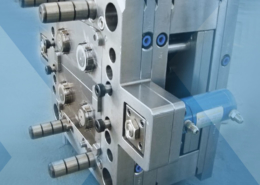
10 Cheap 3D Printing Services to Cut Your Costs - small batch injection molding
Author:gly Date: 2024-09-30
Nexa3D’s ultra-fast printers combine with Addifab’s soluble resins to print complex tools compatible with any injection molding feedstock.
Polymer 3D-printing company Nexa3D has completed the acquisition of Addifab, the developer of Freeform Injection Molding, a proprietary and patented digital tooling process that couples the design freedom of 3D printing with the mechanical performance of injection molding using a full range of engineering materials.
"I don't like to build what people want; I like to build what they need," Robert Schad told PlasticsToday upon the public debut of his new hybrid molding machine company, Athena Automation (Toronto, ON), at an open house coinciding with the recent Plast-Ex 2013 show (May 14-16; Toronto, ON).
As part of its growing commitment to EMEA, and in service of its growing reseller partner network, Ventura, CA–based Nexa3D plans to immediately leverage Addifab’s Copenhagen facility as its Customer Experience Center, comprising a product showroom, service and support hub for Europe-based customers, and warehouse and logistics center.
Combining complementary technologies developed by the two companies unlocks the full potential of digital tooling by blending the design freedom of 3D printing with the reliability of injection molding. The acquisition positions Nexa3D for accelerated growth in the fast-growing additive manufacturing space, said the company. It adds foundational intellectual property and capabilities to Nexa3D’s product line and accelerates its resin formulation and industrial production initiatives. “We believe that the market-validated strategic fit between our businesses and products, combined with the expanded capabilities in product development, next-gen resin formulation, channel coverage, manufacturing, and marketing, will result in significant revenue and accretive growth,” said Avi Reichental, co-founder, chairman, and CEO of Nexa3D.
The acquisition follows a successful year of joint go-to-market collaboration between the two companies in both North America and EMEA, said Nexa3D in the announcement. The joint sales and marketing efforts reportedly resulted in converting dozens of customers from traditional to digital tooling thanks to the time and cost savings. The end-to-end solution formalized by the acquisition combines the speed of Nexa3D’s ultrafast 3D printers with Addifab’s high-impact, high-temperature soluble resins to print complex tools compatible with any injection molding feedstock.
"I don't like to build what people want; I like to build what they need," Robert Schad told PlasticsToday upon the public debut of his new hybrid molding machine company, Athena Automation (Toronto, ON), at an open house coinciding with the recent Plast-Ex 2013 show (May 14-16; Toronto, ON).Most anyone in the plastics processing industry will recognize the name of the iconoclastic founder of Husky Injection Molding Systems, which the German-born Schad built into one of plastics' most dominant injection molding machine makers, especially in the PET preform and closures market. If Schad sounds a bit like Apple's Steve Jobs he has good reason. The visionary, no-nonsense leader recognized the virtues of vertical integration early on, meaning Husky not only made injection molding machines, but also molds, hot runners, robots, and auxiliaries.
Addifab's xMold resin is compatible with the entire range of off-the-shelf thermoplastic materials, including reinforced high-performance feedstocks. Metals, ceramics, and silicones are also covered, enabling users of Nexa3D printers to tap into applications that otherwise would require a substantially larger capital investment. A tool printed with the xMOLD resin is soluble — it does not require complex slides and gates — giving customers the flexibility to test and iterate more frequently. Moreover, the user doesn't have to be an experienced toolmaker to quickly design an injection molding tool using Addifab software or Solidworks.
One high-profile adopter of the technology is Wilson Sporting Goods. Its R&D team was able to produce and test multiple designs simultaneously of its youth baseball bats using final manufacturing materials. This would not have been possible using any other 3D-printed tool, according to Nexa3D.
“Soon after teaming up with Nexa3D, it became increasingly apparent that our combined solution unlocks tremendous opportunities for customers looking to create complex injection molding tools quickly and affordably. A year into our enormously successful commercial collaboration and dozens of customer implementations with the likes of PepsiCo and Wilson Sporting Goods, I’m thrilled that we are officially joining forces,” said Lasse G. Staal, co-founder and business development leader at Addifab.
Copenhagen-based Addifab developed, patented, and successfully brought to market a proprietary end-to-end digital tooling solution that includes a CAD-to-tool software generator, dissolvable tooling resins, and a 3D printing and production injection molding process. By combining the freedom of 3D printing with the industrial strength of injection molding, Addifab said its technology unlocks tremendous potential for contract manufacturers, regional molders, medical device companies, service providers, and low-volume manufacturers that want to offer same-day and next-day part production.
Schad eventually left behind the company he built after selling his majority stake in 2007 to Canadian private-equity investment firm Onex in a deal worth C$960 million overall. "It didn't work out to stay," he says simply.But Schad found he couldn't leave behind what he'd been doing since founding Husky in 1953 as a small machine shop. Originally intending to build air-boats after Husky, his attention soon returned to the plastics processing machinery he knows so well, and the Athena concept was born in 2008. "When I started, I set some very precise goals," he says of Athena. "I would either accomplish them or give up.""The main idea is to build a simple, cost-effective platform with energy consumption similar to all-electric injection molding machines. It can now be automated with the features needed all built into the machine. It's simple to install, and can be customized very quickly and cost effectively," Schad says.The Athena line utilizes servomotors in a hybrid platform to achieve repeatability and accuracy "as good as or better" than all-electrics while maintaining low energy consumption in part due to the active power supply that regenerates braking energy. The machines have a small footprint with large daylight and are quiet, operating at under 70 dB.The Athena machines will range from 150 to 500 tonnes, with screw diameters of 30-120 mm. A clean-slate, and cleanroom-ready design philosophy are at the heart of the Athena approach. The machines are built on a one-piece base and feature distributed controls interconnected by a PowerLink bus. All machines feature 150 mm of floor clearance for easy cleaning. All service connections (water, air, vacuum, electrical) are located at the injection end of the machine. Services are pre-routed through the machine base. Also standard are two-platen electric clamps with non-lubricated tiebars and a closed loop, leak-free oil return system for hydraulic components.A wide range of options include a fully integrated high-speed, side-entry robot, stack-mold carrier, integrated dual injection, and integrated hot runner and robot control, meaning the machines can quickly be adapted for in-mold assembly and rotary cube automation. Athena is partnering with SIPA in its PET solutions ("Athena for SIPA"), offering PET preform systems up to 96 cavities. PET systems are sold and serviced by SIPA under the XFORM brand. Athena will be on SIPA's stand at the upcoming DrinkTec and K shows. "The program is very beneficial to a lot of people," says Schad.Athena currently occupies a 40,000-sq-ft facility that houses R&D, labs and assembly, with plans for a 150,000-sq-ft building sometime in 2015. The company currently has 58 employees."Now we have a nucleus that we can introduce," says Schad, "one platform for many different applications, including medical, closures, and preforms all on one platform. There are many excellent machines in the market, which are overkill. We've scaled it down to basics and added pre-engineered options to roll it out to different markets."When asked what he envisions for the new company, Schad says: "Let's assume we win. I'd like to see a private company that my family is holding together with the employees." As always, Robert Schad knows exactly what he wants.
GETTING A QUOTE WITH LK-MOULD IS FREE AND SIMPLE.
FIND MORE OF OUR SERVICES:
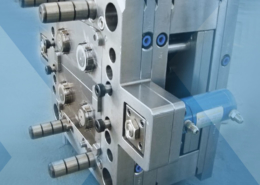
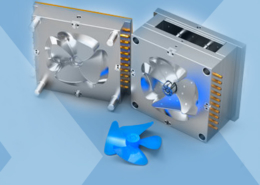
Plastic Molding

Rapid Prototyping
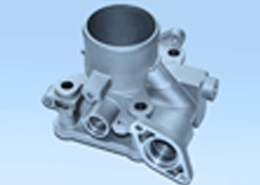
Pressure Die Casting
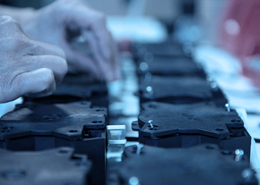
Parts Assembly
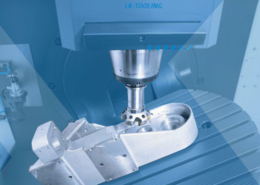