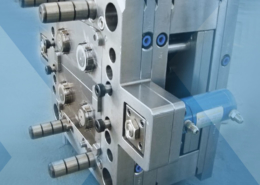
Injection Moulding for Dummies: A Beginner's Guide to Manufacturing Magic
Author:gly Date: 2024-06-08
Welcome to the fascinating world of injection moulding, where creativity meets precision to shape the products we use every day. Whether you're new to manufacturing or a seasoned professional, understanding the basics of injection moulding is essential. In this beginner's guide, we'll unravel the mysteries of injection moulding, exploring its principles, processes, applications, and future prospects.
Demystifying Injection Moulding
Injection moulding is a manufacturing process used to produce plastic parts by injecting molten material into a mould cavity. It's one of the most versatile and cost-effective methods for mass-producing complex components with high precision and consistency. From automotive parts and medical devices to consumer electronics and household items, injection moulding shapes the world around us.
The Magic Behind the Process
At the heart of injection moulding is the injection moulding machine, which consists of a hopper, barrel, screw, and mould. The process begins with the raw material, usually in the form of pellets or granules, being fed into the hopper and transported to the barrel. Inside the barrel, the material is heated and melted by the screw, forming a viscous liquid known as the melt.
Once the melt reaches the desired temperature and consistency, it's injected into the mould cavity under high pressure. The mould, typically made of hardened steel, contains the negative shape of the desired part. As the melt cools and solidifies inside the mould, it takes on the shape of the cavity, creating a precise replica of the desired part.
Applications Across Industries
The applications of injection moulding are virtually limitless, spanning across numerous industries and sectors. In the automotive industry, injection moulding is used to produce components such as bumpers, dashboards, and interior trims with complex geometries and superior finish. In the medical field, it's employed to manufacture devices like syringes, IV catheters, and surgical instruments with stringent quality and regulatory requirements.
Moreover, in the consumer electronics sector, injection moulding enables the production of casings, connectors, and housings for devices such as smartphones, tablets, and laptops. Its ability to produce parts with tight tolerances and intricate features makes it ideal for applications where precision and consistency are paramount.
Future Trends and Innovations
Looking ahead, the future of injection moulding is bright, with ongoing advancements in materials, technologies, and processes. Additive manufacturing techniques such as 3D printing are revolutionizing the way moulds are designed and produced, offering unprecedented flexibility and customization. Moreover, the integration of digitalization, automation, and artificial intelligence is transforming the injection moulding landscape, making it more efficient, sustainable, and responsive to market demands.
Conclusion
In conclusion, injection moulding is a cornerstone of modern manufacturing, driving innovation and shaping the products we rely on every day. By understanding the principles and processes of injection moulding, we can unlock new possibilities and unleash our creativity in designing the future. Whether you're a novice or an expert, the world of injection moulding offers endless opportunities for exploration and growth.
GETTING A QUOTE WITH LK-MOULD IS FREE AND SIMPLE.
FIND MORE OF OUR SERVICES:
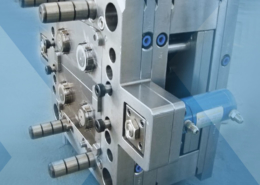
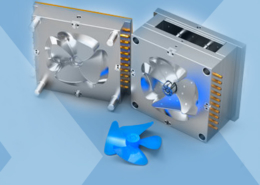
Plastic Molding

Rapid Prototyping
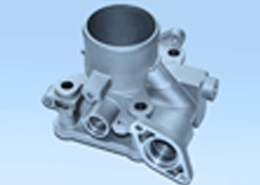
Pressure Die Casting
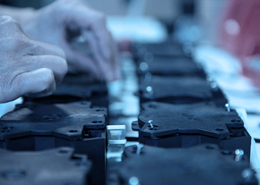
Parts Assembly
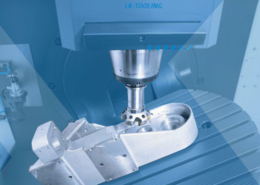