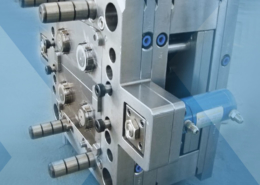
What is shot size in injection molding? - shot mould
Author:gly Date: 2024-10-15
Two-shot is carried out within a single tool, allowing for lower tolerances than other molding processes, a high level of accuracy and repeat-ability, and reduced scrap rates.
When a major automotive OEM failed a side impact crash test, they relied on their Tier 1 supplier and us to develop a two-shot injection molding solution to reinforce the vehicle’s frame.
Two-shot injection molding allows for the creation of complex mold designs that incorporate multiple materials for functionality that cannot be achieved through other molding processes.
Maybe you’ve been turned off by a manufacturer’s quality or delivery issues? We’re here to tell you that you deserve better!
The first is similar to traditional injection molding: A shot of resin is injected into a mold and cooled to form a solid part. In the second phase, the just-molded part is transferred to a second mold via a rotating platen or a robotic arm, and receives the second shot of resin – in, through or around certain parts of the first molded part, depending on the design. The two plastic resins then form a molecular bond and the multi-resin molded part is cooled and ejected.
Two-shot molding allows multiple components to be molded with a single tool, reducing the amount of labor needed to run your parts and eliminating the need to weld or join components after the molding process.
When tolerances and on-time-delivery are important, OEMs choose us for two-shot injection molded parts. We’re more than a manufacturer. We’re problem-solvers, working both with customers and vendors to build functionality, safety, and efficiency into everything we produce.
Two-shot injection molding reduces the number of components in a finished assembly, eliminating an average of $40K in development, engineering, and validation costs associated with each additional part number.
From consumer goods to construction, two-shot molded components are used in nearly every industry, but are most commonly found in applications requiring high functionality.
Compared to other methods of plastic molding, two-shot is ultimately a more cost-efficient way of producing an assembly with multiple components. Here’s why:
The customer is a Tier 1 international automotive supplier with an emphasis on innovation and technology. The company’s products include automotive exteriors, closures, roof systems, and seating – to name a few.
You can rest assured you’re getting the quality you need at a competitive market price when you choose us for your two-shot molding solutions.
It requires high levels of technical expertise and attention to detail, and even the smallest mistakes can cost big money, especially in high-volume production scenarios. That’s why it’s critical to find a highly capable supplier. Look for excellent supplier quality scorecards, defined processes to mitigate against flash, flow lines, and short-shots, and contingency plans to expand capacity as your business and your two-shot molding needs grow. Once you find a supplier, involve them early on in the design phase of your part. They can identify potential problem areas and engineer value into your product.
Two-shot injection molding is the ideal plastic molding process for complex, multi-color, and multi-material plastic products, especially in high-volume production scenarios.
If you’re new to two-shot plastic injection molding, you might think it is more complex, more expensive, or more time consuming than other plastic molding processes. Taken alone, those may be true, but two-shot also creates considerable functionality and cost savings.
GETTING A QUOTE WITH LK-MOULD IS FREE AND SIMPLE.
FIND MORE OF OUR SERVICES:
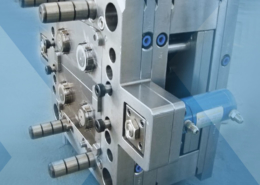
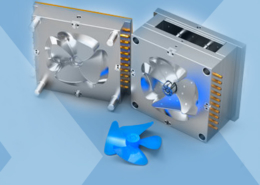
Plastic Molding

Rapid Prototyping
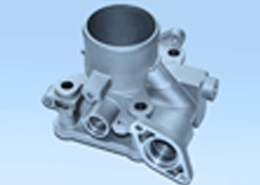
Pressure Die Casting
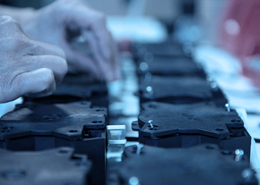
Parts Assembly
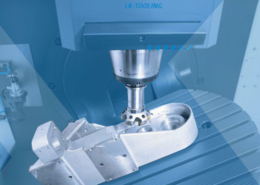