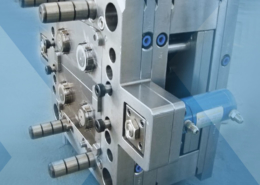
10 Cheap 3D Printing Services to Cut Your Costs - low volume plastic manufacturi
Author:gly Date: 2024-09-30
© 2024 Somerset House TrustRegistered Charity No. 1063640Registered Company Number: 03388137Registered Office Address: Somerset House, Strand, London, WC2R 1LARegistered in England & Wales
The world was about to get hit by this overwhelming force. Supply chains were going to be stretched thin. And the one place we rely on so heavily for manufacturing, China, was about to be locked out of the equation.
Manufacturers of large, complex plastic parts and toolmakers can now test feasibility and implementation at an early project stage. This significantly shortens time to market and avoids costly subsequent errors by identifying and eliminating sources of error early on. Initial customer trials are scheduled to begin shortly.
Funding became available for the project via a Twitter post, through which Nate met Dr Dominic Pimenta, a cardiologist working at an intensive care unit in London and also founder of the charity HEROES, which raises funds to support frontline NHS staff. Dominic quickly found the money to buy 50 3D printers with another ten donated by the printer manufacturer Farnell. These were then set up to produce face shields to protect frontline workers. As Dominic said of the project "For HEROES, it was a no-brainer to be involved. Supporting the NHS frontline with immediacy and impact is why we exist." Working with Nate, he was able to test versions of the face shields on the ground, feeding back on comfort and durability of the various visor versions, so they could be continuously improved.
Until now, large plastic parts have often been manufactured using various processes other than injection molding, which have significant limitations. With the availability of an injection molding machine as large as the duo 5500 combi M in a technical center, extensive possibilities for part and technology development and sampling are now available. This offering reinforces Engel's role as an enabler of new technologies, allowing customers and partners to actively pursue developments in new dimensions and expand injection molding capabilities.
Collaboration and agile working methodologies have been an essential component of making the face shield project a reality. At the start of the project an extended group of Makerversity members and alumni joined Slack channels which Makerversity set up. Here collaborators debated how the group could best support frontline workers, shared insights, designs and operational plans; and ultimately decided what could be meaningfully produced and how to focus the response.
Though Somerset House, its creative community and our visitors have been kept apart over the last few months, Makerversity - a community of emergent maker businesses - have been keeping busy behind the scenes producing much needed PPE for frontline workers.
Nate joined Makeversity a matter of weeks before the pandemic took hold in Europe. He quickly understood that the application of Digital Disruptive Manufacturing, micro-manufacturing using 3D printer ‘farms’, had a new imperative. The Covid-19 outbreak had already forced China into lockdown, a severe crisis was beginning in Italy and the pandemic was about to sweep across Europe. As Nate observed:
Initially developed to mold large parts for the automotive sector, the press is now available for customer trials at the St. Valentin, Austria, technical center.
Tim Burrell-Saward, a long-standing Makerversity member and designer, took the lead in mobilising the many design and engineering collaborators from Makerversity and its extended alumni and friends. In addition, Tim led conversations with experts from SHIELD, an umbrella organisation for various charities and partner platforms, who are passionate about ensuring PPE gets to the frontline. Some of these external collaborators joined Makerversity's Slack groups and Tim, Nate and I joined SHIELD'S various WhatsApp groups.
Makerversity member Nate Petre, who came up with the idea for the PPE 3D print farm, was previously a researcher at Imperial College’s Dyson School of Design Engineering specialising in Digital Disruptive Manufacturing. Backed by funding from NASA, he developed the world’s first fully compostable 3D-printed surfboard. After leaving Imperial, Nate embarked upon extensive global travels, helping small communities 3D print scarce resources, such as water pumps and prosthetic limbs. All this experience was about to become even more relevant.
Face shield production will now move to injection moulding, so it can scale from 1,000 face shields per day to upwards of 10,000 per day. Nate has been evaluating what could be done next with the 3D printers. Possibly even 3D printed transport for NHS workers. Watch this space!
The duo 5500 combi M represents the latest technology in injection molding, said Engel in the announcement. It features two movable (combined and individually operable) horizontal injection units and a combi M injection unit. It is also equipped with two six-axis Engel easix articulated robots for flexible and efficient automation.
For PU applications, two Cannon systems are available — one for small-volume applications and another for high-volume output. A corresponding dosing unit allows for coloring the polyurethane.
There continues to be a shortage of PPE and these projects remain absolutely critical to frontline workers. You can donate to support SHIELD by visiting their website.
The automotive industry increasingly uses larger plastic parts to reduce vehicle weight, improve fuel efficiency, and lower production costs. Plastics offer design flexibility, enhance corrosion resistance, and contribute to the longevity and safety of vehicles. They also allow for the integration of functional elements and reduce the number of individual parts needed. Engel’s new facility supports this trend by enabling the production of larger plastic components.
One of the key challenges of PPE is the fact it is often single use and has a huge impact on the planet. An ICU can get through 30-40 sets of PPE per patient per day, around 9 million units a year, creating vast amounts of waste to be burned or go into landfill. The team focussed their efforts on designing face shields that could be re-used, made from materials that were resilient enough to be disinfected on multiple occasions. The team used reclaimed ocean plastic supplied by Parley, a former collaborator of Nate's, to fabricate the visor part of the face shield; and 3D printing filament used in production was made from a bio-plastic.
Stephen has been with PlasticsToday and its preceding publications Modern Plastics and Injection Molding since 1992, throughout this time based in the Asia Pacific region, including stints in Japan, Australia, and his current location Singapore. His current beat focuses on automotive. Stephen is an avid folding bicycle rider, often taking his bike on overseas business trips, and a proud dachshund owner.
By the time Nate had been at Makerversity a few weeks, there was a well-documented critical shortage of Personal Protective Equipment (PPE) for health and frontline care workers. He was convinced that 3D printing could become a vital part of solving that problem. Nate approached Makerversity to ask us to contribute space to house the 3D printers and provide other support for the project, such as handling media communications. Makerversity's community is all about pioneering creative and technological exploration, with a positive social impact at the heart of our ethos. For us it was completely obvious to support the project as much as we were able.
At the start of the project there were many debates about the areas where members could make the most meaningful difference, particularly given the complexities of official approvals that are needed for medical devices. After discussing everything from gowns to ventilator components, it was decided that the most achievable, high-impact product that could be quickly manufactured was a face shield. After a huge amount of work from the designers and engineers working on the project, a face shield design was created which, via the SHIELD umbrella, is undergoing CE marking.
The company aims to use this machine to explore technologies and mold components in completely new dimensions in collaboration with its customers and partners. The extra-large mold space accommodates molds weighing up to 150 tonnes, with possible shot weights up to a massive 42 kg. The state-of-the-art machine was developed to meet the demands of the automotive industry and technical injection molding and is now available for customer trials.
Makerversity’s community are some of the world’s most pioneering creators and innovators. How important has collaboration been to the success of this project?
With the introduction of the duo 5500 combi M, Engel said it has reinforced its role as a leading hub for testing new technologies and collaborating closely with the industry to promote new injection molding possibilities. The machine allows for the testing and development of existing and new customer projects under real conditions and on neutral ground. This includes tool and material tests as well as the development of new manufacturing technologies.
The new Engel technical center facility covers all application areas for the automotive sector and technical injection molding.
All digital assistance systems from Engel are integrated into the machine control, enabling energy-efficient, sustainable production while optimizing processes.
It was truly remarkable to see what could be achieved virtually and almost instantaneously, by groups of people from diverse organisations and backgrounds. People who had never met each other face-to-face before, but were united by a desire to leverage their respective passions, insights and know-how to make a difference to those in acute need. The SHIELD collaboration received media pick up from the BBC and Wallpaper* the global design authority, amongst others and a fundraising campaign was initiated with virtual input from all partner organisations amidst the depths of lockdown.
Engel reports that it has expanded its technical center in St. Valentin, Austria, with one of the largest injection molding machines from its standard portfolio — the duo 5500 combi M. With a clamping force of 55,000 kN and measuring 32 meters long, 13 meters wide, 6.8 meters high, and weighing 545 tonnes, it is by far the largest technical center machine in the world, according to Engel.
GETTING A QUOTE WITH LK-MOULD IS FREE AND SIMPLE.
FIND MORE OF OUR SERVICES:
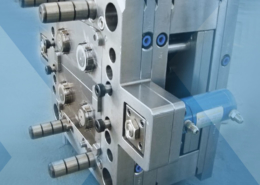
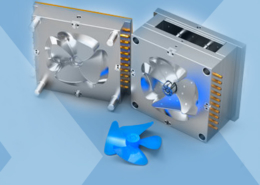
Plastic Molding

Rapid Prototyping
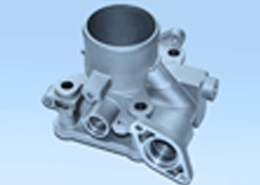
Pressure Die Casting
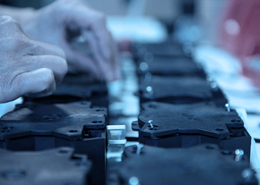
Parts Assembly
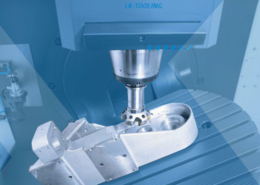