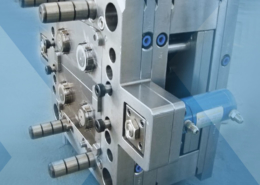
What is Structural Foam Molding? - injection molded foam
Author:gly Date: 2024-10-15
Using a 6 x 4 x 2 model, we can establish a cost analysis for prototype injection mold tooling that compares Fortify, rapid prototyping, and conventional aluminum processes. While it’s important to note that an aluminum mold will last for 1 – 10,000 parts, 3DP tools are much less expensive and provide more flexibility when it comes to design changes or part complexity. For example, injection molded parts with sharp corners, thin ribs, or undercut features will generally be more expensive because it requires a secondary process called EDM machining. Complexity comes free with Fortify, and is nowhere near as costly or problematic.
Prototype injection mold tooling with 3D printing is uniquely advantageous to designers and engineers because it is an inexpensive and fast way to make mistakes. Hard or aluminum tooling is costly and very difficult to alter once the mold has been delivered, making it a logistical and financial nightmare. The data below shows how significant the cost difference is when comparing multiple prototype methods. Not to mention, a dramatic decrease in the product development timeline.
Injection molding can help new firms break into the market with a new product by reducing the time it takes to be up and running. When you choose injection molding as a manufacturing process, you also have the option of working with a turn-key manufacturing partner that will assist you with the tooling, design, and day-to-day production of your product. Here is what you need to know about starting your injection mold molding business.
For the past several decades, 3D printing has become synonymous with rapid prototyping and increased its notoriety as a viable manufacturing alternative. Improvements to printing processes, sintering, finishing, and materials have opened doors to new opportunities that were previously thought to be impossible. For example, the ability to 3D print injection mold tools for short-run prototyping and production projects. This relatively new application is beginning to gain momentum for product developers, tool makers, and contract manufacturers due to several unique advantages.
Those familiar with conventional injection molding (IM) for production purposes are well aware of the inherent benefits associated. An aluminum tool can produce thousands of parts, and steel tools remain the most efficient mass-production method available today. However, the process doesn’t always yield the best results, and tooling mistakes can become economically problematic very quickly. Prototype injection molding with 3D printed tools has become a viable bridge-to-production tool and may be worth considering.
Prototype injection mold tools can be created with a variety of different technologies. As previously presented, it’s possible to use hard tooling, aluminum, or 3D printing depending on resources and availability. To put it into perspective, a normal mold order for a complex part that requires threads, texturing, or undercuts could take approximately 5-8 weeks with an aluminum tool. That’s assuming that there are no alterations or changes within that time to further delay the process.
Chart comparing Fortify’s tooling costs and turnaround time to 3D printing, steel tooling, and aluminum tooling prototyping methods.
Many steel molds are built to process millions of pieces over the course of their lives. Other mold companies prefer Pre-hardened steel molds since they are less wear-resistant and also less expensive solutions for lower volume production. In sections of the mold that require rapid heat evacuation, copper alloy inserts are occasionally employed. This can save cycle time while also increasing the aesthetic quality of the part.
Notice that the first shots with Fortify IM tools are delivered early in Phase 2 while aluminum tooling takes much longer, resulting in parts being shipped at the beginning of Phase 3 (~two weeks later). Assuming you require a single iteration, Fortify can produce parts immediately and have them available in as little as three days. The design finishes on Monday, printing begins overnight then cleaning and curing on Tuesday. On Wednesday, the molds/inserts are coated and the parts are ready in a few hours. Second iteration? Third iteration? No problem, we repeat the process with an identical timeframe.
See how Fortify helped Cogmedix, a MedTech OEM, cut weeks off each design cycle using 3D printing and rapid injection molding technologies.
Prototype injection molding is a bridge-to-production method that minimizes risks and improves product validation well before mass manufacturing. The use of injection molding to prototype is beneficial for several reasons.
Learn more about how Fortify’s mold tooling significantly reduces tooling costs during the new product development process by downloading our free whitepaper
Injection molding is a method of producing shaped objects by injecting material into a mold. It can be done with a variety of materials, but thermoplastic and thermosetting polymers are the most common. A part-making substance will be injected into a heated barrel, mixed, and then pressed into a mold, where it will cool and harden to the shape of the cavity.
The material utilized for the component, the shape and features of the part, the material of the mold, and the properties of the molding machine all require special consideration. The procedure is used to make wire spools, packaging, bottle caps, and automobile parts and components, among other things.
While aluminum molds are less expensive, they are frequently inappropriate for high-volume production with stringent dimensional tolerances. When planned and produced utilizing computer numerical control (CNC) machines or Electrical Discharge Machining (EDM) techniques, aluminum molds may create hundreds of thousands of pieces at a low cost.
The bottom line is the bottom line. Cost and time savings have been referenced several times throughout this guide, and it’s important to address them directly. 3D-printed IM tools are perfect for the low-volume production of prototypes or end-use parts. For any application, it’s important to determine what exactly is low volume and how it pertains to your particular product. This is not easy, so we recommend speaking with an expert to determine what makes the most sense for your application and process.
As a start-up, you will have a lot to think about as you create your final product and work toward the end objective of getting your product to the market. It may feel overwhelming on some days, but finding the proper partner that can help with design, manufacturing, and logistics is very crucial. FOW Mold is one of the best companies in China plastic injection molding industry.
Historically, 3D-printed tools were considered a gimmick and unqualified due to a lack of material capabilities. They were brittle and unable to withstand the high temperatures of molding, leaving many engineers without a viable alternative. That is until Fortify presented a technology that is flexible, inexpensive, and strong enough to mold parts in end-use materials. Ceramic fiber-reinforced materials are revolutionary for the prototype injection mold market that enables a true bridge-to-production tool that will save engineers time and money, without sacrificing quality.
Prototype IM tooling is a cost-efficient way for engineers to shoot end-use materials for true product testing and evaluation. For example, 3D printed mold tools that are reinforced with ceramic fiber and are strong enough to be injected with a variety of thermoplastics that include polycarbonate, nylon 66, ABS and POM, Ultem, GF Ultem, and more. Now, the engineering team can produce 20+ prototypes that are representative of the final product ready to be tested and processed.
Injection molding has witnessed significant expansion in recent years. It has so far emerged as one of the few industries that are growing rapidly, and this is due to the wide range of products and services that they provide. So take a chance and invest in injection molding. Best wishes!
When it comes to creating plastic injection molds, FOW Mold is more than capable of meeting your requirements. For years, the company has been providing plastic injection mold service and assisting in the production of a wide range of products for a variety of industries. The automotive, toy, and plastic storage sectors, as well as the electronics industry, are among these businesses.
The table above compares several methods of producing multiple prototypes or low-volume production. As you can see, rapid prototyping of multiple parts starts to get relatively expensive as the quantity increases, but is still nowhere near the cost of an aluminum tool for less than 100 parts. However, the Fortify IM tool is significantly less expensive and just as capable to mold parts with the appropriate end-use materials. In fact, an engineering team can redesign a prototype injection mold tool with Fortify over 15 times for the same cost as a singular aluminum mold.
If you’d like to learn more about how you can maximize prototype injection molding with Fortify, get in touch with our experts.
Let’s face it, no one designs or prototypes the perfect part right off the bat. What’s more problematic to your new product development (NPD) lifecycle—wasted time or wasted money? The real answer is both. Therefore, adopting a prototype injection molding process will provide real answers to production problems that typically occur late in the game. Thus eliminating costly redesigns or worse, production mishaps.
Hardened or pre-hardened steel, aluminum, and beryllium-copper alloy are used to make plastic injection molds. Steel molds are more expensive, however, they are generally favored due to their long endurance. Others prefer hardened steel molds majorly in terms of wear resistance and longevity.
Product development relies on internal and external feedback to make improvements. Having access to a small batch of product parts with prototype IM tooling enables beta customers and remote engineering teams immediate access to the product. This is ideal to enhance customer relationships or international organizations with multiple facilities. No delays or hold-ups due to part scarcity.
ACIS®, Autodesk Inventor®, CATIA® V5,Creo™ Parametric, IGES, Parasolid®, Pro/ENGINEER®,Siemens PLM Software’s NX™, SolidEdge®, SolidWorks®, STEP
Plastic Injection molding is the most frequent process for producing plastic parts since it allows for large quantities of the same thing to be produced. Injection molding can be used in the following applications:
FOW Mold understands the necessity of having a variety of injection molding alternatives when creating plastic injection molds. Industries require high-quality molds in order to mass-produce products quickly. As a result, they provide a variety of mold-making procedures.
Inject a variety of thermoplastics that include polycarbonate, nylon 66, ABS, and POM from a Fortify mold that is ~90% cheaper than aluminum. The conventional IM tooling process can take up to eight weeks to get parts delivered, imagine having those same parts within days. Fail fast and fail often by quickly redesigning prototype IM tools and testing parts immediately, getting to market faster than ever before.
However, Fortify offers a unique path toward a much faster and more flexible solution. The Gantt chart below shows a traditional 3-phase injection molding process. Presuming that the product development (Phase one) takes approximately three weeks, we can determine the next steps in the process by comparing aluminum vs. Fortify molds.
GETTING A QUOTE WITH LK-MOULD IS FREE AND SIMPLE.
FIND MORE OF OUR SERVICES:
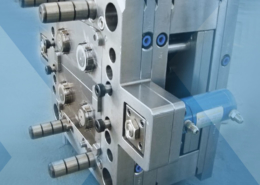
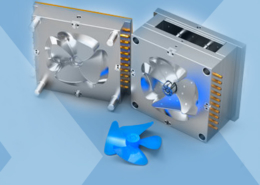
Plastic Molding

Rapid Prototyping
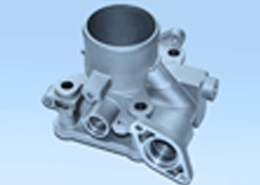
Pressure Die Casting
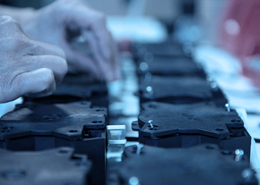
Parts Assembly
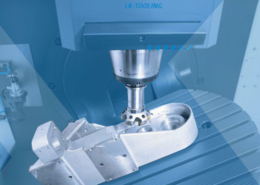