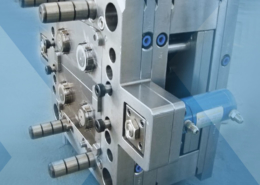
Exploring Medical Device Injection Molding Companies
Author:gly Date: 2024-06-08
Introduction
Medical device injection molding companies play a crucial role in the healthcare industry, providing essential manufacturing services for the production of precision components used in medical devices and equipment. As the demand for innovative medical devices continues to rise, the importance of reliable and experienced injection molding companies cannot be overstated. This article aims to delve into the world of medical device injection molding companies, shedding light on their significance, capabilities, processes, and impact on healthcare innovation.
Background and Significance
Medical device injection molding companies specialize in the production of plastic components and assemblies used in a wide range of medical devices, including diagnostic equipment, surgical instruments, drug delivery systems, and wearable devices. These companies play a vital role in the healthcare ecosystem by providing manufacturers with the expertise, technology, and resources needed to bring medical innovations to market.
The healthcare industry places stringent requirements on the quality, performance, and safety of medical devices, making precision and reliability paramount in manufacturing processes. Injection molding companies catering to the medical sector must adhere to rigorous quality standards and regulatory requirements, ensuring compliance with regulations such as ISO 13485 and FDA guidelines.
Capabilities and Expertise
Medical device injection molding companies possess specialized capabilities and expertise tailored to the unique requirements of the healthcare industry. These include:
Advanced Materials Knowledge
: Expertise in selecting and processing medical-grade materials such as ABS, polycarbonate, silicone, and thermoplastic elastomers, ensuring biocompatibility and regulatory compliance.
Precision Molding Technologies
: Utilization of advanced injection molding technologies, including cleanroom molding, micro molding, overmolding, and insert molding, to produce complex and miniaturized components with tight tolerances.
Quality Assurance and Compliance
: Implementation of comprehensive quality management systems and strict adherence to regulatory standards to ensure the highest levels of product quality, consistency, and safety.
Design for Manufacturability (DFM)
: Collaboration with medical device manufacturers during the product design phase to optimize part geometry, material selection, and manufacturability, reducing time-to-market and overall production costs.
Prototyping and Validation
: Offering rapid prototyping, tooling, and validation services to facilitate product development, design iterations, and regulatory submissions, accelerating the path from concept to commercialization.
Challenges and Solutions
While medical device injection molding offers numerous benefits, it also presents unique challenges that companies must navigate. Some common challenges include:
Stringent Regulatory Requirements
: Compliance with FDA regulations and international standards adds complexity to the manufacturing process. Companies must invest in quality management systems, documentation, and validation protocols to ensure regulatory compliance.
Material Selection and Biocompatibility
: Selecting medical-grade materials with suitable biocompatibility and sterilization properties is crucial for patient safety. Companies must have expertise in material science and access to certified suppliers.
Complex Part Geometry
: Medical devices often feature intricate designs and tight tolerances, requiring advanced molding technologies and tooling capabilities to achieve the desired specifications.
Supply Chain Management
: Managing the supply chain for critical components and materials is essential to ensure continuity of production and minimize the risk of disruptions.
Cost Pressures
: Balancing cost-effectiveness with quality and compliance is a constant challenge in the competitive healthcare market. Companies must optimize manufacturing processes and leverage economies of scale to remain competitive.
Future Trends and Innovations
Looking ahead, medical device injection molding companies are poised to embrace emerging trends and innovations that will shape the future of healthcare manufacturing. These include:
Advanced Materials
: Continued development of medical-grade polymers, bioresorbable materials, and smart polymers with enhanced properties for medical applications.
Additive Manufacturing
: Integration of additive manufacturing technologies such as 3D printing for rapid prototyping, customization, and on-demand production of medical devices.
Digitalization and Automation
: Adoption of digital manufacturing platforms, robotics, and artificial intelligence to optimize production processes, improve efficiency, and reduce time-to-market.
Personalized Medicine
: Customization of medical devices and implants based on patient-specific anatomical data and personalized treatment plans.
Sustainability Initiatives
: Implementation of sustainable manufacturing practices, recycling programs, and eco-friendly materials to reduce environmental impact and promote circular economy principles.
Conclusion
In conclusion, medical device injection molding companies play a critical role in advancing healthcare innovation by providing essential manufacturing services for medical device manufacturers. With specialized capabilities, expertise, and a commitment to quality and compliance, these companies contribute to the development of safe, reliable, and effective medical devices that improve patient outcomes and quality of life. As the healthcare industry continues to evolve, injection molding companies will play an increasingly vital role in driving innovation, efficiency, and sustainability in medical device manufacturing.
GETTING A QUOTE WITH LK-MOULD IS FREE AND SIMPLE.
FIND MORE OF OUR SERVICES:
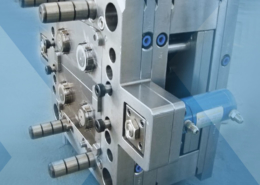
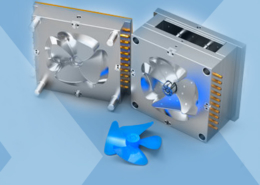
Plastic Molding

Rapid Prototyping
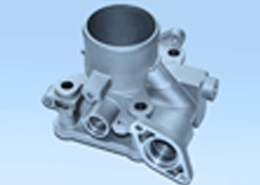
Pressure Die Casting
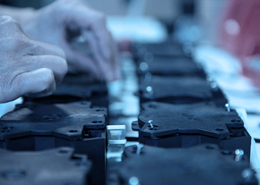
Parts Assembly
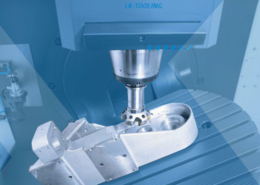