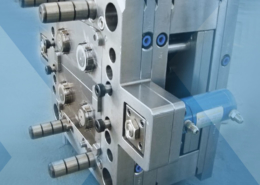
The World of Injection Moulding Business: A Comprehensive Overview
Author:gly Date: 2024-06-08
Injection moulding business stands at the forefront of modern manufacturing, driving innovation, efficiency, and versatility across industries worldwide. This article delves into the intricate landscape of injection moulding, unraveling its significance, processes, applications, challenges, and future prospects.
The Essence of Injection Moulding
Injection moulding epitomizes precision manufacturing, leveraging thermoplastics, thermosetting polymers, or elastomers to create intricate components with unparalleled accuracy. Its essence lies in the transformative power to shape raw materials into complex geometries, catering to diverse industry demands.
Injection moulding's journey traces back to the late 19th century, evolving from manual processes to automated systems, revolutionizing mass production and spurring technological advancements.
Process Overview and Technologies
At its core, injection moulding entails injecting molten material into a mould cavity under high pressure, followed by cooling and solidification. The process encompasses several key stages: material feeding, melting, injection, cooling, and ejection.
Modern injection moulding technologies encompass a spectrum of approaches, including:
Conventional Injection Moulding:
Employing hydraulic, electric, or hybrid machines for standard production.
Micro Injection Moulding:
Catering to miniature and precise components, driving innovation in electronics and medical devices.
Multi-material Injection Moulding:
Facilitating the integration of diverse materials within a single component, enhancing functionality and performance.
Additive Manufacturing:
Fusion of injection moulding with 3D printing, unlocking new design possibilities and reducing time-to-market.
Applications Across Industries
Injection moulding's versatility transcends industries, permeating automotive, aerospace, healthcare, consumer goods, and beyond. Key applications include:
Automotive:
Production of interior components, exterior body parts, and intricate engine parts.
Medical:
Manufacturing of disposable devices, surgical instruments, and drug delivery systems, adhering to stringent regulatory standards.
Packaging:
Crafting lightweight and durable packaging solutions, optimizing product protection and shelf appeal.
Electronics:
Fabrication of enclosures, connectors, and intricate circuitry components, meeting the demands of miniaturization and connectivity.
Consumer Goods:
Creation of household appliances, toys, and personal care products, blending aesthetics with functionality.
Challenges and Innovations
Despite its myriad benefits, injection moulding encounters challenges, including:
Material Selection:
Balancing properties such as strength, durability, and cost-effectiveness.
Design Complexity:
Addressing intricacies in part geometry and tooling requirements.
Environmental Impact:
Mitigating plastic waste through recyclability and sustainable materials.
Innovations such as advanced simulation software, real-time monitoring systems, and sustainable material alternatives pave the path for overcoming these challenges, fostering a more resilient and eco-conscious industry.
Conclusion: Pioneering the Future of Manufacturing
Injection moulding business stands as a cornerstone of modern manufacturing, driving innovation, efficiency, and sustainability across diverse sectors. Its evolution from conventional processes to cutting-edge technologies underscores its adaptability and resilience in an ever-changing landscape.
As we navigate towards a future defined by digitalization, sustainability, and customization, injection moulding remains poised to lead the charge, shaping tomorrow's products and industries. Embracing innovation, collaboration, and sustainability will be paramount in realizing the full potential of injection moulding and charting a course towards a more prosperous and sustainable future.
GETTING A QUOTE WITH LK-MOULD IS FREE AND SIMPLE.
FIND MORE OF OUR SERVICES:
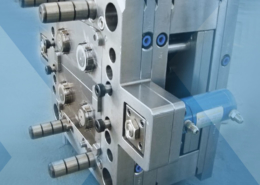
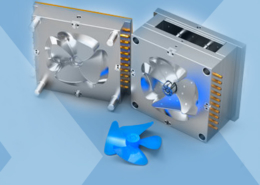
Plastic Molding

Rapid Prototyping
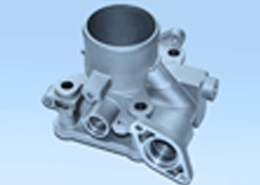
Pressure Die Casting
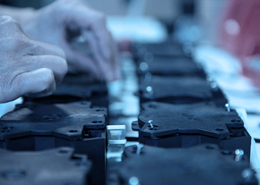
Parts Assembly
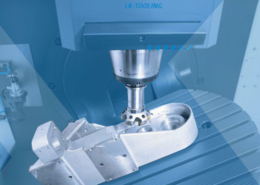