announcement.
Medical device, automotive and consumer goods. Some of these moulds will end up in the USA as there is very little import duty from the EU to the USA for moulds.
Tooling made via Mantle’s TrueShape technology have produced millions of parts while reducing both tooling lead time and cost. Image courtesy of Businesswire.
“We purchased a Mantle system for two reasons — to reduce time-to-market for our products and to make our toolroom more efficient while attracting next-generation talent to Heyco,” commented Vice President of Operations Danny Anthony. “By using Mantle to print mold tooling, we have already brought a new product to market two months faster than we would have otherwise. We also increased the throughput in our toolroom by giving our toolmakers access to the latest technology that makes them significantly more productive.”
We can see that globalisation turns into localisation. Since we have a lot of customers in Europe, we thought that being in the EU with a maximum two- to three-hour plane ride from all the big European factories, would be very helpful. Also, we can see that many US customers do not want to source in Asia anymore, but are very open to Europe. So far, orders in VEM Bulgaria are up more than 80 per cent compared to last year.
Investors are bullish on Mantle’s metal 3D-printing system that reportedly can slash tooling costs by more than 65% and development cycles by as much as 90%.
Beyond the sheer numbers, some of those jobs require a specific skillset and command commensurate compensation. Moldmaking is in that cohort, which is why Mantle’s technology is attractive to investors and customers alike. The TrueShape system reportedly delivers the accuracy, surface finish, and tool steel properties required for demanding tooling applications, while reducing tooling lead times and costs. Mantle has gathered some testimonials to back up that claim.
We will be present at Medical Design & Manufacturing West in Anaheim, California in August, as well as at Fakuma in Friedrichshafen, Germany, in October – aside from the K Show, we know this is the biggest plastics show in Europe. We also be present at Interplas in Birmingham, UK, in September.
While job creation numbers grow, employers are scrambling to find skilled workers to fill those positions, and it’s only getting worse. More than two million manufacturing jobs could go unfilled by 2030, according to a study by Deloitte and the Manufacturing Institute.
US government incentives and policies, such as the Inflation Reduction Act, along with geopolitical risks in various parts of the world that threaten global supply chains have buoyed near- and reshoring as well as foreign direct investment (FDI), according to a recent report from the Reshoring Initiative. The organization said that 2023 was the second highest year on record in terms of job creation linked to reshoring and FDI, adding 287,000 jobs based on its record keeping.
By focusing on printing tools for mass production rather than the parts themselves, Mantle said it has tackled the longstanding issues of high costs and lengthy production times associated with tool creation for mass production. This strategic shift has resulted in cost reductions for customers exceeding 65% and accelerated manufacturers' development cycles by up to 90%, it claims.
Business, not surprisingly, is booming: Last year saw double-digit growth in shipments, according to San Francisco-based Mantle.
Heyco Products, a US-based manufacturer of wire protection products and electrical components, deployed Mantle technology for in-house molding and toolmaking.
"Mantle is poised to revolutionize the global tooling industry," said Alexandra Manick, principal of Schooner Capital. "The company’s advanced manufacturing platform, TrueShape, is proven to deliver significant cost savings and, more importantly, unprecedented speed for its customers. This paradigm-shifting solution is readily adoptable and sorely needed to address persistent skilled labor shortages and accelerate product development timelines for industrial toolmakers and OEMs worldwide,” said Manick.
To shock you a little bit, the Europeans are already ahead of the Americans. Germany, for example, can, on a warm, sunny and windy day, already generate 100 per cent of its energy needs from renewable energy. Europe has a clear strategy and action plan for recycling different materials, especially plastics. The USA (at least the places I have been to in the last 12 months) is way behind and I hope they can learn from the Europeans very soon.
Based in Clovis, California, VEM President Marc Weinmann discusses the reasons for bringing his company’s toolmaking expertise to the European market.
Arburg is a world-class manufacturer of injection moulding machines. We will grow with them in Europe, but we are also working on a very big 2K project with one of the biggest medical device companies in the US, where Arburg supports us technically and where they, if successful, can ship a lot of their machines to California.
First of all, that is a very correct statement that not many industry insiders know. Bulgaria was/is the Toolmaking Capital of the Eastern Block so there is a lot of tradition, but also a skill set available. Most of the local engineers and toolmakers speak excellent English, as well as Russian. VEM is bringing the international exposure to the table, we now have seven nationalities working there in VEM. And with the latest technology (VEM has its first 5-axis CNC machine there), we can help them to improve and get to the next level.
GETTING A QUOTE WITH LK-MOULD IS FREE AND SIMPLE.
FIND MORE OF OUR SERVICES:
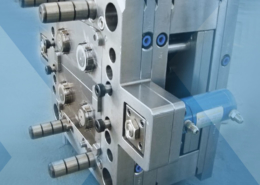
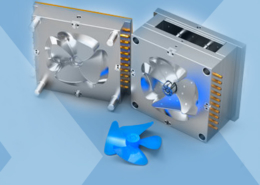
Plastic Molding

Rapid Prototyping
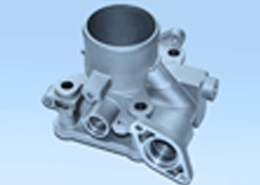
Pressure Die Casting
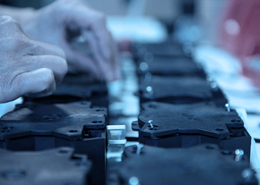
Parts Assembly
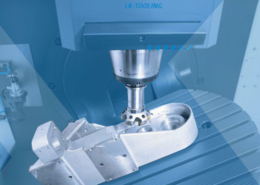