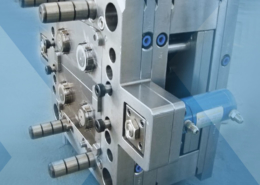
What is 2k injection molding, and how does it work? - Ace-Mold. - 2k plastic inj
Author:gly Date: 2024-10-15
Injection molded parts can undergo a variety of post-processing operations, such as assembly, machining, laser marking, pad printing or surface finishing, to meet the exact requirements of the medical device.
Meeting stringent regulatory requirements is a non-negotiable in the medical device industry. Injection molding excels in this regard. The ability to use FDA-approved materials and consistently produce parts that meet these standards ensures compliance from the outset.
We have been serving the medical industry for nearly 40 years, specializing in handling complex, multi-part programs and medical device molding for a variety of customers. Our direct contact with doctors and other medical professionals gives us insight into their needs and helps define and assist with final product solutions.
Mold and microbial inhibitors are sometimes used in buildings where water damage has been sustained or where general humidity and moisture can result in mold growth. Such products have varying uses. They may be used in new construction or existing buildings as either cleaners to treat construction surfaces or primers for latex paints to remove mold, reduce mold growth or create a microbial barrier for mold prevention.
In many cases, our medical device customers look to process validation to ensure quality parts. After all, patients lives depend on PTI to deliver high quality parts each and every time.
Having served the medical industry for nearly 40 years, we understand medical device manufacturing. Plastic Injection Molding remains one of the best manufacturing methods for achieving precision and cost-efficiency as well as maintaining patient safety.
Some of these products contain incompatible nonionic surfactants (i.e., synthetic detergents) that may cause environmental stress cracking when contact is made with CPVC sprinkler systems. This typically occurs on fittings, although pipes may occasionally be affected.
Process validation is the best way to ensure the production of safe parts, to reduce rejection rates, to prevent part failures in the field and to ensure the part meets with application, specification and regulatory obligations.
This provides yet another example of why the FBC System Compatible Program – developed by Lubrizol for FlowGuard®, BlazeMaster®, Corzan® and TempRite® Technology CPVC piping systems – should be used as a reference tool exclusively to these products and not those of other manufacturers. Only Lubrizol CPVC. Every brand of CPVC piping is made with unique compounds, some of which may contain resins with different molecular weights and varying chlorine content.
To learn more about mold inhibitors and other ancillary construction products and how they may – or may not be – used in conjunction with BlazeMaster CPVC, visit the FBC System Compatible Program.
Lubrizol Advanced Material’s FBCTM System Compatible program lists four mold inhibitor products under the Cleaners & Disinfectants category that are compatible with BlazeMaster CPVC. Each product links back to the manufacturer’s product page, and all display the FBC System Compatible Program logo either on the product page or the product’s data sheet. All four of these products may be used with confidence in a fire sprinkler system that utilizes BlazeMaster CPVC.
Injection molding produces parts with a high level of structural integrity, ensuring they can withstand the rigors of their intended application. These parts are less prone to defects and offer superior performance over their lifecycle.
Of course, if you encounter a mold inhibitor product that is not listed on either page, it is always best to err on the side of caution and assume that it is not compatible with BlazeMaster CPVC.
At PTI, we collaborate with you to achieve the best possible design for manufacturability. In fact, we have a FREE guide to help you with this.
Injection molding is scalable, which means it can cater to a variety of production volumes, from small-scale prototypes to mass production. This scalability offers manufacturers the flexibility to meet different market demands.
It is interesting to note that one of the products listed as compatible with BlazeMaster CPVC – Anabec Advanced Cleaning Solution Plus – only recommend their products for use with BlazeMaster CPVC.
There’s also a page that lists incompatible products. On this list are two mold inhibitor products that should never be used with BlazeMaster CPVC. Rationale is provided for each. Either the products were:
Furthermore, we have over 5,000 square feet of controlled environment space. This segregated area is temperature controlled and pressurized, and can accommodate part decorating, assembly and packaging needs.
When installing or specifying a BlazeMaster® Fire Protection System, it is always a good idea to understand which ancillary products are being used that may come into contact with the piping. This will ensure system integrity for years to come. If an installation is taking place in an area that has recently seen water damage or is prone to high humidity or moisture, the use of mold inhibitor products should be considered prior to installation or during the specification stage.
Many medical devices must be in direct contact with the human body. Injection molding allows manufacturers to choose biocompatible materials, ensuring patient safety. These materials can be sterilized without affecting their properties, making them suitable for a wide range of medical applications.
Injection molding for medical devices represents the perfect synergy of precision engineering and advanced manufacturing technology. Its benefits, from precision and consistency to cost-efficiency and regulatory compliance, make it a top choice for design engineers and medical device manufacturers. The process empowers engineers to innovate, create intricate components, and bring lifesaving devices to market faster than ever before. The future of medical device manufacturing is being molded with precision, and injection molding is at the forefront of this revolution.
PTI Engineered Plastics provides medical device manufacturers with full-service advanced product development delivered in a compressed timeframe. With superior design for manufacturability, tooling, and molding capabilities, PTI turns product visions into reality and gets your product to market first.
By: Mark Knurek on July 23rd, 2019
At PTI, we have over 16,000 square feet of ISO Class 8 cleanroom space that we utilize in our injection molding process to ensure as little contamination as possible. We adhere to strict protocols that meet the demands the medical industry requiring ISO 14644 Cleanroom specifications, including bioburden and electrostatic discharge (ESD).
That’s one advantage of working with us – we take the guesswork out of which construction products may be used and which may not.
One of the most significant advantages of injection molding is its design flexibility. Engineers can create complex, customized components with minimal tooling changes. This adaptability is essential in a field where the demand for innovative and unique medical devices is ever-expanding.
The high initial tooling costs can be a barrier to entry for some manufacturers. However, once the molds are in place, injection molding is incredibly cost-effective for large production runs. The ability to produce a large number of parts in a short time reduces unit costs significantly, making it an ideal choice for mass production.
Injection molding allows medical design engineers the freedom to design complex or intricate parts, a vast selection of suitable materials and the consistency to produce both low and high volumes of devices.
Then find out why not all orange piping is as reliable as BlazeMaster Fire Protection Systems by downloading the free Brand Comparison Guide.
Mold Design is a crucial step in the injection molding process. Once you’ve finalized your part in CAD software for fit and function, it must then be transformed into a design for molding to ensure the capture of all the specified details. In some cases, certain features of the part design may not be manufacturable via the injection molding process.
All ancillary products listed as compatible and non-compatible with BlazeMaster CPVC on the FBC System Compatible Program website and apps have been specifically tested for compatibility with Lubrizol CPVC piping only – never with any other brand of CPVC.
With streamlined production processes, injection molding can significantly reduce time-to-market for medical devices. This is crucial in a rapidly evolving industry where innovations can make a significant impact on patient care and outcomes.
Process Validation as defined by the FDA is “The collection and evaluation of data, from the process design stage throughout production, which establishes scientific evidence that a process is capable of consistently delivering quality products.”
The injection molding process generates minimal material waste compared to other manufacturing methods. This not only contributes to cost savings but also aligns with the increasing focus on sustainable and environmentally friendly manufacturing practices.
Injection molding offers unmatched precision and consistency in the production of medical device components. The process allows for intricate designs and tight tolerances, ensuring that each part is identical to the next. This uniformity is crucial in the medical field, where reliability and precision are paramount.
Some of the most common materials used in medical devices are: Polypropylene, ABS, Polyurethane, Polyvinylchloride, Polycarbonate, Polystyrene, Polysulfone, Acetal and Polyethylene.
Careful selection of materials is extremely important within the medical industry. Materials must meet FDA and other regulatory standards, ensuring patient safety, biocompatibility, sterilizability and durability. As Injection molding allows for a vast selection of both thermoplastic and thermoset materials to choose from, there is certain to be a material suitable for just about any application.
GETTING A QUOTE WITH LK-MOULD IS FREE AND SIMPLE.
FIND MORE OF OUR SERVICES:
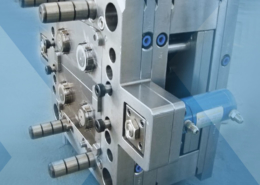
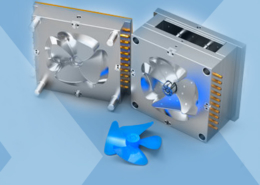
Plastic Molding

Rapid Prototyping
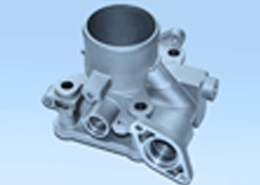
Pressure Die Casting
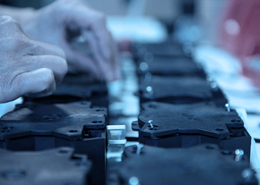
Parts Assembly
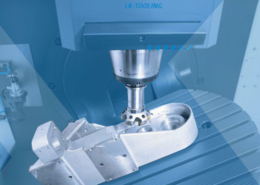