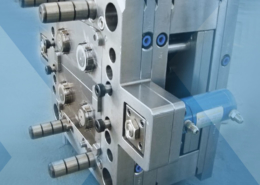
Exploring the World of Medical Device Plastic Injection Molding: Innovating Heal
Author:gly Date: 2024-06-08
Medical device plastic injection molding stands as a cornerstone in the realm of healthcare manufacturing, enabling the production of intricate and reliable components for a diverse range of medical devices. This article delves into the complexities of medical device plastic injection molding, examining its mechanisms, applications, and future prospects.
Introduction: Unveiling the Significance of Medical Device Plastic Injection Molding
Medical device plastic injection molding holds immense importance in the healthcare industry, facilitating the mass production of components essential for medical devices ranging from simple syringes to complex implantable devices. With the increasing demand for high-quality and cost-effective medical solutions, understanding the nuances of plastic injection molding in the medical sector becomes paramount.
Mechanisms and Process Overview
The Injection Molding Process
Medical device plastic injection molding involves the injection of molten thermoplastic materials into a mold cavity under high pressure, where they cool and solidify to form the desired component. The process begins with the feeding of plastic pellets into a heated barrel, where they are melted to a precise temperature. The molten plastic is then injected into a mold cavity, typically made of stainless steel, aluminum, or tool steel. The mold is designed to impart the desired shape and features to the final part, with intricate details and tight tolerances achievable through advanced mold design and manufacturing techniques.
Material Selection and Validation
Selecting the appropriate plastic resin is critical in medical device injection molding, considering factors such as biocompatibility, sterilization compatibility, and mechanical properties. Common medical-grade plastics used in injection molding include polycarbonate (PC), polyethylene (PE), polypropylene (PP), and thermoplastic elastomers (TPE). Material validation involves rigorous testing to ensure compliance with regulatory standards, including biocompatibility assessments, cytotoxicity tests, and chemical resistance evaluations. Additionally, sterilization validation confirms the material's ability to withstand common sterilization methods such as steam autoclaving, ethylene oxide (EtO) sterilization, and gamma irradiation without compromising performance or integrity.
Tight Quality Control and Regulatory Compliance
Maintaining stringent quality control measures is essential in medical device plastic injection molding to ensure the safety and efficacy of the final products. Quality management systems, such as ISO 13485 certification, govern every stage of the manufacturing process, from design and development to production and post-market surveillance. Regulatory compliance with standards set by regulatory bodies such as the FDA (Food and Drug Administration) and CE (Conformité Européenne) mark ensures adherence to safety and performance requirements, mitigating risks associated with product recalls or liability issues.
Applications Across Medical Fields
Medical device plastic injection molding finds extensive applications across various medical specialties, contributing to the development of innovative healthcare solutions.
Implantable Devices and Surgical Instruments
In orthopedics, plastic injection molding is utilized to manufacture implantable devices such as bone screws, plates, and joint prostheses. The ability to produce complex geometries and customize implant designs enhances surgical outcomes and patient satisfaction. Additionally, surgical instruments such as forceps, scalpels, and retractors benefit from injection molding's precision and repeatability, ensuring optimal performance in surgical procedures.
Drug Delivery Systems and Disposable Devices
Plastic injection molding plays a vital role in the production of drug delivery systems such as syringes, vials, and inhalers. Single-use disposable devices, including catheters, tubing sets, and wound care products, are also manufactured through injection molding processes. The scalability and cost-effectiveness of injection molding enable the production of high-volume disposable medical devices essential for infection control and patient safety.
Diagnostic and Monitoring Equipment
Medical diagnostic and monitoring equipment, including blood glucose meters, ultrasound probes, and patient monitors, incorporate components manufactured through plastic injection molding. The ability to integrate features such as fluid channels, sensor housings, and ergonomic grips enhances the functionality and usability of diagnostic devices, contributing to accurate diagnosis and treatment monitoring in clinical settings.
Advancements and Future Directions
Medical device plastic injection molding continues to evolve, driven by advancements in materials, technologies, and manufacturing processes.
Advanced Material Formulations
Research and development efforts focus on the development of advanced plastic materials tailored for specific medical applications, such as bioresorbable polymers for implantable devices and antimicrobial additives for infection control. Novel material formulations offer enhanced properties such as biocompatibility, durability, and ease of processing, expanding the application possibilities for medical device injection molding.
Integration of Additive Manufacturing
The integration of additive manufacturing technologies such as 3D printing complements traditional injection molding processes, enabling rapid prototyping, design iteration, and customization of medical devices. Additive manufacturing techniques offer flexibility in design complexity and material selection, facilitating the development of patient-specific implants and personalized medical solutions.
Conclusion: Shaping the Future of Healthcare Manufacturing
In conclusion, medical device plastic injection molding stands as a cornerstone of healthcare manufacturing, enabling the production of innovative and reliable medical devices essential for patient care. Through precise control of materials, processes, and quality standards, medical device manufacturers can deliver safe, effective, and cost-efficient solutions to healthcare providers and patients worldwide. Embracing advancements in materials science, manufacturing technologies, and regulatory compliance will further propel medical device plastic injection molding into the future, driving continued innovation and excellence in healthcare delivery.
GETTING A QUOTE WITH LK-MOULD IS FREE AND SIMPLE.
FIND MORE OF OUR SERVICES:
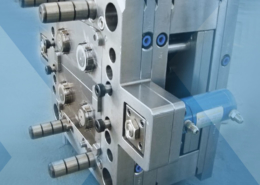
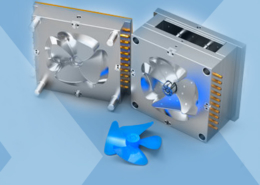
Plastic Molding

Rapid Prototyping
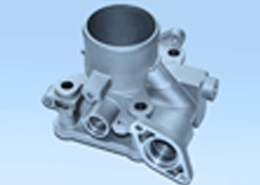
Pressure Die Casting
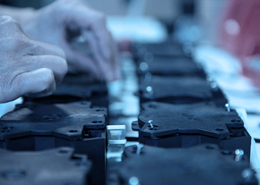
Parts Assembly
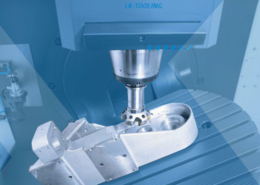